The Case For Variable-Speed Drives For Vapor Recovery
July 05, 2017
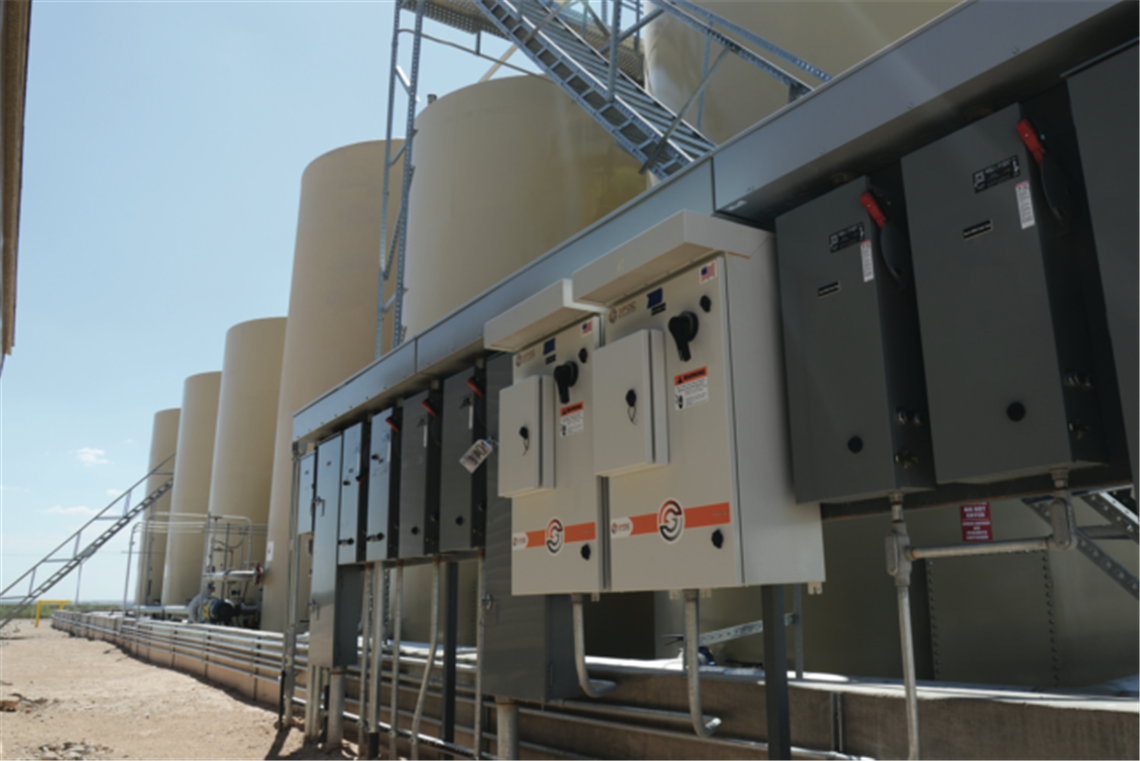
This article was originally published in the June issue of COMPRESSORtech2. Get every issue in your inbox/mailbox and access to our digital archives with a free subscription.
By Rich Vigil
It is no longer news that the growing emphasis on sustainability is leading the charge for increased efficiency in new technologies.
Underground crude oil contains many lighter hydrocarbons in solution. In natural gas, the goal is to reduce methane and volatile organic compound (VOC) emissions. During storage, a variety of gases are drawn out of the storage tank under low pressure. These include light hydrocarbons like methane (40-60%) and other VOCs; natural gas liquids (NGLs); hazardous air pollutants (HAP) and some inert gases.
In recognition of this growing environmental challenge, in some states and in other parts of the world, vapor recovery is becoming mandatory. One way to prevent emissions of these light hydrocarbon vapors — and yield significant savings — is to install vapor recovery units (VRUs) near storage tanks.
Vapor recovery units are integrated compression systems used to collect and compress low-volume gas and recover natural gas emissions with high levels of hydrocarbon sulfide from oilfield stock tanks. According to the U.S Environmental Protection Agency (EPA), VRUs safely prevent up to 95% of VOCs from being released into the atmosphere and/or from generating noxious and potentially explosive fumes and environmental damages. Currently, 8000-10,000 VRUs are installed in the oil production sector, with an average of four tanks connected to each VRU.
The vapor recovery process
When oil is brought to the surface and processed, the oil is first piped to high-pressure and low-pressure separators (also called suction scrubbers). Large suction scrubbers effectively separate condensate from the gas and drain to waste or back to the stock tank.
From the separator, condensed liquids are separated, collected and recycled back into the storage tank to await sale and transportation offsite. The remaining vapors flow through a compressor and are metered and removed from the VRU system.
The purpose of VRUs is to regulate the amount of pressure within the storage tank. When the storage vessel is pressurized and the gas is drawn down, it will not leak, or it may leak very slowly.
When the oil is withdrawn and the oil level drops, a vacuum forms in the top of the tank. Vapors “flash out” and collect in the space between the liquid and the fixed roof of the tank. As the liquid level in the tank fluctuates, the remaining hydrocarbons in the oil are emitted as vapor into the tank. These vapors are then vented, flared, or recovered by VRUs.
Economic benefits of recovered vapors
Venting and flaring are becoming less common as there are now established limits on the amount of VOCs a company may emit each year. Instead, vapor may be recovered and recycled for a number of applications:
- Recapture the gas for use or sale.
- Liquefy it for recirculation, convert it to LNG or process it into NGLs.
- Reinject it into the reservoir to lift more oil.
- Burn it via a combustor or boiler to generate an energy source that can be used for power generation or wastewater treatment.
Configuring a VRU package
When configuring a VRU package, it’s necessary to consider a number of factors, including the type of gas, volume, molecular weight, pressure, and corrosiveness of the hydrocarbon gas.
Technology choices include rotary screw, rotary vane, reciprocating and liquid ring vacuum pumps/compressors in sizes that range from just a few horsepower to several hundred horsepower.
Commercial factors also come into play depending upon the recovery requirements, the process the gas will be cycled through, maintenance considerations, and cycle and runtime.
Regardless of the final process, it’s a challenge for many facilities to manage the gas flow efficiently because vapor recovery itself is never constant. Variations in pressure, temperature and volume can occur multiple times within a tank, resulting from seasonal temperature changes or changes in production. Yet for all their environmental and economic benefits, VRUs are not always optimized to respond to environmental and operational fluctuations.
For example, a compressor’s output may exceed demand by 50%, yet the compressor is set to run nonstop at maximum speed. This means that much of the energy required to power that compressor is wasted.
Optimized compressor speed for changing conditions
To effectively capture the vapors at peak intervals, the compressor must adapt its speed in response to changing conditions. For this reason, electrical-driven compressors equipped with variable-speed drives are crucial to VRU efficiency.
Variable-speed-driven gas compressors continually and automatically adjust the production and output of compressed gas to meet fluctuating power requirements. With this configuration, the operator can vary the compressor’s speed to respond to changes in pressure, temperature and volume.
Substantial energy savings
For the operator, this yields substantial savings in both energy consumption and operating costs. Compared to a fixed-drive compressor, a properly sized variable-speed-driven compressor can be operated for significantly less power.
To put this in perspective, for a 200 hp (150 kW) compressor running at a constant speed around the clock, the electrical cost at US$0.03 per kWh is US$41,273 per year. If the kWh price jumps to US$0.08, the cost to operate that compressor jumps to US$110,062 per year — not including other costs such as on-peak or demand charges. When you add VSD technology to the equation, an operator can often save 25% in energy costs.
Successful harmonics mitigation
With the volume of nonlinear devices continuing to rise, the current waveform has become more complex, sometimes causing disruptions in the power grid in the form of electrical harmonics. One type of technology designed to cancel harmonics is an active front-end VSD. These variable-speed drives optimize the compression process and cancel harmonics by maintaining the perfect compressor speed. For the operator, this means increased production, reliability, and energy efficiency, reduced energy costs, and improved goodwill with the utility.
More efficient process management and monitoring
While the variable-speed drive controls the compressor motor, an integrated programmed logic control (PLC) can manage the package’s process set points, including the inlet and discharge pressures, temperatures, cooling fans, oil lube system, condensate management and vibration, all while recording the trending and run history.
With an integrated package, the operator can control the entire skid locally from the drive’s interface or remotely via a SCADA solution. With SCADA, parameter changes can be managed remotely, saving service calls to the compressor site. These increased efficiencies help to reduce maintenance costs.
Integration means simplicity in setup and support
For all its benefits, an integrated VRU with a variable-speed-driven compressor can be simple in terms of assembly, testing, troubleshooting and maintenance. Integrated VSDs can simplify the controls and improve your efficiencies in production, energy usage and equipment maintenance. They work on a range of gas compression and vacuum applications such as wellhead recovery, gas lift, reinjection and boosting.
Incentives for VFD drives are available from local power providers and from programs that are funded by state and local municipalities and supported by the Department of Energy. Check with your power provider or local agencies to determine what additional funds are available.
MAGAZINE
NEWSLETTER
CONNECT WITH THE TEAM
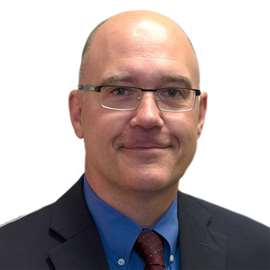
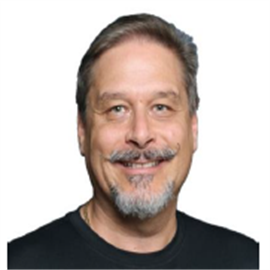
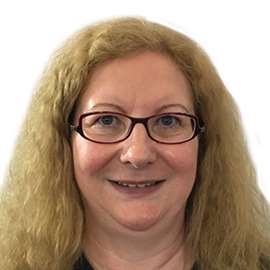