Industry collaborates with specialized compression schools
July 13, 2022

Partnerships are essential for both industry and academia, with clear benefits for both sides. These partnerships give industry access to a skill workers and academia the ability to keep a given curriculum relevant to the evolving needs of industry.
Bob Firth, Dean of School of Engineering & Construction Technologies, at Oklahoma State University Institute of Technology, said the partnerships the school has with its industry partners through Advisory Committees are essential to keep the curriculum relevant.
“They give valuable insight into the industry and the way it is going,” he said.
OSU Institute of Technology, based in in Okmulgee, OK, has the largest two-year associate program in gas compression in the U.S. At any time, there are about 35 students enrolled. The school of Engineer & Construction Technologies has a 92% placement rate. Most of those who do not have jobs upon graduation have decided to pursue advanced degree programs, he said.
The school gives its students a firm grounding in all aspects of the compression industry: compressors, drivers, components, coolers and scrubbers. “We teach everything from the inlet valve to the outlet valve,” he said.
In addition, it requires each student to complete two separate internships. “This gives them the opportunity to practice the trade,” he said.
Younger generation
In general, younger students adapt more readily to technology than a previous generation of students. For this reason, the school is collaborating with Tulsa, Oklahoma-based XALTER to develop a series of virtual reality training modules to give its students insights into how a compressor works and how it is maintained.
The technology includes a VR headset that allows students to see a visualization of a complete compressor in its newest state.
The headset, often called an oculus, allows them to visualize the compressor on a skid, rotate it, turn it upside down and to view it from angles that are sometimes difficult in the real world.
“You can climb into the compressor crankcase and look inside. It’s an excellent visual tool,” he said. “The technology allows students to look inside a compressor before tearing it down, giving them a better sense of what they are about to work on.”
“You can see every inch of it. You can turn it. It will move with you and you can walk into it,” he said.
The technology gives students the freedom to make a mistake while tearing down a compressor without putting themselves or others in danger. In addition, they can put on the headset and have a look at the interior components and understand what it looks like when it’s brand new. They can then compare those images to what they see as they tear down the compressor.
“They can look at the wear patterns, which helps them understand and dig into that more closely.”
Although the students readily embrace the new technology, Firth said it does not replace hands-on instruction from experienced instructors who are industry experts. The school has a range of compressors, drivers and components that give their students the opportunity to put their hands on the equipment and tools needed to maintain it before they go into the field.
A second institution which benefits from partnerships with the compression industry is Panola College, based in Carthage, Texas. Daniel Hall, Department Chair at the School of Energy at Panola College, said the school meets regularly with an advisory board to keep its program relevant. The board includes representatives from all sectors of the energy industry, including Chevron, JW Power Company, Enterprise, DCP Midstream, Eastman Chemical and CSI Compressco.
“We have been fortunate to get all three sections of the energy industry to partner with us,” he said. “They steer us into what they are looking for in a workforce.”
In addition to giving the college guidance on how to keep its program relevant, they routinely recruit from the college. The newest program in Panola’s School of Energy is a two-year associate’s program in natural gas compression, which is designed to produce graduates who can work as entry-level compression mechanics.
The school has a hybrid approach to instruction. It uses online and classroom instruction for lectures and homework. In addition, its technical courses in the energy department rely on an array of equipment, including professional simulators and donated equipment, to give students hands-on experience.
The compression program gives students skills and knowledge of both compression and drivers. The program has a basic and advanced engine course and three levels of instruction for compressors. In addition, it has a series of related supported technical instruction that include valves, alignments, pulleys, bearings and other components.
Panola College has a trailer which is used as a mobile teaching facility and as a recruiting tool to draw the attention of prospective students. When not in use with other programs at the college, Panola uses it as a mobile classroom that can accommodate up to 10 people.
The trailer also allows the college instructors to give specialty classes on safety and other industrial topics. “We’re open to the idea of coming to you and teaching a course,” he said.
Virtual reality as a recruiting tool
Clark White, executive vice president at Targa Resources, said the company encourages training programs for students in an effort to keep ready access to a skilled workforce.
Most of the field technicians in the compression industry who started the industry in the late 70’s boom are now in their mid-60s and are starting to retire. As a result, the company is hiring many younger workers due to retirements and increasing field compression due to increasing gas volumes, he said.
“There is a big need for an influx of new young talent to perform mechanic duties in the field. We’re struggling to find and hire new employees -- and we’re not alone,” White said.
To help train its workforce, Targa is working with XALTER to develop a series of interactive virtual reality training modules to train a young workforce and to keep the skills of an experienced technician sharp. In addition, the technology is a valuable recruiting tool the company can use to draw and train a skilled workforce, he said.
“The younger employees adapt more readily to a virtual reality training module than they do to a classroom setting with a power point presentation,” he said. “We think they learn and develop more quickly with that technology.”
The modules allow a new technician to practice maintenance on an engine before going out into the field. They learn what all the parts are and how they go together, he said.
The modules also teach the steps needed to lock out and tag out a compressor and the steps needed to safely change hot valves. The modules give young technicians the opportunity to make a mistake without putting themselves or others at risk.
“We can run through this and, if they do something wrong, it will simulate what happens, but they don’t get hurt,” he said.
A new age of training
Kodiak Gas Services, a compression services provider based in Montgomery, Texas, has developed an extensive and robust training program designed to bring new employees up to speed quickly and to keep the skills of its current employees sharp.
“We consider training to be a significant investment in our employees,” said Cory Roclawski, Chief Human Resource Officer at Kodiak. “We are proud of our training and development department and the strategic partnership they have with operations.”
The company’s field technicians make up approximately 80% of its workforce and require thorough mechanical, electrical, and troubleshooting skills. Kodiak’s technical training department, led by Melody Shulse, Director of Training and Development, includes in-house technical trainers and an instructional design team to ensure the customized curriculum is cutting-edge and effective. Traditional instructor-led courses offer hands-on training with compressor components, tools, and standard equipment used throughout the industry. Kodiak regularly partners with OEM vendors, like Ariel and CAT, to ensure training courses support the latest and greatest technology. With ESG commitments and sustainability initiatives driving industry innovation, Kodiak recently connected with Hyundai to demonstrate features of their electric drive motor for key Kodiak technicians operating electric engines.
“We have defined the curriculum of technical courses we want our technicians to complete,” Shulse said. “From onboarding our new technicians in a 90-day, competency-driven mentor program, to offering various levels of technical training that grow our employees’ skillsets, we spend a lot of effort to ensure our workforce has the opportunity to develop while they are at Kodiak.”
Historically, trainers travel anywhere between two and four weeks each month to conduct hands-on, instructor-led training at each of Kodiak’s 20+ field offices.
Throughout the pandemic, Kodiak like everyone else, was forced to adjust its training model to accommodate for social distancing. “We were able to shift to remote training and use online platforms to continue training during the pandemic. However, our technicians still prefer the hands-on aspect of learning, rather than passively receiving information via presentation,” Shulse explained. “It was a positive experience to see that it is possible to implement effective alternative methods for training. Even now, we have continued to use remote training for certain classes, due to the accessibility of getting to reach so many from different areas at one time.”
Individuals have different learning styles, and many of the styles have continued to evolve with the younger generation of employees. For example, the younger generation is more comfortable with computer-based training and adapts to it more readily than previous generations. They are also more open to visual learning styles than previous generations.
In addition to its in-house training program, Kodiak partners with several technical schools across the country to ensure their curriculum is fit for purpose and thorough enough for students to develop the skills needed in the compression industry. “We go in as their partner, work alongside the school directors and professors, and then recruit the students to intern or hire on with us after completion of their program,” Roclawski said.
Oklahoma State University’s Institute of Technology, home of the nation’s longest established and largest gas compression program in the nation, is a key partner. Kodiak recently presented the school with a grant to further develop its customized program and demonstrate its commitment to a long-term partnership.
One of the ancillary benefits to this key partnership has been the integration of virtual reality (VR ) into the training and development of both OSUIT and Kodiak. Kodiak recently partnered with Targa Resources and XALTER, a software developer for immersive XR training to create the industry’s first VR training modules. “We are really excited to bring this new technology for learning to our industry,” Shulse said.
New facility
Cooper Machinery Services recently established the Mazerole Training Center, a dedicated training facility in Houston, Texas, to give gas compression professionals essential skills and training. The company offers both customers and employees a range of courses that cover high-speed engines, high-speed compressors, integral engine compressors, and AJAX engine compressors.
The training center is named after Anthony G. Mazerole, who started his career with Cooper in 1988 and had a 30-year career in the industry. The center is designed to educate customers, operators, and maintenance personnel in the specifications, operation, and routine servicing of large-bore, integral and high-speed compression equipment. A well-trained staff is essential to minimize downtime, improve safety and reduce overall operating costs, the company said.
The target audience for the courses include operators, mechanics, technicians, engineers, and maintenance and equipment specialists responsible for the safe operation and care of compression equipment.
Cooper recently hired Charles Ely, formerly of Dresser Rand, and two other instructors to run the center and teach the courses. The instructors have comprehensive theoretical understanding of compression and practical experience with all major drivers and compressors.
Cooper’s training packages include lectures, discussions, hands-on material, student handouts, and a certificate of completion. In addition to its open enrollment workshops, Cooper can provide on-site training that is customized for specific equipment.
ACI SERVICES is offering a free one-day eRCM Pro training session in November, in the Houston, TX area. Free lunch provided. eRCM Pro upgrades and significantly expands upon eRCM – the 20-year industry staple for modeling, tuning, and reconfiguring reciprocating compressors. Please check the ACI website for more details and how to register.
Elliott Group’s turbomachinery training provides the knowledge and confidence that operations and maintenance personnel need to ensure safe, reliable, and efficient equipment operation. Its experienced, full-time technical trainers conduct training programs on steam turbines, centrifugal and axial compressors, expanders, lube and seal systems, and cryogenic pumps and expanders. The company offers training at its facilities, onsite at customer locations around the world, or through its many live, online webinars. Please contact the Technical Training Manager for more information or to inquire about customized training: [email protected]
European programs
Laschet Consulting is a German company for engineering services, technical consulting and special customer training specialized in various areas of drive technology. The training covers the complete range of torsional vibration analysis (TVA), including rotordynamic calculation and evaluation of complete shaft systems in rotating machinery. The training program can be arranged according to the customer’s preferences – also online. Furthermore we offer our annual “International Seminar on ROTORDYNAMICS and FLUID-FILM BEARINGS”. www.laschet.com Laschet Consulting provides customer support mainly for the European market.
Benefit from more than 170 years of experience! LMF offers individual training programs through the LMF Academy - online or at the Academy in Leobersdorf, Austria. Standard training includes basic and advanced mechanical and EI&C courses, as well as hands-on training. Fully customized programs available upon request. For more information please contact [email protected] or visit our website: www.lmf.at.
HOERBIGER offers free, virtual technical training covering a range of compression topics including valve basics, pistons and rings, compressor rod packing and wipers, lubrication, unloading systems, and troubleshooting and maintenance. To learn more, visit www.linkedin.com/company/ hoerbiger or contact us at info-americas@ hoerbiger.com for the company’s current customer webinar training schedule.
Changes to training processes mandated by world events have brought innovation and creativity to the fore, accelerating the use of tools and methods that are likely here to stay. Atlas Copco Gas and Process now trains and supports customers and staff through extensive use of Virtual Reality and remote access tools, including hardware/software to reduce the need for on-site presence.
Examples include the Microsoft Hololens, an augmented reality holographic device that allows a remote Atlas Copco representative to guide an equipment user or service engineer in troubleshooting and diagnosing field issues from anywhere in the world.
Equipment operators can also engage remotely by utilizing Turboview, a mobile app-based tool utilizing a cell phone’s camera to live feed video from the customer’s site to a remote Atlas Copco engineer. In real time the customer can be instructed on troubleshooting and remedial actions, saving time and money while reducing risk of exposure.
Hololens and Turboview support the dual purpose of strengthening customer skills and providing real-time remote field support. Combined with more traditional training methods, Atlas Copco customers experience the best of old and new. Contact [email protected] to learn more.
NEAC Compressor Service offers training and seminars for reciprocating compressors. The training sessions can be held either in the NEAC Training Center located at the NEUMAN & ESSER headquarters close to Aachen, Germany, or at a customer’s location.
NEAC provides project-related sessions or open customer courses. Courses will be done for NEA piston compressors and also for HOFER diaphragm compressors. In addition to the theoretical basics practical exercises are done on compressor components in a workshop area. Depending on the scope of a training also the other NEAC entities in USA, Brazil, Thailand, UAE and Italy offer customer-oriented seminars, all targeting at making operators and maintenance staff familiar with the compressor for safe and proper function. For more see: Training: NEACADEMY (neuman-esser.de)
Miba Industrial Bearings offers customized trainings and support for engineers and maintenance teams at the end user and OE’s on inspection and installation of bearings. Hydrodynamic bearings are a critical part of every rotating equipment including compressors. Many aspects of babbitted bearings have to be understood to allow a safe and efficient installation. Items to inspect before installations, best practice, hot topics like bearing clearance and discussing common mistakes are part of our customized service.
MAGAZINE
NEWSLETTER

CONNECT WITH THE TEAM
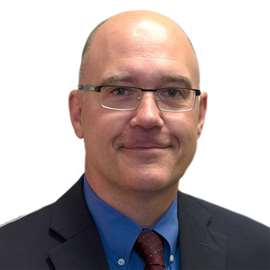
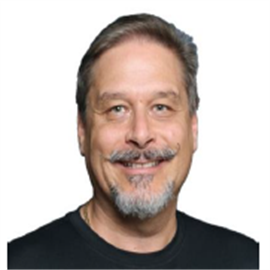
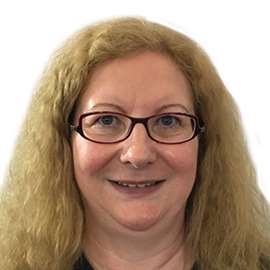
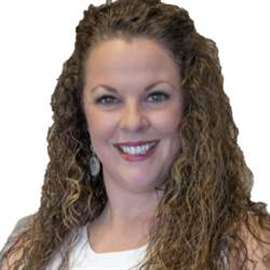