Cornerstones of Compression: Evolution of Air Compressors
11 November 2024
This continues a series of Cornerstones of Compression corollary articles that provide an historical look at the industries that drove the invention and technological evolution of compressors and that supported the growth and development of the industries that depended on them. This issue continues the evolution of air compressors for mining, construction and manufacturing.
Reciprocating Compressors Evolve To Meet Growing Use of Compressed Air
As steam-powered rock drills gave way to more efficient air-powered rock drills, reciprocating air compressors evolved quickly. In the U.S., the Rand & Waring Drill and Compressor Company introduced the first Rand air compressor for powering rock drills in 1872. At about the same time, inventor and businessman Simon Ingersoll started the Ingersoll Rock Drill Company, continuing the research and development of reciprocating air compressors and rock drills. Both New York City based companies developed new and larger compressor models, expanding rapidly and becoming the two most prominent manufacturers of air compressors. Almost all of the air compressors in this period were driven by steam engines. But, in addition to integral steam-driven, both manufacturers developed belt-driven models such as the large pre-1900 Rand duplex air compressor in Fig. 1. These took advantage of the growing use of both DC and AC electric power for motor drives in the 1890s and beyond.

As early as the 1890s, both Ingersoll-Sargeant and Rand Drill had designs for high-pressure compressors producing 1000 psig (69.0 bar) for early uses such as compressed air guns and locomotives. During the 1890s, both companies manufactured virtually identical equipment for mining and construction, however their marketing territories were different. As their territories began to overlap, rivalry increased, and in 1905, they merged to form the famous Ingersoll-Rand Company, that would lead the air compressor industry for much of the next century.
The Westinghouse Machine Company began building small air compressors for the railway air brake industry in the mid-1880s and it produced small starting air compressors for its gas and oil engines, which required 100 to 150 psig (7 to 10 bar) air injected into the power cylinders for starting. By the early 1890s, some steam engine-driven compressors, such as the one shown in Fig. 2, were being produced by Westinghouse for industrial applications.
With the birth of the industrial age, air compression gained new uses in the field of manufacturing. In 1888, Viktor Popp, an Austrian engineer, developed Europe’s first compressed air-powered plant, starting at 2000 hp (1500 kW). Located in Paris, the plant had expanded to 24,000 hp (18,000 kW) by 1891. Soon, other inventors were patenting a variety of tools and accessories that ran on compressed air. The city of Paris became the center of a raging debate whether compressed air would overtake electricity as the technology moving forward.
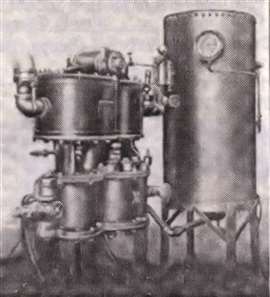
The Norwalk Iron Works, later the Norwalk Compressor Company, of Norwalk, Connecticut patented a one-stage double-acting air compressor in 1876, followed by a patent for the world’s first multiple-stage air compressor in 1881. An early Norwalk two-stage air compressor is shown in Fig. 3 with an intercooler between cylinders. The linkage on the side mechanically actuated the compressor valves, similar to the technology used for steam engines at the time.
The first air compressors were known as “wet compressors,” with water in direct contact with the air for cooling during compression. Water was originally introduced in a stream with the air, later being injected as a spray. However, the presence of water in a reciprocating compressor air cylinder was extremely objectionable, both for mechanical and theoretical reasons. Soon after John Waring’s invention of a water-jacketed cylinder (see last month’s edition), Norwalk also abandoned the direct contact system and developed cylinders and cylinder heads with water jackets for surface cooling. They even experimented with circulating water through a hollow piston rod to the piston. However, piston cooling was difficult and soon eliminated.
These and other advances in compressor technology soon made Norwalk an early industry leader, considered so innovative that it was featured on the cover of the June 12, 1880 issue of Scientific American. In 1885 the U.S. Navy used Norwalk compressors to test a ship-mounted gun that would fire shells with compressed air. An 1888 catalog stated that Norwalk compressors could produce pressures of 5000 psig (345 bar), believed to be the highest air pressure ever attained by any practical commercial machine to that time. And in 1891, an international commission meeting in London awarded a $1000 prize to Norwalk Iron Works for the most advanced compressor in the world.
As the 20th century approached, a number of large and many small air compressor manufacturers emerged. The Laidlaw-Dunn-Gordon Company of Cincinnati and Hamilton, Ohio began making air compressors in c.1885. In 1899, Laidlaw-Dunn-Gordon became part of what would eventually be the Worthington Pump & Machinery Company. Fig. 4 shows a c.1901 Laidlaw-Dunn-Gordon Class BB 10 in. (254 mm) stroke, 45 hp (34 kW), 150 rpm steam-driven air compressor with poppet air valves in the 10 in. (254 mm) bore cylinder. Laidlaw-Dunn-Gordon continued to be a prolific air compressor manufacturer, with many advanced machines including large tandem machines with throws on either side of a flywheel in the center such as the c.1904 Cincinnati Class 11 machine shown in Fig. 5, which was a 24 in. (610 mm) stroke, 345 hp (257 kw), 125 rpm two-stage steam-driven duplex air compressor with 32 in. (813 mm) and 20 in. (508 mm) diameter air cylinders with Cincinnati valve gear and an integral intercooler. Before World War I, Laidlaw-Dunn-Gordon had the broadest line of air compressors of any manufacturer.
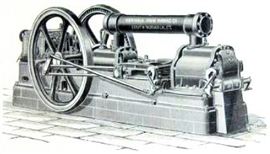
Capitalizing on the increasing use of compressed air in many types of industries, the Gardner Governor Company, a Quincy, Illinois manufacturer of steam engine governors, was also manufacturing air compressors by the end of the 19th century. An example of an early Gardner steam engine-driven air compressor, with the famous Gardner speed regulating governor atop, is shown in Fig. 6. Gardner’s product lines and production volume grew rapidly in the early 20th century, and it merged with the Denver Rock Drill Company to become Gardner Denver in the 1920s.
The next issue will continue the rapid evolution of horizontal air compressors that supported the industrial revolution.
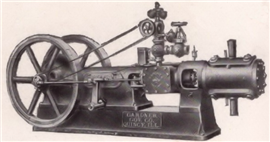
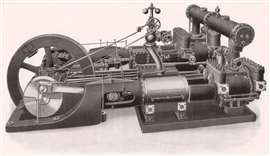
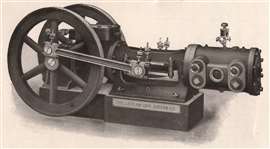
MAGAZINE
NEWSLETTER
CONNECT WITH THE TEAM
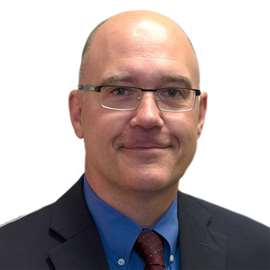
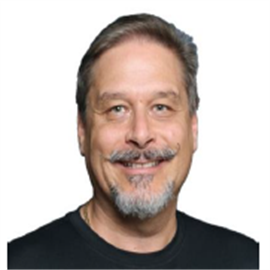
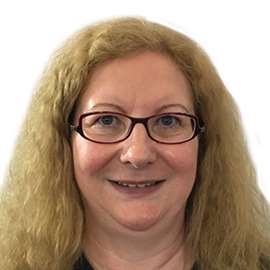