Engineering uptime: the Rokbak approach

Partner Content produced by KHL Content Studio
04 November 2024
“It’s important to see the bigger picture when it comes to equipment uptime, rather than only the here-and-now cost.”
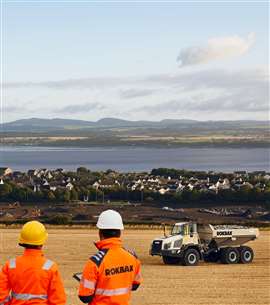
So says Charlie Urquhart, product manager with Rokbak, a manufacturer of articulated dump trucks, based in Motherwell, Scotland.
We are discussing machine productivity, and the numerous roads that lead to optimal uptime, including servicing, maintenance, operator training and general practices that can help extend the useful life of construction equipment.
Time is money in industries such as construction, quarrying and mining, but when it comes to uptime, most would agree it’s time well spent to ensure machines are healthy and operating at maximum efficiency.
The problem with short-term thinking
A recent report from the aftersales technology firm ClearOps reported that machine downtime costs are now estimated to be some $40,000 per machine per year.
This sobering figure is based on the potential cumulative effect downtime can have on a construction business. If, for example, an excavator is unexpectedly down, then trucks become idle and production output is reduced or stops, often causing project delays.
And this scenario will generally play out wherever the downed machine lies in the earthmoving chain.
All too often though, the manufacturer’s recommendations on the correct use of equipment, on using original components to replace wear parts, or on maintenance and service intervals, are taken with a pinch of salt – or even a healthy spoonful of cynicism.
Urquhart believes “leaving anything to the last minute is rarely a good idea, and that is especially the case when dealing with production-critical equipment.”
He adds, “The cost of production comes from more than just moving material from A to B. Machine warnings, fault codes and maintenance intervals should never be ignored, as to do so could exacerbate issues and result in more costly or time-consuming repairs.
“Also, performing scheduled maintenance on time will help with machine resale value, providing peace of mind to a prospective buyer that the equipment has been looked after properly.”
The case for original parts
On the subject of maintaining equipment, Urquhart also urges construction, quarrying and mining businesses to avoid buying cheap third-party components, as it is highly likely they will wear faster than original OEM parts.
“You may have saved some money on the purchase price,” he says, “but now your machine is back in the workshop – sooner than expected – and your production operation is adversely affected. The old saying ‘buy cheap, buy twice’ springs to mind.”
As well as potentially having a positive influence on machine uptime, original approved parts will generally be guaranteed (for two years, or 6,000 hours, in the case of Rokbak) and that equates to peace of mind for owners and operators.
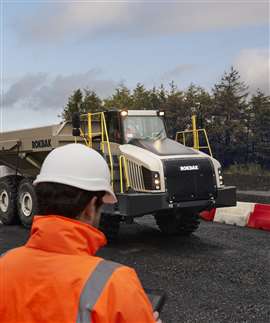
Urquhart, incidentally, sees the operator as a hugely important part of the uptime equation.
As with all pieces of earthmoving equipment, haul trucks are production-critical machines, and he believes it is crucial that operators are properly trained in their correct use.
They should fully understand, for example, how and when to use differential locks and retarders, as to do so incorrectly could have an adverse effect on component lifetime and subsequently on machine uptime.
“The correct use of such features also promotes safer operation, as well as improving cycle times and benefitting overall production,” Urquhart says.
Benefits of technology
The complexities of maximising uptime are challenging to manage – particularly on expansive sites where materials, equipment and workers interact in countless ways on a daily basis.
Fortunately, technology is now available to ensure both equipment operators and construction businesses remain in the proverbial driving seat.
Manufacturers who provide telematics systems with their equipment have been working hard to expand their capabilities and give customers up-to-the-minute data on the operating health of their machines.
Rokbak’s system is called Haul Track and the latest iteration is able to transmit real-time data on a wide range of machine matters, to an internet-connected device.
As well as machine location and fault alerts, Haul Track data includes machine hours worked, idle time and fuel consumed, as well as the advanced monitoring of machine systems, temperatures and pressures.
Used in conjunction with Rokbak’s optional on-board weigh load system, Haul Track can also identify issues with underloading or overloading, helping to maximise productivity and efficiency.
In short, customers receive a clear picture of a machine’s productivity and its current state of operational health.
More data, more uptime
Urquhart says the Rokbak system, Haul Track, has been developed with input from key dealers to be a collaborative tool for customers with mixed fleets, as its API (application programming interface) allows data from the hauler to be analysed alongside that of other machines on site.
Urquhart says regular and detailed analysis of Haul Track data can lead to significant savings in equipment costs, but he highlights the popularity among Rokbak customers of the maintenance alert feature.
“Haul Track provides notice of an upcoming scheduled maintenance event,” he says, “so the necessary people and parts can be in the right place at the right time to ensure machine downtime has minimum impact on productivity.”
Similarly, fault alerts are an extremely useful tool for maintaining effective operational costs. Not only are machines protected from operating with fault that previously may have gone unreported, but technicians can arrive at the machine with the correct tools and parts to fix the fault.
In the past, telematics systems like Haul Track would have been introduced by larger contractors, looking for technology to deliver marginal gains to the bottom line that could make a difference on sizeable projects.
Now things have changed and the latest machine technology can be equally beneficial for construction, quarrying and mining businesses of any size.
Fuelling change
Possibly the best example of this is in fuel usage, which represents one of the largest operational costs in construction. Last year, a report from the Association of Equipment Manufacturers estimated that between 10% and 30% of fuel burn comes from the non-productive idling of equipment.
This is a significant unnecessary cost for construction businesses and one that can be identified and effectively reduced through the use of telematics.
Urquhart is adamant that technology such as this is already playing its part in increasing productivity in the construction industry. He says, “Having a clear picture of your fleet means you can be proactive with things like maintenance plans. This alone will improve machine uptime and has the potential to keep production on or ahead of schedule.”
He does admit, however, that more has to be done in terms of educating the industry about the benefits of the technology that is currently available.
“When you’re operating a busy quarry or construction site, finding the time to get to grips with new machine technology is never easy,” he says.
“Along with our dealers, we can help by offering technical advice and support to ensure trucks deliver optimal uptime and productivity.”
Ultimately, Urquhart believes the benefits on job sites can be significant, when operators are given the right tools for the job.
“You need a combination of engineering excellence, quality build and great technology to maximise machine uptime,” he says. “If you get the combination right, you’ll see the difference in the bottom line.”
--------
All images courtesy Rokbak
--------
This article was produced by KHL’s Content Studio in collaboration with experts from Rokbak
MAGAZINE
NEWSLETTER
CONNECT WITH THE TEAM
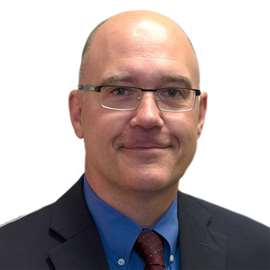
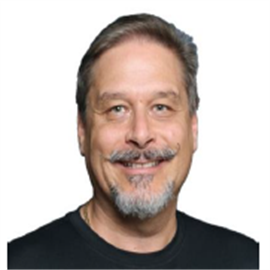
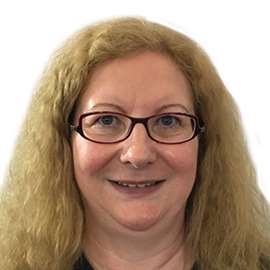