Material Recovery: Balancing profit and sustainability in demolition
14 November 2024
In the evolving world of demolition and recycling, new companies are emerging with a focus on asset recovery and sustainability, reshaping the industry’s approach.
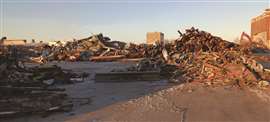
One such example is United States-based SUSA International – an asset recovery and disposition specialist that markets sustainability as a profitable venture, extracting untapped value from materials otherwise destined for landfills.
Their work involves salvaging structural materials like wood, brick, and metals, as well as building contents, including industrial equipment, electrical switchgear, and inventory, for repair, reuse, resale, and recycling – benefitting both the environment and clients.
So, how do these new ‘circular economy’ businesses differ from traditional waste recycling and asset recovery companies in the sector?
Reimagining Demolition and Recycling
Companies like SUSA follow the principle of giving materials a second life rather than sending them to landfill. Geoff Devlin, Member of the Leadership Team at SUSA, explains: “We’re not a demolition company. We specialise in asset monetisation to extract value from every part of the building.”
Geoff says this approach appeals to clients aiming to align projects with sustainability goals, as it doesn’t require choosing between sustainability and profitability.
However, some may view this model as complex. While many materials can be salvaged, the process requires careful planning and often direction from SUSA in terms of separating materials and dismantling structures.
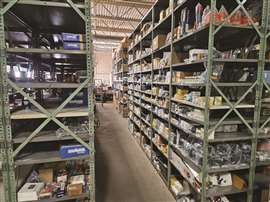
While Geoff acknowledges this, SUSA aims to alleviate much of the contractor’s workload. Not only does the company handle asset removal, but it also manages the labour-intensive sorting, separation, preparation, and storage of most assets before resale.
SUSA operates its own warehouse facilities, where a team researches, dismantles, prepares, and sells smaller, high-value items that shouldn’t necessarily be recycled or reused traditionally. SUSA also manages the ‘distribution’ side of salvaged items, especially when working with more specialised materials.
Balancing Sustainability and Practicality
While pairing profitability with environmental responsibility is commendable, deconstructing buildings to preserve materials can demand more time and resources, which may not always align with a demolition contractor’s priorities or budget. This is partly why some in the deconstruction sector remain sceptical.
Geoff acknowledges this: “Sometimes demolition contractors assume that extracting value from assets means delaying their project or adding complexity. However, the removable/unfixed materials and equipment are usually removed before a demolition permit is even granted, thus having little to no impact on the schedule.”
While even this could be significant for contractors on tight deadlines, the gains from utilising asset recovery specialists can make the extra time worthwhile.
A Case Study
One example is SUSA’s work on the Locke Insulator Factory in Port Covington, Baltimore. Once home to 24 kilns and up to 500 employees, the 15-acre plant manufactured porcelain insulators for General Electric, which bought a stake in it in 1920. Demolition began in 2022, with SUSA coordinating with the demolition and environmental teams.
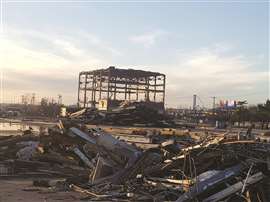
SUSA managed the disposition of all assets, including ferrous and non-ferrous metals, machinery, and reclaimed wood and brick. “It contained all sorts of electrical and historical equipment,” says Geoff. “The brick was antique, and manufacturers actually bought it back because it was cheaper and easier than making new bricks look antique.”
SUSA recovered US$3.5 million for the project owner through asset sales, including a taxable donation that yielded a tax credit. Around 5,000 tonnes of steel, 24 loads of wood timbers, and 1,200 tonnes of brick were salvaged, diverting 1,540 tonnes of material from landfill.
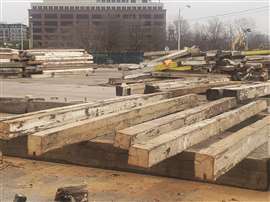
“There’s so much value people don’t even think about,” says Geoff. For instance, SUSA often sells transformers, power distribution units and various components as valuable replacements, rather than recycling them at lower returns.
In the Locke factory case, SUSA was hired by the client and developed an incentive compensation structure with the project’s demolition contractor, ISI Demolition, to preserve wood value. In many cases, however, SUSA is contracted directly by demolition companies as a partner, becoming part of the contractor’s bid.
“Ultimately, demolition contractors believe we can extract more value than they can on their own,” Geoff explains. He adds: “Talking to us early allows us to plan for maximum value, which helps contractors present the most competitive proposal and avoid schedule impact, or incorporate additional time into the schedule if needed.”
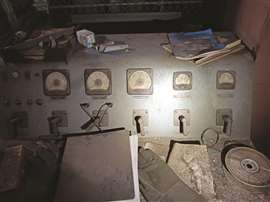
The Asset Recovery Model: Costs and Benefits
For contractors considering companies like SUSA, additional layers of complexity and administration are potential concerns, especially on smaller projects where the added ‘effort’ may not seem worthwhile.
Although financial gains can’t be guaranteed, Geoff highlights a profit-sharing model, where SUSA takes a portion of revenue from asset sales. “We profit-share with our partners,” Geoff explains, emphasising SUSA’s commitment to achieving the best return.
While certain niche items may not yield quick returns, SUSA and other companies like it offer flexibility, allowing contractors or clients to set resale timelines for recovered assets.
“There’s another advantage,” Geoff notes. “We provide detailed, transparent financial and waste diversion reports to clients, so the demolition contractor doesn’t have to.”
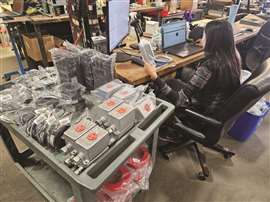
Impact on the Broader Demolition Sector
As regulations tighten and eco-friendly practices gain traction, demolition contractors are increasingly expected to prove their sustainability, including that of their partners. Firms like SUSA, which provide material tracking data could offer greater support in this area.
Additionally, contractors attempting to salvage items like doors, windows, and structural materials face challenges when it comes to reselling them for reuse. This is where companies like SUSA could help establish a more structured marketplace.
The Potential
While it remains uncertain whether this model will be widely adopted, Geoff believes it’s “better for the environment, better for business, and better for the future of the industry.”
Indeed, the future of demolition may well be led by those who can turn waste into wealth.
MAGAZINE
NEWSLETTER
CONNECT WITH THE TEAM
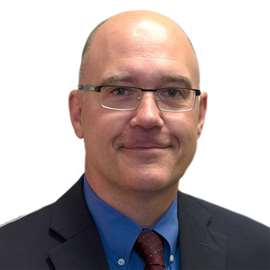
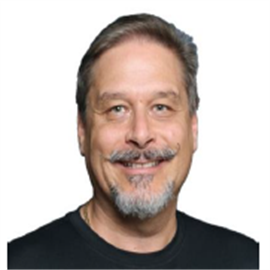
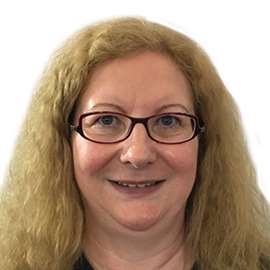