Large-scale CO2-capture project to halve emissions
December 21, 2021

HeidelbergCement Norcem, a Norwegian cement manufacturer, plans to build the world’s first carbon capture facility for large-scale cement production using proprietary technology from Aker Carbon Capture and compression technology from Man Energy Solutions.
HeidelbergCement Norcem plans to capture 400,000 tons of CO2 annually from the cement factory in Brevik, Norway, about half of the factory’s overall emissions. Once completed in the summer of 2024, the carbon will be compressed and liquefied using technologies from Aker Carbon Capture and MAN Energy Solutions. From there, the liquefied CO2 will be transported by ship to an underground storage location, MAN announced.
The cement factory in Brevik will be the first to use the ‘Carbon Capture Heat Recovery’ technology (CCWHR) developed by MAN and Aker Carbon Capture.
A new process allows the heat emerging from the compressor system to be recovered and used as steam to meet approximately one third of the total heat demand from the Aker Carbon Capture plant. Consequently, the system solution demands significantly less energy compared with conventional carbon-capture technologies, MAN said.
“We are delighted to realize the world’s first carbon-capture plant on an industrial scale in a cement-production facility,” said Erik Langholm, executive vice president, projects, at Aker Carbon Capture. “Carbon capture and storage plays a big part in cutting European CO2 emissions, and hard-to-abate industries like the cement sector are integral to our ‘10 in 25’ strategy. Aker Carbon Capture has set a target to secure contracts for capturing 10 million tonnes of CO2 annually by 2025.”
“CO2 emissions are currently unavoidable in cement production with the sector accounting for almost 6 - 7% of the world’s carbon-dioxide emissions. This is why the cement industry is key on the road to a decarbonized future,” added Dr. Uwe Lauber, CEO of MAN Energy Solutions. “We are very proud to be able to deliver such an energy-efficient solution for HeidelbergCement Norcem, which is the result of our successful pioneering work in the CCS field together with Aker Carbon Capture.”
MAN Energy Solutions will supply an electrically-powered compressor train – a type RG 63-7 with integrated CCWHR technology, which allows the compression heat of the recovery compressor to be exploited. The steam generators cool the CO2 mixture between the compressor stages and generate steam that is in turn used for capture.
Alexander Sobolyev, head of standardization & solutions at MAN Energy Solutions, said digital technology has enabled the company to simplify the process of carbon capture and storage (CCS).
“As part of the Norcem project, the digital-twin-based engineering approach of MAN Energy Solutions has led to concrete optimizations. The dynamic process simulation showed that originally planned system components, including heating, valves and additional pipes for safe plant operation, were not required. The time taken for a cold start of the plant can thus be reduced from around 12 hours to 20 minutes – an important characteristic as quick-start capability is always a central criterion for renewable energies,” he said.
MAGAZINE
NEWSLETTER
CONNECT WITH THE TEAM
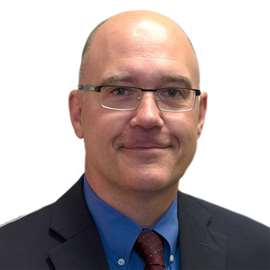
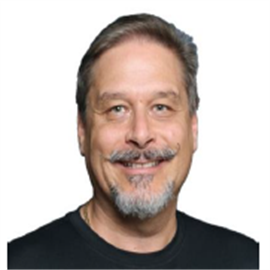
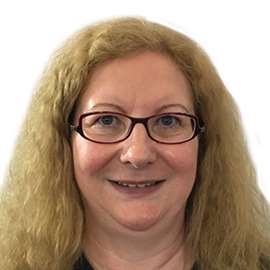