LNG production: Efficiency, compactness and modularity
June 18, 2024
COMPRESSORtech2 talked to Baker Hughes about the latest trends in liquefied natural gas (LNG) production.
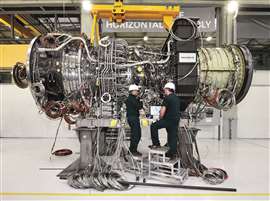
“There is no doubt that demand for LNG is growing. According to Baker Hughes’ estimates, to meet this demand an additional 100/150 MTPA of new projects have to be approved in the next two to three years.” This is Enrico Calamai’s preface to a discussion about trends in LNG production around the world.
Calamai is LNG Strategic & Growth Leader at Baker Hughes and, as an expert in the LNG market, has shared his thoughts and analysis with our editors on more than one occasion.
The latest has been at the Baker Hughes Annual Meeting 2024, held in Florence, Italy, in January 2024. An event that gathered over 2000 participants from all over the world to discuss Energizing Change, not only in the energy industry but also in other industries such as mining, aerospace, and hard-to-abate CO2 emissions sectors such as cement and steel production.
According to Calamari there are more than 800 MTPA of projects at different stages of development in competition to reach FID.
“These projects are segmented in terms of the technology being used for liquefaction, with some major trends emerging,” said Calamai. “For the drivers that operate compressors, we are seeing a shift from heavy-duty gas turbines to more efficient aeroderivative gas turbines and electric motors.” He added that this trend is confirmed also for future projects that aim at reducing emissions.
“In terms of the liquefaction train size, we see that future projects involve smaller solutions in the mid-size range. Larger trains are still being installed for those projects that are already in the works, but they don’t seem to be the preferred solution going forward.” Flexibility is a key element in future installations where growing production needs can be met at a later stage with the addition of more liquefaction trains.
When it comes to project execution, Calamai added that modular solutions are increasingly in demand, and offshore installations are growing.
“The market is very volatile and many projects are started with the intention of capturing a positive phase; in this scenario a quick project execution becomes key and modular construction constitutes an ideal approach.”
Modular solutions are an important area of research and investment for Baker Hughes. One of their latest product developments is the NMBL compact liquefaction module (Editor’s Note: NMBL is pronounced Nimble), which is available up to 1 MTPA and 1.5 MTPA.
The NMBL module solution can be driven by a gas turbine or an electric motor without changing module configuration. The modules are produced and fully tested in Baker Hughes’ operation in Avenza, Italy, and are delivered as plug-and-play modules to the site. This enables greater speed to market: up to two years faster from inception to operation, reducing both site time and on-site personnel.
NMBL is recommended for both onshore and offshore liquefaction and for small to medium-size operations. It is ideal though for remote locations, where Baker Hughes can also offer dedicated power generation options.
“With operations driven by electric motors, we have cases where a reliable power grid is not available and a dedicated power generation solution on-site might be necessary,” said Calamai. “In such instances we can offer our LM9000 gas turbines in simple- or combined-cycle configuration for maximum efficiency.
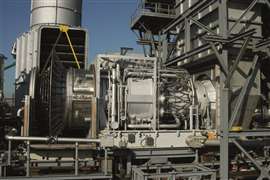
“The LM9000 is an aeroderivative gas turbine and as such is designed for frequent starts and stops. This makes it a reliable solution also in combination with renewable energy sources which are fluctuating by nature.”
Calamai added that Baker Hughes is currently exploring the possibility of a larger NMBL module and is working at improving its supply chain and further reducing delivery and execution time.
Rossella Palmieri, LNG Decarbonization Manager, Baker Hughes, explained that decarbonization is a key concept for Baker Hughes in the LNG value chain, but it applies also to the whole natural gas industry.
In this respect, she outlined three major trends, starting with technology efficiency: “Our aeroderivative gas turbines constitute the backbone of our decarbonization efforts when it comes to technology.”
The LM9000 gas turbine, as an example, reaches 73.5 MW power output with 44% efficiency in simple cycle and up to 56% in combined heat and power cycle. “This gas turbine is very flexible and can be used both in mechanical drive or power generation and is suitable for 50 or 60 Hz frequency applications.”
In general, efficiency can also be improved in brown field projects where Baker Hughes offers upgrade kits for its gas turbines.
“The second trend for decarbonizing natural gas and LNG production is electrification,” said Palmieri. “Baker Hughes made an important step in this direction with the acquisition of Brush Power Generation in 2022, which added electric motors and generators to the company’s portfolio.”
One of the most recent projects that includes Brush Power Generation’s electric motors is the contract with ADNOC Gas signed in October 2023, where Baker Hughes will provide two electric liquefaction systems for the Ruwais LNG project in the United Arab Emirates.
Two Baker Hughes’ LNG liquefaction trains with a capacity of 5 MTPA each, driven by three 75-MW Brush Power Generation electric motors each.
Finally, the last trend for decarbonization looks at new energy solutions. According to Palmieri, some technologies are emerging in the natural gas chain and all its applications – down, mid, and upstream. These include hydrogen; carbon capture, reutilization, and sequestration; integration of renewable power sources; and emissions abatement.
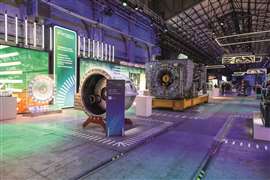
“In addition, CO2 compressors and pumps are the first components that can contribute to CO2 emissions reduction in liquefaction plants,” she said. “Feed gas is pretreated before being liquefied to eliminate CO2 which would otherwise freeze during the process.
“Currently, the captured CO2 is vented into the atmosphere, but customers are increasingly looking at CO2 sequestration to abate emissions.”
Petronas’ Kasawari Carbon Capture and Sequestration (CCS) project, which is being developed off the coast of the state of Sarawak in Malaysia and is expected to be the world’s largest offshore CCS facility, with capacity to reduce CO2 emissions by 3.3 MTPA, is a great example of how these technologies deliver emissions reductions.
Baker Hughes is providing a state-of-the-art compression solution with minimized footprint and weight, as well as a power density allowing for larger flows per unit and best-in-class efficiency. The compressors will be used to enable the transportation and reinjection of the CO2 separated from natural gas into a depleted offshore field via a subsea pipeline.
(Editor’s Note: NMBL is a trademark of Baker Hughes and is pronounced Nimble)
MAGAZINE
NEWSLETTER

CONNECT WITH THE TEAM
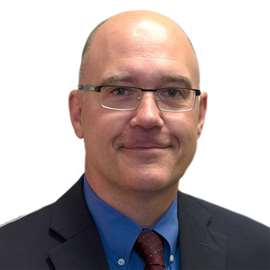
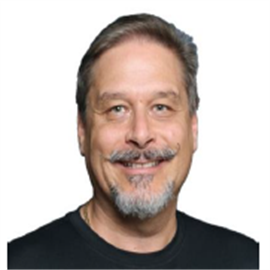
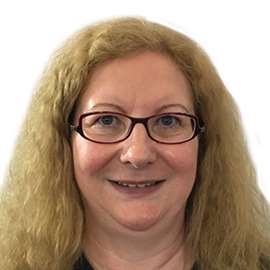
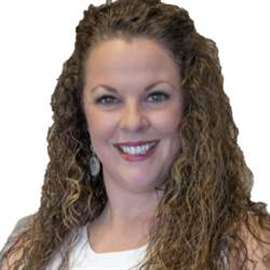