How axial fans are redefining the performance of off-highway machinery

Partner Content produced by KHL Content Studio
07 June 2024
The design priorities for today’s off-highway mobile machines and gensets are clear.
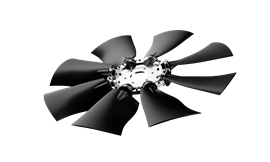
New machines must emit reduced levels of CO2, as well as other harmful gases and particulate matter.
Efficiency, durability and greater uptime across their lifespan is essential.
And more, end users and regulators demand that these machines are quieter – not an easy thing to achieve, given the prerequisite of equivalent or greater performance.
Nevertheless, new machines are ticking these boxes to a large degree, and R&D departments are seeing their budgets swell, as manufacturers ensure new models bring saleable upgrades to the table.
What makes engines cool?
Within the construction arena, fans need to cool heavy-duty engines which are operating hardcore duty cycles, often in harsh climates.
It’s little wonder that manufacturers are now placing higher importance than ever on the effective cooling of these engines.
Patrick Bold is the product director for impellers and clutches with Multi-Wing, the Denmark-based firm that designs and manufactures axial fans for use across industries including construction and power generation.
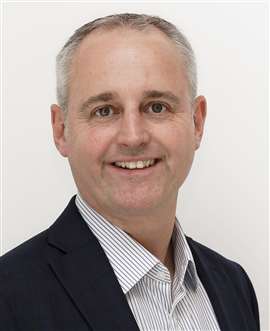
“We’ve recently seen a much higher focus on increasing the limiting ambient temperatures, or LAT, of equipment”, he says. “The LAT is the maximum allowable ambient temperature to which the engine cooling system can operate without failure or over-heating.
With emissions regulations and the use of machines in harsher climates, there is a need to have far better cooling of these machines, to ensure they’re up and running at all times.
“To achieve cooling requirements for emissions regulations, you need a thicker radiator, auxiliary coolers with a bigger resistance and higher airflow.
That all points to the fan needing to do more work, while minimizing the noise, because manufacturers are also being asked to reduce noise emissions from machines.”
These demanding prerequisites call for fans that can deliver much more than impressive airflow; they must boost a machine’s efficiency in ways not previously considered.
When describing the development of such fans, Nicolas Geiger, global development manager for engine cooling impellers at Multi-Wing, says, “A lot comes down to understanding the fan as part of a system.
You can do all the tests you want in laboratory conditions, but if you don’t take into account how the machine is set up – and what its current limitations are – it’s very difficult to optimise it with a fan.”
Geiger describes the recent use of 3D printing technology, which can demonstrate the potential of the latest fan designs.
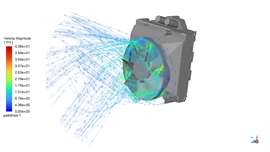
He says, “We can now 3D print working prototypes for customers that can be placed directly into an excavator, for example. That was nearly unthinkable even a couple of years ago.”
Fluid dynamics in action
While Geiger stresses the importance of working hands-on with machines to ensure optimum fan design, he also acknowledges the benefits of utilizing the latest technology to aid the process.
“A lot of what we do,” he says, “revolves around fluid dynamics, which we test with CFD computational fluid dynamics simulation.
We can optimise the profiles to generate the least possible turbulence, which results in lower noise and higher efficiency.
The cleaner the air, the more you can reduce the noise – but that’s a difficult thing to achieve when the air is at such high pressure.
“With CFD, we are able to run tests on thousands of designs in a few days, and the tests themselves are becoming more refined, as software improves and computers are faster. We can run models today that were impossible to imagine two or three years ago,” explains Geiger. “
That said, results still fundamentally come down to the best combination of physics and the machines knowledge.”
Looking to the future
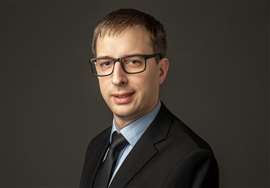
Given the significance being placed on equipment manufacturers to produce more sustainable equipment, it’s easy to see why fan manufacturers are having to up their game.
According to Geiger, “The impeller used to be a catalogue product. You would say I need something around this pressure and this diameter. What do you have? It would be ordered and sent out and you’d hear no more about it.
“Today, we are being asked to design a fan for a machine that will be on the market in potentially three years, and the fan must operate optimally within extremely specific constraints.”
Patrick Bold agrees, adding that, in heavy construction and power equipment, the airflow path is severely obstructed, a fact that also drives the need for a more efficient fan.
“In the past,” he says, “fan blade profiles were all relatively similar, virtually universal products that could be used in heating, ventilation and air conditioning, as well as engine cooling applications.
“These new blades are designed with a focus on the engine cooling environment, with very poor air inlet conditions and radiators with inadequate shrouds, which have commercial targets at the forefront of their design.”
There is no doubt that today’s manufacturers are waking up to the performance and noise reduction benefits a highly efficient fan can bring to their equipment.
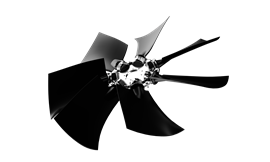
Bold uses the booming power generation industry as an example, saying, “Every kilowatt you can save cooling the engine is one more kilowatt you have available from that machine, and that means burning less fuel.
That is a very strong focus in the genset industry – a minimum amount of power to cool the engine.”
Design for life
So, an optimum cooled engine that results in reduced fuel burn delivers a lower total cost of ownership, but that is only true for as long as the fan is operational. With that and their efficiency demands in mind, OEMs generally expect fans to last as long as the engine they’re cooling.
“Here,” says Bold, “the weight of the impeller is really important from a durability perspective, because the higher the weight of the impeller, the more wear there is on the bearings, as well as the belts in the machine. Also, service intervals will be extended with a lighter fan.
In other words, the lower the weight of the impeller, the lower the total cost of ownership of the machine.
“A lot of our recent work has been on achieving lower weight while making sure performance targets are met, and we’ve done that by using the minimum number of blades.
The equation is pretty simple: fewer blades, less material, lower noise and less weight.
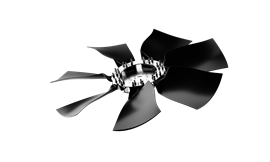
We’ve optimised the blade design and the shape of the blade to increase the working surface area and maximize performance.”
We have reached a point in the construction industry where incremental gains such as this can be worth their weight in new business, but Bold and Geiger maintain these new axial fans have the potential to deliver more than incremental gains.
Bold says, “Operators will definitely notice the difference in terms of noise emissions. As engines have become quieter, especially with the filters behind the engine, you’ll find in some machines that most of the noise doesn’t come from the engine, it comes from the fan.
So that puts the fan into focus in some of the latest high-tech machines.”
Geiger agrees, but adds, “Unlike for consumer products, where low noise is a differentiation feature only there are regulations now that say if your machine makes too much noise, you cannot use it, you cannot sell it.
Noisy and inefficient machines are just not an option anymore.”
All images courtesy Multi-Wing
-------
This article was written by KHL’s Content Studio, in partnership with product experts from Multi-Wing
Collaboration between OEMs and engine cooling experts during the early stages of the design process delivers significant advancements. This allows OEMs to optimize their machinery design for efficient thermal management, enhancing performance, reliability and longevity. Contact Multi-Wing to discuss your application with an experience sales engineer. www.multi-wing.com |
MAGAZINE
NEWSLETTER
CONNECT WITH THE TEAM
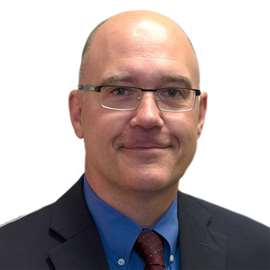
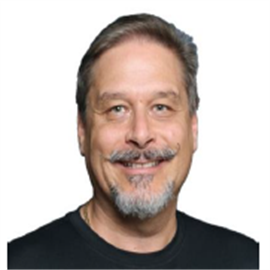
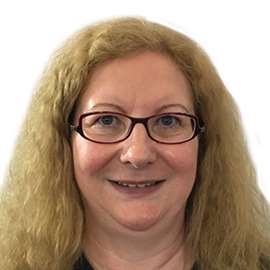