Industrial-grade LED lighting improves safety
July 12, 2021
Employee safety is a primary directive in the oil and gas industry, but despite a multitude of safeguards, accidents still happen. In fact, the industry suffered an average of over 9,300 injuries and more than 100 fatalities annually for a decade, costing companies some $4.2 billion[1], not to mention the toll on workers and their families. While accident and fatality rates are down in recent years, it’s still far from zero, which should always be the goal.
By Fariyal Khanbabi, CEO at Dialight
With the majority of oil and gas facilities still relying on antiquated high-pressure sodium and fluorescent technology, poor visibility is a pervasive problem that contributes directly to workplace accidents[2]. Whether it’s from inadequate light output or frequent fixture failure at the hands of harsh operating conditions, sub-par lighting is a major safety hazard.
Poor lighting is the leading cause of slip and trip incidents, which are the most common cause of lost work day accidents. At one Valero California refinery, poor lighting forced employees to use supplemental portable lighting to conduct equipment maintenance even with a fixture directly above the equipment.
Better lighting has proven to reduce accident rates by as much as 60%, and LED lighting in particular has shown to improve trip-hazard detection by nearly 24% , helping workers detect trip hazards 94% faster[3]. To mitigate the accident risk, Valero installed high-performance LED hazardous location (hazloc) fixtures with precision optics to place more light on the target area compared to its previous HPS fixtures, thus improving visibility where it matters most for workers and eliminating the need for supplemental lighting.
Because the light emitted by HPS, fluorescent and other conventional fixtures are missing large parts of the color spectrum, the resulting illumination causes poor color rendering, making it hard to distinguish colors and making certain colors too dark. At Valero, that meant workers had a difficult time reading and interpreting colored safety placards or identifying color-coded wiring and were forced to use supplemental lighting.
But the new LEDs installed at the facility provide full spectrum light with no gaps in the color spectrum, mimicking natural daylight. This makes for a more natural color rendering and eliminates the need for supplemental lighting for color acuity.
Falls from elevation ranked #1 in OSHA’s Top 10 Most Cited Violations list for the 10th consecutive year, with more than 5,400 fall-protection last year alone. Because of the harsh conditions in oil and gas facilities, conventional fixtures require frequent bulb changes. At Rubis Terminal’s European facilities, that means workers must build scaffolding and work at high elevation in teams of two with portable lighting, just to change lightbulbs—a significant safety risk.
When building its new zero-emissions terminal facility in Rotterdam, The Netherlands, Rubis chose high-efficiency, long-lasting, hazloc certified industrial LED fixtures each backed by 5-, 7- and 10-year warranties. That means Rubis can count on virtually maintenance-free fixtures for many years to come, eliminating the safety risk of frequent lighting maintenance.
Airborne combustibles in oil and gas facilities demand hazloc certified fixtures to prevent the risk of fire or explosion. But using conventional lighting is risky in hazloc applications for two primary reasons: the frequent maintenance necessitates that even sealed fixtures be opened often, creating a combustion risk; and because of the ambient heat they produce, HPS can’t be used in certain Class I Div 1 environments.
By contrast, industrial-grade LED lighting is available in a wide range of form factors suitable and certified for hazloc applications, including Class I Div 1 Groups A, B and C. These fully sealed fixtures offer long-life performance and last up to 3X longer than HPS (with some warranted for up to a decade). These zero-maintenance fixtures have no serviceable parts, so they not only last longer, but also eliminate the risk of opening the fixture in a volatile environment.
In many oil and gas facilities, dirty power can be a problem. Fluctuations in voltage caused by equipment power cycles can result in brown outs and blackouts. Because conventional HPS lights have an extended restrike period of up to several minutes—and even longer in cold weather—power events can plunge facilities into instant, prolonged darkness, even after emergency generators have kicked on, creating a tremendous safety risk for workers.
LEDs, on the other hand, have instant-on capability, which means they provide immediate visibility as soon as backup generators engage, even in sub-zero conditions. That eliminates the prolonged darkness and ensures workers have good visibility even in dirty power situations.
As facilities like Valero and Rubis have discovered, deploying high-performance, long-lasting industrial LED fixtures can substantially improve oil and gas facility visibility. This makes for a much safer and more comfortable environment where workers can perform their jobs with confidence and clarity, and it reduces the financial burden of avoidable safety issues in an industry where so many other unavoidable risks are present.
Upgrading to modern, industrial-grade LED lighting is a smart investment that delivers immediate and long-term ROI in both safety and overall operational efficiency.
MAGAZINE
NEWSLETTER

CONNECT WITH THE TEAM
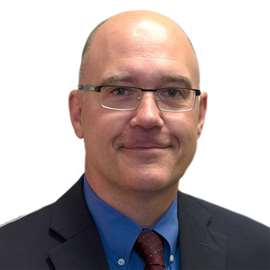
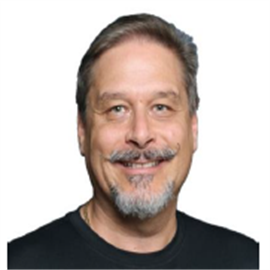
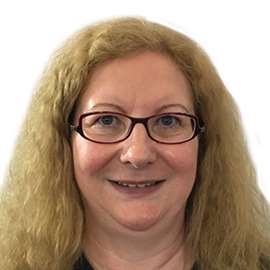
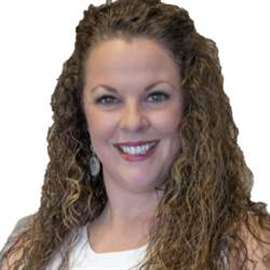