New coupling attenuates vibration in low-emission engines
18 November 2024
In a bid to address the growing demand to reduce the carbon footprint of cranes and other heavy-duty equipment, OEMs are installing leaner, more efficient Stage V/Tier 4 diesel engines that run at lower idle speeds with high torque and have lower CO2 emissions as they consume less fuel. While better for the environment, these power dense engines produce much higher levels of vibration, especially when at idle due to major harmonic order resonance.
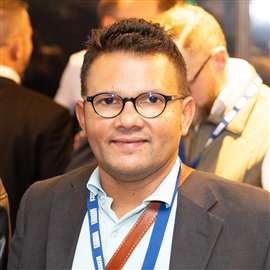
“Higher vibration is always bad, as it causes everything else to suffer, from the pump drive to the gearboxes to the bearings,” said Rene Klimach, engineer and product manager at Regal Rexnord, a U.S.-based powertrain solutions provider.
Couplings are key to attenuating torsional vibration from the engines and ensuring the reliability of powertrain components. However, most flexible couplings are too dynamically stiff for Stage V/Tier 4 engines, said Regal Rexnord, forcing them to be run at higher idle speeds to prevent overload, protect equipment and safeguard uptime – while essentially negating their efficiency benefits.
Crane manufacturer Tadano’s German location found itself facing just such a challenge when it chose to work with its engine supplier to redesign the drivetrain on a large lattice boom crawler crane model. The Stage V engine’s lower idle speed (as low as 600 rpm) and higher vibration risked accelerating wear and tear of vital powertrain components, such as gearboxes and bearings.
With most couplings not designed for speeds under 750 rpm, Tadano approached the engineers at Regal Rexnord to come up with a solution.
Doubling down on vibration control
That solution proved to be the CENTAFLEX-TIR (TIR), a new-generation roller coupling with soft progressive torsional characteristics that Regal Rexnord said can serve numerous complex applications in agriculture, construction, marine, quarries, as well as generator sets with variable speeds.
“The CENTAFLEX-TIR acts as a dampening element between the engine and driven components, effectively absorbing a significant portion of the vibration,” said Klimach. “This allows the entire operation to run at lower idling speeds under high torque demand condition, resulting in reduced fuel consumption and CO2 emissions.”
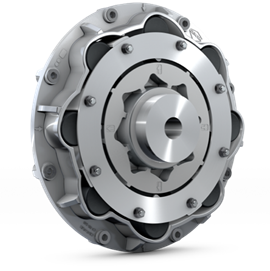
On the surface, the TIR doesn’t look all that “new,” with available sizes and materials used in its construction largely the same as previous couplings. But unlike traditional flexible couplings, the TIR has two lines of flexible rubber rollers rather than a single line.
Dr. Hasan Mahamudul (Dr. Maha), director of R&D at Regal Rexnord, and the chief engineer behind the CENTAFLEX-TIR coupling idea and design, said this dual-stage roller design allows the new coupling “to absorb even more vibration without overheating, thereby increasing its allowable power loss and improving vibration and the lifespan of system components.”
Modified chambers ensure smooth sliding of the rollers. “When you’re applying the lower rpm motor, these rubber rollers will only slide in their chamber,” Dr. Maha said. “So, you will not get any resonance in the driveline. It will be completely resonance free due to its softness, and shift the major order resonance peak in lower rpm.”
The design also enables an 80% improvement in thermal load capacity at higher alternating torques compared to its predecessor, said Regal Rexnord. A corresponding 80% increase in permissible power loss ensures that it effectively absorbs vibration, preventing coupling overload and alternating torque spikes in the powertrain.
In addition, the coupling’s ability to vary dynamic stiffness with changes in mean torque is much smoother and softer compared to conventional designs, Dr. Maha noted. “While conventional designs become progressively stiffer as torque increases, the CF-TIR coupling maintains a softer stiffness even under high mean torque.”
As a result, the TIR provides the torsional softness to withstand idle speeds from 525 to 625 rpm, which are common among Stage V/Tier 4 diesel engines.
Cost and emissions reductions
Dr. Maha describes the TIR as “a very cost-competitive solution and a very simple design.” Yet, it has the potential to impact a number of aspects of both machine design and application.
By implementing the TIR coupling, the company said OEMs may be able to go down in gearbox sizes. Dr. Maha noted that his team is currently working on a pilot project with a customer to increase gearbox life. “But it is slow in progress because the vibration is so low with this coupling, they are thinking to get a [smaller] gearbox.”
Such a step would deliver weight savings and greater overall efficiency, generating cost savings at a system level.
There are other prospective savings, as well. Following its installation in the Tadano lattice boom crawler crane prototype, torsional vibration analysis showed the TIR coupling significantly reduced system vibration and lowered idling speeds from 750 to 650 rpm. This led to an average decrease in diesel consumption of .18 gal./hour (.7 liters/hour). With two engines on the crane, it’s estimated that this will save up to 288 gal. (1,092 liters) of diesel per year, equating to an annual savings of up to $1,900 (1,750 euros).
“It easily pays for the coupling just in fuel savings alone,” said Klimach. “Within a year, you have the… return on investment. That’s interesting for the end user… you have a better savings there because it’s idling lower.”
Then there are the environmental benefits. It’s estimated that the crane will see a reduction in CO2 emissions at a rate of 6.37 lb. (2.89 kg) per year.
“If you burn less fuel in the field, you have a reduction of CO2 emissions,” said Klimach. “And in this certain application, we’re talking about 2.8 tonnes of CO2 emissions per year, which is very interesting for the OEM when it comes to the fleet average emissions.”
Added up, Klimach said, “I think we have a very clear value [proposition] with this product innovation.”
Editor’s Note: Regal Rexnord’s Tadano crane project was a finalist for the 2024 Power Progress Summit Awards’ Off-Highway Product Application of the Year.
MAGAZINE
NEWSLETTER
CONNECT WITH THE TEAM
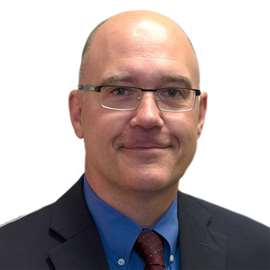
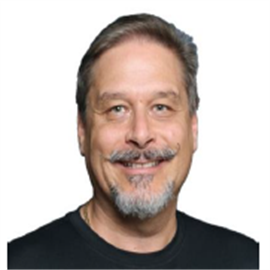
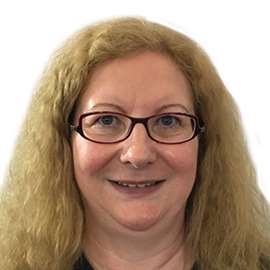