TechCorner: Research from EFRC reveals compressor reliability
August 27, 2021
André Eijk explores the compressor reliability survey from the European Forum for Reciprocating Compressors (EFRC), which reports the improvement of reliability, efficiency and integrity.
The reciprocating compressor’s flexibility in handling wide capacity variations and generating high pressures independent of the density of the gas, makes it a vital component in today’s energy markets – upstream, midstream and downstream.
Reciprocating compressors are expected to become even more important in the near future as hydrogen finds applications as an energy carrier in transport, industry and households. Especially for hydrogen applications, reciprocating compressors have advantages over turbo compressors due to their higher efficiency, higher flow rates and higher pressure ratios.
Notwithstanding the many inherent advantages of reciprocating compressors, their reliability, efficiency and integrity have improved considerably over recent decades. This has been achieved through developments such as improved flow control devices, new and improved valve design, new materials, product optimisation and improved techniques for pulsation and vibration control.
In the past the industry still had a perception that reciprocating compressors suffered from poor reliability in comparison with turbo compressors. For that reason, the EFRC in 2009 carried out a compressor reliability project to investigate users’ experience with several types of compression equipment regarding versatility, robustness and reliability. The focus was on those aspects that industry had indicated are most critical with respect to unscheduled shutdowns (Figure 1).

The results of the study have been used by several compressor OEMs and parts suppliers to focus their R&D programmes on further improving their products. Another useful outcome of the 2009 survey was the EFRC guideline of How to avoid liquids in reciprocating compressor systems. This is used worldwide by both operators and reciprocating compressor system designers.
Click here to download the EFRC guideline of Scope of standards and guidelines for reciprocating compressor systems
In 2019, with the original compressor reliability survey now 10 years old, the EFRC’s R&D group decided it was time for a new one. This new reliability survey would collect the latest information on users’ perceptions of the reliability of reciprocating compressor systems and their parts.
Based on the results of the new study, the EFRC also intends to develop a new guideline called Operations and troubleshooting. The aim of this document is to provide information on how to operate reciprocating compressor systems safely, reliably and efficiently so as to avoid failures and unscheduled shutdowns. With this in mind, the new reliability study also asked users which topics the new guideline should include.
Effect of compressor speed remains uncertain
In several of its questions, the survey made a distinction between low speed (200-600 rpm), medium speed (600-1000 rpm) and high speed (>1000 rpm) compressors. For many of these questions, the numbers of responses for medium and high speed compressors was limited (<15 percent).
This means that for several items, conclusions with respect to medium and high speed compressors are not statistically reliable. For that reason they have not been included in this article.
Reliability (R), Availability (A), Maintainability (M) and Integrity (I)
Compressor systems can be classified in terms of their Reliability (R), Availability (A) and Maintainability (M). Generally speaking, reliability and availability are considered together, while maintainability, although equally important, is dealt with separately. The reason for this is that reliability and availability can be clearly defined, to the extent that they often feature in contract guarantee clauses.
For maintainability, in contrast, only principles and guidelines can be specified, since many variables and constraints typically affect the designer’s ability to provide the ideal solution.
The most commonly accepted definitions of reliability and availability are:
In which:
8760 = number of hours in one year (substitute the required number of operating hours, if this is lower);
SD = scheduled downtime, hours per year, and;
UD = unscheduled downtime, hours per year.
The subtle difference between reliability and availability is that, because of the need for Scheduled Downtime (SD), availability will never be 100% even if there is no unscheduled downtime.
In practice, one also sometimes sees availability defined identically to reliability. By this definition, availability will be 100% if the machine is available for all of the time that it was planned to be.
Maintainability, the ability to maintain a machine, is really self-explanatory. However, it does have a direct effect on availability. Simply put, if the SD is extended because the machine is difficult to maintain, the availability is compromised.
Fourth variable of Integrity (I)
Integrity is defined to account for the number of failures that affect a specified compressor. Integrity focuses on the economic damage and loss of production due to an unscheduled failure. Unscheduled failures have the greatest impact on reliability.
The difficulty in defining this parameter is that multiple aspects can influence integrity. The economic damage caused by a failed compressor can vary greatly between different compressors and their systems. The amount of economic damage and loss of production depend, for example, on the availability, the Mean Time Between Failures (MTBF) and Mean Time To Repair (MTTR), the total costs (operating costs, maintenance costs for repairs, initial costs for spare parts and installation) and reliability.
Results of EFRC 2019 study
Despite the fact that the number of responses to the 2019 study was 19% less than that for the 2009 study, the results can still be used.
General consensus on Reliability (R)
In general we can conclude that the largest share of reciprocating and screw compressors have a reliability in the range 90-97%, both onshore and offshore (Figure 2).
The share of reciprocating compressors with reliability in the range 90-97% is slightly higher than in the 2009 study (42.7% in 2009 versus 49.5% now). For screw compressors the corresponding figures are 31.71% in 2009 versus 38.39% now, which is also an increase.
In the reliability range 98-100%, turbocompressors have a much larger share than that of reciprocating and screw compressors, both onshore and offshore. The share of turbocompressors with reliability in the range 90-97% is slightly higher than in the 2009 study (36.59% in 2009 versus 39.20% now).

Another important conclusion is that the perception of reliability for offshore systems is much lower than for onshore systems, for all compressor types. This is especially the case for compressors with reliability in the range <60%.
The detailed results show that we can attribute this to their use in offshore applications. The top five components responsible for unscheduled shutdowns follow the same order in the 2019 study as they did in 2009 (Figure 3).

All other components have a lower criticality than in the 2009 survey. Components that are negatively affected by incorrect cylinder lubrication have the highest score for wear parts. In decreasing order of the number of unscheduled shutdowns, these are piston rings, valves, packings and rider bands. The figures are more or less the same as in 2009.
Compressor valve life
The participants indicated that the dominant parameters negatively influencing compressor valve life are liquid carryover, lack of knowledge, gas leakage and operating at off-design conditions (Figure 4).
Most of these parameters relate to operational conditions that can only be influenced by end users, not by compressor manufacturers.

Pulsation and vibration fatigue failures
With respect to pulsation and vibration, we conclude that most fatigue failures (58.5%) are experienced for Small-Bore Connections (SBCs, Figure 5).
According to ISO 20816-8, SBCs are branch connections on mainline piping, vessels, or equipment, whose diameter is up to DN 50 (NPS 2”) or up to 10% of the diameter of the main line, and excluding connections whose diameter is greater than 25% than that of the main line.
The number of SBC failures is highest for high speed compressors. Piping is number two in the list of fatigue failure sites, and is also highest for high speed compressors. The relatively high level (46.34%) of compressor valve failures attributable to pulsations and vibrations is also remarkable.

Training on monitoring systems can increase reliability
A large proportion of the participants (85%) indicated that reliability increases when condition monitoring systems are installed. However, 70% of the participants indicated that they do not have enough knowledge of how to interpret the monitoring data.
They also indicated that training on monitoring systems can increase reliability, which was also the case in 2009. The share of participants who have this opinion is much higher in the present study than in 2009 (74% now versus 43% in 2009). Furthermore, 38% of the participants indicated that they have wireless condition monitoring systems, and within this group 36% stated this has increased reliability.
Flow control systems
The survey shows a large increase in reliability in comparison to the 2009 study for compressors with stepless flow control systems, especially for low speed compressors.
The aspects with the strongest negative impact on the reliability of stepless flow control systems are problems with the control system, and pulsations and vibrations. The participants indicated that the reliability of such compressors can be improved by greater knowledge of this type of control system, an opinion that is much higher now than in 2009 (87.2% now versus 50.5% in 2009).
Reciprocating compressor systems
The top five parameters that have increased the most in terms of reliability are, in descending order: compressor valves; pressure packings; process conditions; rider bands, and; cylinder lubrication/lube systems (see also Figure 6). These ratings are approximately the same as in 2009.
It is remarkable to see that four out of these top five parameters (compressor valves, pressure packings, process conditions and rider bands) feature in the top five components that mainly cause unscheduled shutdowns.
This suggests that compressor and parts suppliers have improved their products, despite the fact that these components still cause the majority of unscheduled shutdowns.

More detailed information can be found in the report, which can be purchased via Maja Schütz at the EFRC, click here to send an email

He is a retired senior expert at TNO in the Netherlands on pulsation and vibration control of pipe systems, compressors, pumps and process equipment.
Eijk was actively involved in API, and EFRC working groups for the development of standards and guidelines on pulsations and vibrations, for numerous years.
MAGAZINE
NEWSLETTER

CONNECT WITH THE TEAM
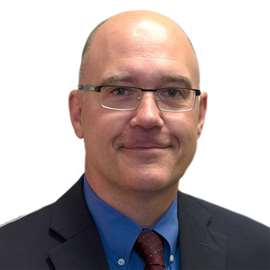
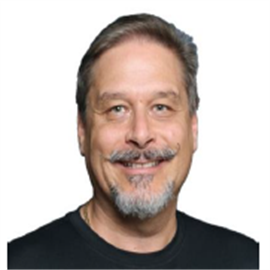
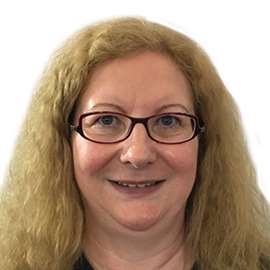
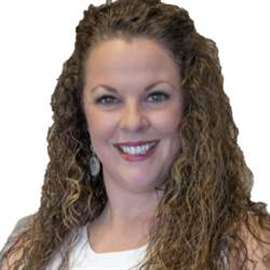