The future of crane operator training: technology, safety and efficiency trends
October 22, 2024
In an industry that is constantly evolving, it’s easy to see that the crane and rigging sector is undergoing a significant shift in how operator training is delivered, with technology playing a central role in shaping the future.
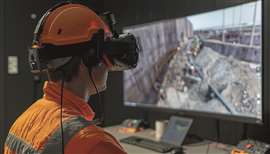
ACT convened a panel of three industry experts to discuss evolving trends in operator training, from classroom instruction to virtual reality simulators, highlighting how new technology, hybrid learning and safety standards are reshaping crane and rigging education. Participants include Bruce Kabalen, vice of president of sales & marketing, A1A Software; Andrew Kauser, chief product officer, senior vice president of virtual reality and online learning, Industrial Training International; and Dana Jackson, chief operating officer, North American Crane Bureau.
What are the trends you are seeing in terms of classroom and in-the-seat training?
KABALEN: Our classroom training is up well over 50 percent in 2024, and I anticipate further growth in 2025 as our new products continue to reach our customers.
KAUSER: There has been a shift towards blended learning. Traditional classroom and hands-on, in-seat training are evolving. There’s a growing trend of integrating digital tools and simulations to complement in-person instruction. Classroom training is increasingly supported by e-learning, animation, simulation and pre-assessment tools, which allow instructors to tailor content based on individual skill levels.
We are also seeing focused, shorter training sessions, as there’s been a push towards more focused, shorter training modules, allowing companies to minimize downtime. This trend is driven by a demand for more efficient training without sacrificing quality or safety. Instructor-led experience also remains key. There’s still a strong emphasis on instructor-led, in-the-seat training where trainees directly engage with equipment under real-world conditions. This remains critical for high-risk industries like crane and rigging.
JACKSON: In the crane and lift industry, training trends are evolving to address technological advancements, safety regulations, and the need for more efficient and effective learning methods. While we still experience technology every day, many of our clients are still looking for in-person training with practical seat time. We have also been working through a blended learning approach with online training leading into in-person training. Of course, proper training with credentials and certifications are expected to meet and exceed today’s standards and regulations.
What are the trends you are seeing in terms of simulator training?
KABALEN: You still have the static operator training simulators (TV screens with operator’s seat and controls) with virtual jobsite with specific crane model that training group purchased.
KAUSER: Adoption of simulator technology is accelerating. Simulators are becoming more widely accepted across industries. They’re increasingly seen as a cost-effective, safe way to train operators on complex equipment without risking damage or accidents. The reduced downtime and the ability to simulate difficult scenarios are major draws. Simulation technology is advancing, with improved realism, data analytics and feedback loops for learners. Operators are being evaluated not only on skills but also on their ability to respond to unexpected conditions, something difficult to simulate with traditional training. There’s also a trend toward delivering simulations via browser or mobile device, allowing organizations to deliver high-quality training more broadly and increase speed to competence.
JACKSON: Overall, simulator training is enhancing crane operator training by offering a more effective, flexible and safe learning environment. It helps bridge the gap between theoretical knowledge and practical applications, preparing operators for real-world challenges in a controlled setting. We continue to offer our VR-based Overhead Crane and Mobile Crane Simulators, which have soared on popularity. In addition, the involvement of simulation training is key to generating interest from our next generation of crane and lift equipment operators.
What are the trends you are seeing in terms of virtual reality training?
KABALEN: I believe A1A’s 3D Lift Vision is the newest in the industry and allows users to create training environments in 3D Lift Plan and then transport the instructor and student into that environment “virtually” to operate and demonstrate critical lift plans within the created environment.
KAUSER: VR training is gaining adoption because it offers a safe environment for high-risk training scenarios while improving the skills of the user. Learners can practice scenarios that would be too dangerous in the real world and hone their skills, without adding additional wear and tear to the existing machines. VR has become more reliable and affordable, allowing organizations to scale training efforts. Employees in multiple locations can access standardized training programs without the need for expensive travel or facilities. VR allows for a more customized training approach. With custom Learning Paths we can create unique learning opportunities for each trainee based on their specific learning requirements and offer personalized feedback. VR with Learning Paths allow trainees to progress at their own pace. This trend aligns with the broader shift towards individualized learning in the industrial training space.
JACKSON: Our virtual reality training units are being used in numerous ways. They are being used to generate interest in the lift industry from new potential operators. This seems especially obvious when we utilize virtual reality in collaboration with job fairs or skilled trade expos. The attention virtual reality brings to the lift industry is key in starting the conversation of what’s next for job seekers of all ages. This is extremely important as skilled trades struggle to fill high-paying positions not previously considered.
After the pandemic, there was an uptick in remote training. Is this avenue of training still growing?
KABALEN: [We] don’t see it growing, but our customers use our online offerings to prepare for in-person training like most of the crane manufacturers.
KAUSER: The pandemic led to a significant rise in remote training as companies sought to minimize in-person interactions. While the initial surge has slowed, remote training is still growing, particularly in hybrid models where trainees might engage remotely for theoretical or foundational learning, then follow up with in-person or simulation-based practical sessions.
Remote training allows companies to train larger audiences, especially for theoretical aspects. For organizations with global or distributed workforces, this model is proving to be efficient, reducing travel costs and logistical constraints.
JACKSON: The pandemic had an immediate impact on the lift industry just as it has on every facet of how we operate every day. The way we looked at in-person training changed immediately and opened up discussions not previously considered as options. Questions about online learning, blended learning and VR simulation training all began to come to fruition. While we did see an immediate increase in remote training in the years after the pandemic, that interest seems to have leveled off. Our programs have had a major upswing back in the direction of in-person training, at our clients’ sites. However, we are still using the blended approach to decrease the time needed for in-person training.
What are the biggest issues in terms of operator training?
KABALEN: [This is not applicable] in our training, so can’t really comment.
KAUSER: One of the biggest issues facing operator training is the widening skills gap, driven by an aging workforce and a shortage of skilled new operators. This makes training critical to prepare the next generation of workers. Companies often struggle to balance the cost of training with the need to minimize equipment downtime.
Effective solutions are needed to ensure that training doesn’t impact productivity, which is where simulators and VR training are gaining traction. Another challenge is ensuring consistent, high-quality training across locations and instructors. Variability in training delivery can result in inconsistent skill development, which impacts operational safety and efficiency. Implementing a training program that incorporates VR and simulation creates a consistent deliverable with measurable data allowing companies to identify skill readiness across the workforce.
JACKSON: Crane operator training is essential for ensuring safe and effective crane operations. We look to OSHA and ANSI for the baseline of rules and regulations to follow. Risk, compliance, consistency, standardization, cost restraints and retention remain challenges at the forefront of training and why it’s so important.
Here at the North American Crane Bureau, we are fully committed to addressing these challenges, which require a combination of well-designed training programs, advanced technology and ongoing support to ensure that crane operators are well-prepared to handle their roles safely and effectively. We continue to learn and balance theoretical knowledge with practical experience and continuously adapt to industry developments which are key to overcoming operator and equipment owner training issues.
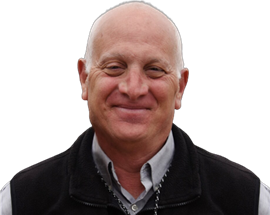
Bruce Kabalen is A1A Software’s Vice of President of Sales & Marketing. Before joining A1A in 2023, he spent 25 years as the key technology expert for Link-Belt Cranes. He was the primary liaison with A1A to implement A1A’s products for Link-Belt’s dealers and customers.
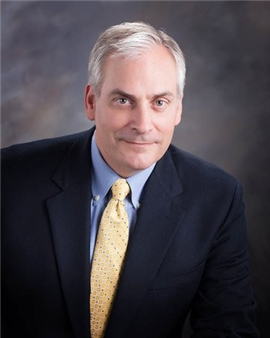
Andrew Kauser has over 20 years’ experience in the management and implementation of advanced education programs. His history with ITI goes back a number of years, with him officially joining the company full time in 2021. With a special interest in industrial skills training, he guided TPC Training Systems to become a market leader. Kauser currently sits on multiple boards and is the past Chair of The International Association for Continuing Education & Training (IACET).
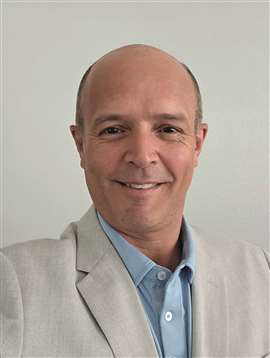
For the past 17 years, Dana Jackson has held pivotal positions at the North American Crane Bureau, (NACB), culminating as the Chief Operating Officer, playing a pivotal role in shaping the company’s direction within the lift industry. Under Jackson’s leadership, NACB has grown significantly, culminating in its recent acquisition by Crane Tech USA and WHECO. This strategic move has greatly expanded the company’s offerings and helped further solidify its position as a leader in the crane and lift industry.
MAGAZINE
NEWSLETTER

CONNECT WITH THE TEAM
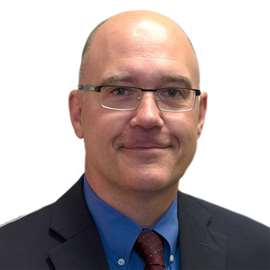
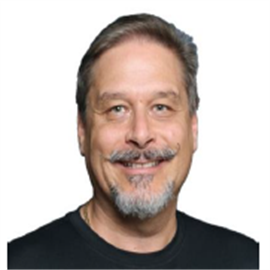
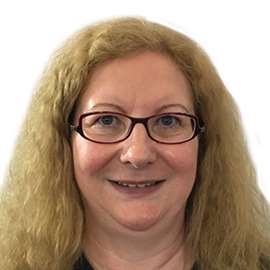
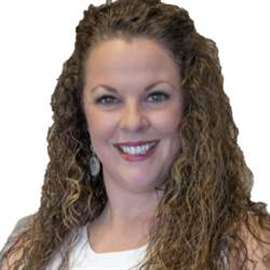