How to hit net zero

Partner Content produced by KHL Content Studio
11 June 2024
On a global scale, the shift from the construction industry to more sustainable practices has been at once impressive and underwhelming.
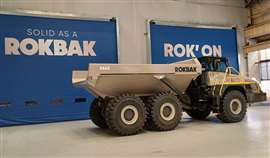
To put that statement into perspective, we have seen huge efforts being made to improve the energy efficiency of off-highway equipment. At the same time, carbon emissions from construction continue to rise and sustainability is more often seen as a buzzword in press releases than making a real difference on jobsites.
Clearly, the industry needs to do considerably more than making more fuel-efficient machines.
Of course, there are forward thinking companies bucking the trend – and some are finding that challenging targets and challenging timelines can be the mother of invention.
One such is Rokbak, the Motherwell, Scotland-based hauler manufacturer, that has reinvented itself, in more ways than one, since it was acquired by the Volvo Group in 2014.
At that time, it was called Terex Trucks, but the Volvo takeover, along with a hugely successful rebranding to Rokbak in 2021, has resulted in a paradigm shift for the company, which has become a genuine net zero trailblazer.
A strategy of through-and-through sustainability goals is already shifting the R&D strategy for Rokbak haulers, but the changes already seen within Rokbak’s manufacturing facility is impressive, to say the least.
Start by making a start
Being part of the Volvo Group, Rokbak aligns with the Science Based Targets initiative (SBTi) and has published targets of a 30% decrease in its machine CO₂ emissions by 2030 and a 50% reduction in factory emissions by the same year.
This path, says the company, should lead to net-zero emissions by 2040.
According to Rokbak’s sustainability manager, Karen Anne Duffy, the company’s sustainability roadmap has resulted in that 50% reduction in factory emissions arriving some six years ahead of schedule.
Describing some of the actions that have enabled this impressive result, she says, “We started by removing natural gas from our admin building and from the annexes on another two buildings – areas where our lunchrooms and offices are located. In total, between 2018 and 2022, we reduced our natural gas usage by 35%.
“We then compartmentalised the main factory building, with fireproof curtain. As well as preventing fire spread, this brought about solid energy benefits, as we’re now heating smaller spaces, as opposed to one large space.
“We also replaced all of our roller doors with fast-acting doors, which led to significant energy savings. In fact, it was very surprising to realise how much heat was being lost, just through doors failing to be closed on a regular basis.”
It was calculated by audit that this action saved approximately 109 tonnes of CO2. That figure takes into account factors including the average outdoor and indoor air temperature, average wind speed, the time taken to open and close the doors and the number of times per day the doors are opened.
Describing one of her “favourite transitions to date”, Karen Anne says the team switched the factory lighting from high pressure sodium lamps to LED lights, saving over 550kwh, or 42% of the energy used for lighting.
Karen Anne admits that the ten-year timescale to halve emissions from the facility was daunting when it was first put to them by Volvo.
“It did seem like a lot at the time,” she says, “especially when you consider that gas accounted for about 80% of our overall energy use. Even now, we don’t have clear line of sight as to what the replacement for gas will be; four years ago, we had even less idea what that might look like.”
She says having a 50001 certificate “keeps us focused on energy management and constantly looking for improvements and opportunities to cut emissions.”
This ISO accreditation is offered to businesses with healthy energy performance indicators and efficient energy management systems. It requires proof of reduced energy consumption and environmental impact, as well as increasing profitability.
Teamwork key to success
Karen Anne believes the cornerstone of Rokbak’s sustainability success is the people. The Motherwell site has been producing articulated haulers for over 50 years and many of the staff have family ties with the company that go back further still.
“They’ve got a family history with the site,” she says, “and they genuinely care about the place. I think that helps.
“The problem is, how do you comprehend carbon emissions? It’s a difficult thing to get across, but we’re working closely with consultants to ensure we’re engaging with staff in the best possible way, because it’s vital that everyone buys into the project.”
When asked if she expected to move so fast with energy savings, Karen Anne says, “I suppose it is quite surprising, largely because it hasn’t been what you would think of as headline emissions-reduction projects that have got us to this point.
“There have been a good number of relatively straightforward fixes up to this point. A lot of incremental gains, you might say.
“We’ve got a really engaged team of energy champions who are regularly on the shop floor, trying to find areas for improvement, to identify unnecessary waste and working with our overall energy management team to progress the initiatives we’re implementing.
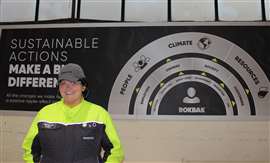
Karen Anne talks about some of Rokbak’s longer-term plans and comes back to the energy supply situation, which can be problematic for many manufacturing businesses, due largely to the levels of investment required to enable change.
She says, “All of our electricity is now purchased from 100% renewable resources. Gas is not so straightforward. There is green gas available, but not widely accessible.
“Also, you must still factor in grid emissions, because it’s combined with natural gas on the grid. So, the situation is a bit muddy at the moment.
“We are looking at the potential for on-site power generation as well, just to make us a bit more self-sufficient and to have more control over our energy supply. But that’s a longer-term plan, which will doubtless involve significant capital expenditure.”
The economics of sustainability
Asked whether reducing CO2 emissions must necessarily come at a cost to the business, she says “I actually think there are economic benefits to this transition, but it’s not always clear and it’s often not going to be immediate.
“In terms of current energy prices – particularly gas – if we were to become self-sufficient, there would be an immediate economic benefit, as we wouldn’t be paying suppliers.
“Also, looking to the longer term, we are probably going to start seeing things like carbon taxes become more prevalent, as we have seen with landfill tax for waste.
“These things are only going to go in one direction, and we feel it’s far better to be ahead of the curve.
“To that end, companies like Volvo CE and Rokbak are in a position to lead the way, and that’s what we’re trying to do.”

From a policy perspective, Karen Anne says any sustainability initiative put forward must try to show a return on investment.
“And in every case we’ve proposed so far,” she says, “we’ve managed to do that.
“In fact, it’s now built into our CapEx [capital expenditure] tool that the sustainability element must be included.
“So, if you’re submitting a project, what is the energy impact? Is this going to use more energy than we currently do? Is it going to present an energy saving and if so, what does that look like?
“Sustainability is now being built into the process; we have to think about it within the scope of every project we put forward, which is really good to see.”
Net zero through the value chain
“Because climate policies are only as good as the length of term of any given government; it’s businesses that are here for the long haul that have the ability to shape the emissions landscape. And we are starting to see other OEMs talking about the same things, which is great, because it helps to build pressure on governments to make policies that bring lasting benefits.”
Karen Anne’s focus at Rokbak is on emissions generated by the manufacturing process, but she also describes some of the work being undertaken by the company’s purchasing team, which is also making inroads to the wider Scope 2 and 3 emissions, generated by suppliers and end users.
She says the team is “working really hard with our suppliers, to bring them along on this journey with us. A new supplier portal allows them to record their CO2 emissions and their energy use.
“In terms of our products, there’s a lot being done to make them as sustainable as possible – and there’s a technology roadmap in place, to help us move towards that net zero product offering.
“The overarching ambition from Volvo is for the whole supply chain, the whole value chain, to be net zero by 2050, but with products, we’re aiming to reach net zero by 2040.
“With the average lifespan of our products being 10 years, that basically gives our customers that much of a run up to make the transition.”
Karen Anne admits that this transition is unlikely to be made without some pain.
She says, “We know some customers are working on really remote sites, where it’s not always easy to get power for electric machines, for example, as there’s not the infrastructure in place.
“There’s a lot of work to do, but we’re working hard to bring customers with us on our journey and help them overcome their own transition challenges.
“In fact, many of our suppliers are coming to us and asking for the opportunity to discuss sustainability.
“Our paint supplier, for example, has asked for a meeting, with sustainability one of the topics on the agenda – they want to talk about how we can work together to reduce solvent emissions.”
The future is greener
While Karen Anne feels extremely positive about the progress made so far by Rokbak, she recognises that the next part of the journey – from 50% reduction to net zero emissions – will be much tougher.
“I think what we’ve done so far, while also increasing our output volume, is really great, in terms of speed.
“It’s never going to be super-fast and I think, in order to do this right, you have to take a slow and steady approach.
“Becoming more sustainable for the long term is something that has to be considered from every angle. You can’t just look at it from an energy reduction perspective, it also has to work from a business point of view.
“But Rokbak has been clear in its messaging and that is that we are in this for the long haul.”
---------
All images courtesy Rokbak
---------
This article was produced by KHL’s Content Studio in partnership with experts at Rokbak
MAGAZINE
NEWSLETTER
CONNECT WITH THE TEAM
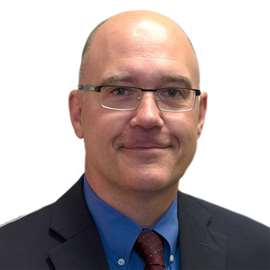
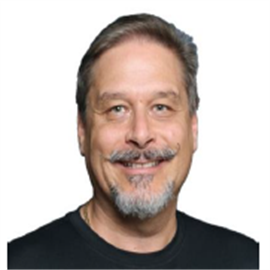
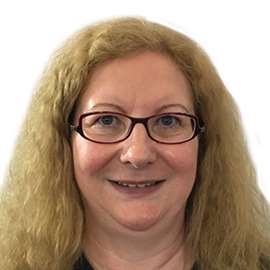