Turbulence Control
05 December 2016

Reduction of pulsation, vibration and noise through modification of piping
By NATHAN W. POERNER, DUSTIN CASTLE AND VISHWAS IYENGAR, PHD
Enlink, formerly Devon Energy, maintains separation and processing plant facilities intended to separate heavier hydrocarbon constituents. At one of these locations, a number of significant issues with a turbine ex- pander/process compressor system had existed for an extended period of time, with the issues primarily occurring on the compressor side of the system.
A partial history of the issues experienced by this unit details noticeable and problematic vibration, unit failures and shutdowns, as well as a persistent noise issue in the vicinity of the unit and a downstream cooler. Specific failures of the unit itself included broken blades on the compressor wheel, sheered diffuser plate bolts, and diffuser plate damage. Unit outage due to these failures occurred three times in a 2.5-year period, with a mean time between failures of less than a year.
The operating conditions of the unit are incoming production stream gas entering the compressor at 600 psig (4137 kPa gage) and exiting at approximately 750 psig (5171 kPa gage). The gas then enters an expander at 725 psig (4999 kPa gage) after passing through an air cooler — for condensation of the heavier liquids in the hydrocarbon stream — and exits the expander at 150 psig (1034 kPa gage) for further processing.
Initial field-testing
Testing setup and conditions
After Southwest Research Institute (SwRI) was contracted to aid in resolving the issues with the machinery, key information was gathered in a field study performed at the Bridgeport facility in Texas. Measurements were also made on a similar installation at a second facility (Northridge) in Oklahoma. Measurements made at both facilities included vibration measurements, sound level measurements and, where possible, pressure pulsation measurements. These measurements were used in the comparison of the two different facilities, and eventually in comparison with computational fluid dynamics (CFD) models for critical piping stretches. . . .
Read the full story in the October issue of COMPRESSORTech2.
MAGAZINE
NEWSLETTER
CONNECT WITH THE TEAM
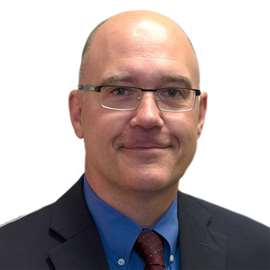
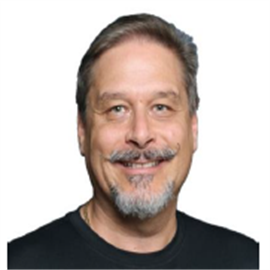
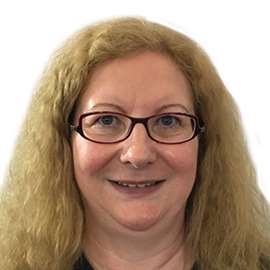