What is it like to build in Antarctica?
28 April 2023
Construction contractor BAM Nuttall, engineer Ramboll, and designers Sweco are working with the British Antarctic Survey (BAS) on a £300 million (US$372 million) modernisation of BAS buildings in the Antarctic. Currently, the team is working on the construction of the new ‘Discovery Building’ at Rothera, the largest BAS research station, with work expected to complete in 2024.
As David Brand, senior project manager, BAS, and Robert Kerr, project manager and site agent, BAM, come to the end of another summer construction season, they tell International Construction about the project and what it is like to work in such unforgiving conditions.
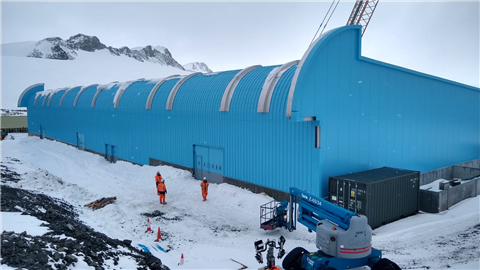
How much longer will construction be able to go on this season before it gets too cold? When is the next phase of work and what will be involved?
Construction was completed in mid-April before the site is winterised once again and the final demobilisation port call by [polar research vessel] RRS Sir David Attenborough arrives at the end of the month. Beyond April, the amount of daylight reduces substantially, temperatures drop regularly below freezing point, and the sea ice begins to form preventing ship calls. Flights had ceased a month earlier in Mid-March.
With the building weathertight, works will focus more on the internal fit-out with us starting work again in November for the start of another six-month construction season. The 2023-24 season is a hugely important season for us as we look to complete the M&E fit-out, start the final finishes, as well as complete the external work such as glazing and erecting the wind deflector. We will also complete the Site Wide Services (SWS) and connect the services up to the legacy buildings. It’s an ambitious timetable, but one that allows us to commission and handover the Discovery Building in the 2024-25 Season.”
What have you had to consider when designing a building in such a harsh environment?
We designed for a range of environmental conditions including high levels of snowfall up to a single storey height, high 38m/s wind speeds with gusts up to 45m/s, freezing and thawing of ice both above and below ground, and sharp drops in temperature to -35oC (-31oF).
Focus has been on the thermal performance of the external building envelope (cladding panels) and ensuring sufficient thermal breaks and vibration dampers are included in the design. The design concentrated on the reuse of heat with our power generation and ventilation systems so that we reduce the energy demand on fuel and heating fresh circulated air.”
What solutions have you come up with to create a building that can withstand the conditions, particularly when it comes to the exterior?
The Discovery Building is positioned and orientated in an east-west axis to maximise the wind scour from the predominant north-easterly wind across
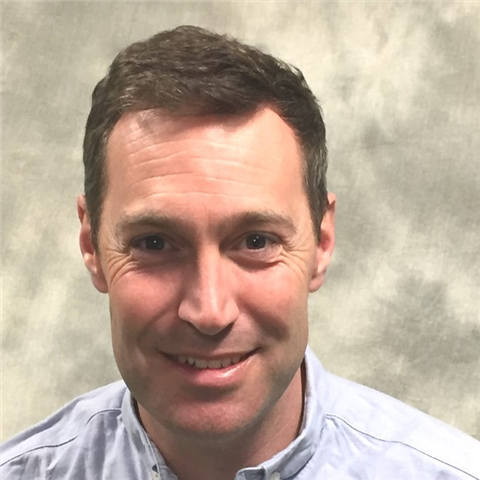
the 90m length of the north face of the building.
The movement of people and vehicles between the building and its exterior environs is concentrated on the north side of the building, hence the number of door openings on the north elevation, making the best use of the wind scour to clear snow from this side of the building.
The building has 71 ground anchors which enable it to be secured to the ground against the wind forces acting on the main frame whilst maintaining its transient characteristic required by the Polar Protocol. The 5o pitch of the roof has proven to be the best angle for enabling wind scour, and penetrations through the roof have been avoided with a flue tower on the east side of the building to avoid snow build-up. A curved steel wind deflector along the southern roof elevation is designed to redirect wind down the sheltered side of the building to clear snow from the immediate footprint of the building.
There must be limitations in terms of availability and delivery of materials and equipment. How do you manage this process?
It is a major logistical undertaking to get every single item required to construct a building of this magnitude at the other end of the world - there is no Keyline (https://www.keyline.co.uk/) along the road unfortunately! All materials to construct the building were shipped via two commercial vessels, which were loaded in Teesport in the UK. Collaboration between clients, designers and supply chain partners has been the key to success. The project has benefitted immensely by engaging project partners at the front end of the design development, leaving no stone unturned.”
How much prefabrication and modular construction has been involved?
Programme reassurance is critical in Rothera - as we have fixed construction windows to deliver works in. The project team have managed this by undertaking trial erections and pre-assemblies ahead of shipping.
The control tower - which was installed this year - was trial assembled at the steelwork fabricators’ yard. The roof section was fabricated at the port of shipping in the UK which ensured the quality of the product was achieved whilst also removing approximately 2-3 weeks of work from the site construction programme.
In addition, GA Barnies, the M&E contractor, have prefabricated and modularised services for the plant rooms, corridors and congested room spaces. This prefabrication process has been essential for this project. Not only has it reduced waste, saved time on site and maintained quality, it has allowed us to pre-commission, test systems and provide essential training with the client in the UK prior to shipping. This allowed us to iron out any issues, make amendments easily, avoid missing parts on station and streamline the handover process on station.
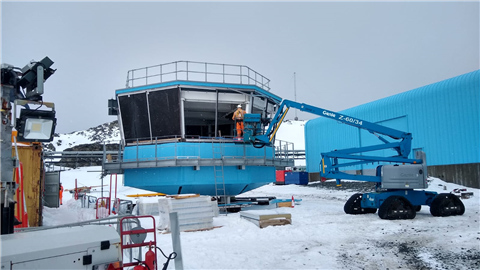
Are there any considerations you have to make for storing materials, given the conditions?
Logistically, storing materials is a real challenge due to both space and climatic considerations. Materials are generally packed into containers for shipping and for ease of handling they remain within containers on site.
As to be expected, Antarctica can be incredibly cold with temperatures plummeting to -35oC (-31oF) in the middle of winter. Material selection was discussed at length during the design phase including its suitability for long-term storage. Where materials need to be stored at minimum temperatures, we have shipped a number of heated stores.
How do you aim to make the building net zero?
“The construction of the Discovery Building and the station’s new Site Wide Services (SWS) is on course to decrease fuel use on Station by 20-30% [depending on how BAS demand changes under the new operational model]. The project achieves this through reduction in both operational demand and more efficient supply.
Demand is reduced by a smart use of the Building Management System (BMS) that assesses sensor data on the occupancy of spaces to reduce the air exchanges by the ventilation system, and hence decreases the volume of cold air requiring heating. The building is also zoned enabling areas to be winterised when occupancy is at its smallest. The ventilation system has been designed to efficiently recover heat from dirty warm air in the ventilation system. With energy supply, the power generation system has been developed to maximise energy efficiency through a blend of heat recovery generators and solar voltaic renewables.
You have an on-site construction team of 54. How experienced are they with working in conditions like this and what is the atmosphere like in the team?
An incredible amount of time and effort is required to ensure that the team selected are both professionally skilled to undertake the complex works but also capable of working and living together in Rothera.
This is our fifth year of construction in Rothera, and such is the attraction that almost a tenth of the team have completed every season. 60-70% of the construction team this year are also returners, which ensures we have a good level of experience and knowledge within the team.
Ensuring we have a good balance of new and experienced members within the team keeps things fresh, adds to the depth of the team and allows the knowledge gained to be passed on.
The atmosphere within the team is currently very high, after a long but incredibly rewarding season, the Sir David Attenborough is moored up and preparing to take some members of the construction team on the first leg of the journey home.”
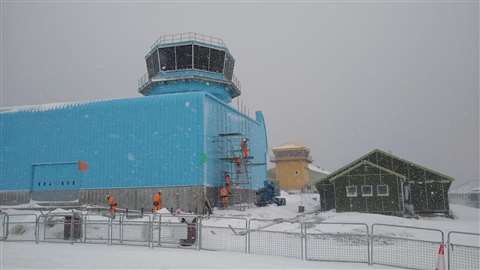
Can you tell us about one particular high and one particular low that you and the team have experienced so far?
A particular high the team has experienced would be the landing of the communications tower in March this year. A significant milestone in the construction programme, it really was the “cherry on top” and marks the transition from external to internal works…a new chapter in the Antarctic Infrastructure Modernisation Programme.
Ultimately, the low point in the project was the delay to completion because of the global pandemic. The Covid-19 pandemic made the preparations for the second construction season very challenging. Despite worldwide lockdowns, the strength of the partnership prevailed by maintaining continuity in delivery. The key to overcoming the challenge was the adaptability, perseverance, and professionalism of all partners to work collaboratively to tackle the challenge head on.
Robert, you are completing your second season in the Antarctic and have spent approaching five months in Rothera. How have you personally found working in such a remote location?
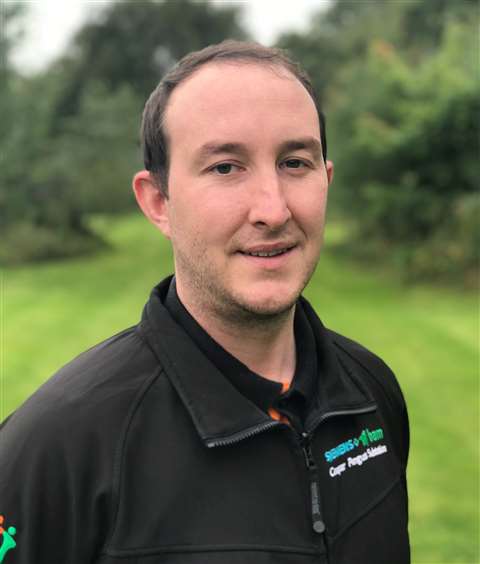
I would be lying if I said I wasn’t looking forward to getting back to my family and home comforts!
While it is a challenging place to work in, I am incredibly grateful for the opportunity.
The term ‘once in a lifetime’ is regularly overused - not in this case - it is not every day you are constructing a state-of-the-art building with penguins toddling through the site, or humpbacks popping up in the bay…
Working in Rothera has changed my life, for the better, both personally and professionally.
MAGAZINE
NEWSLETTER
CONNECT WITH THE TEAM
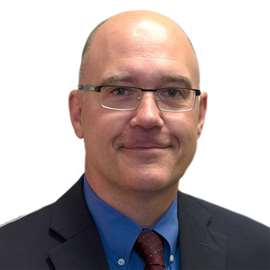
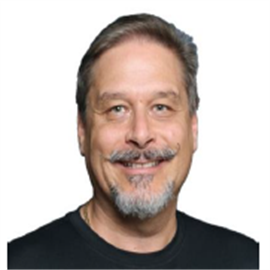
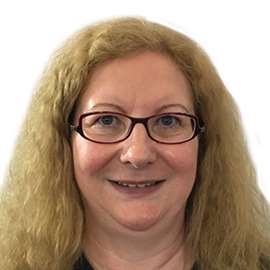