Heat exchangers make a difference
08 March 2023
BU Power Systems developed special heat exchanger in collaboration with COG
BU Power Systems is the official distributor of Perkins engines in sixteen countries in Europe and celebrated in 2022 its 10th anniversary of activity in Italy. Before 2012, the company was a Perkins’ branch.
The know-how and experience the company possesses in the field of diesel engines allows it to look for consistent and innovative solutions that address the specific needs of its customers.
One example is the collaboration BU Power Systems started with Italy-based heat exchange solutions expert COG srl in 2017, for the supply of a specially developed radiator for 8- and 12-cylinder diesel engines, covering about 10 different applications so far.
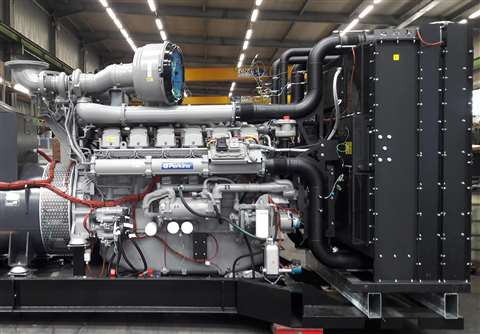
Andrea Botta, BU Power Systems’ application engineer for power generation, explained this project as a necessity to address some performance boundaries for the operation of large gen-sets in critical and demanding ambient conditions.
“COG developed jointly with us a heat exchanger for the power band between 1000 and 2000 kW, which offers more performance and more flexibility in operation compared to the products we had traditionally used,” said Botta. The radiator is available to other Perkins distributors as well.
Giacinto Colucci, Chairman of COG srl, explained: “The heat exchanger we developed for BU Power Systems is an innovative unit delivering top-in-class performances. Development started with the engines’ technical data and the analysis of the ambient conditions that had to be considered.”
He said that gen-sets using large engines are often required to operate in extreme ambient conditions.
“The engines were equipped with a radiator unit capable of operating up to 50°C ambient temperature,” said Colucci. “After years of investments in R&D, engineering and test campaigns, we have developed our high-efficiency heat exchanger technology. Then, following requirements from BU Power Systems and through a careful study of the engine load curves, the heat rejection, and the internal pressure drops across the charge air cooler, we have been able to design and manufacture a product that operates efficiently up to a temperature of 55°C.”
Another requirement for the development of the new heat exchanger was that the gen-set had to fit into a standard container. “Such large gen-sets often have the engine inside the container but a remote cooling circuit. We have been able to guarantee dimensions that allow to fit also the radiator in the container while at the same time guaranteeing the heat dissipation performance (for gen-sets up to 1900 kVA).”
A particular attention has been put also on safety aspects and on easy maintenance that can be carried out while the gen-set is in operation. “Following the field experience driven by BU’s Botta, we studied a solution where greaser plugs for shafts and bearings and the regulation of the belt tensioning are positioned externally, directly on the metal frame of the radiator. This allows to easily carry out basic maintenance operations in the shortest time.”
COG is a vertically integrated company, not only for the manufacturing of its core products – heat exchangers – but also for all related processes (metal framework production, CNC milling and lathing, and so on). “Our production starts from aluminum coils, we do not buy semi-finished components,” said Colucci.
He explained that the philosophy behind COG’s products was initially to offer a competitive alternative to radiators produced in Asia, which are mostly based on a very basic plate and bar technology or on copper and brass cores.
COG develops solutions based on aluminum tube/fin technology as well, which is very competitive in terms of efficiency, quality and price. The company also produces copper and brass units, a mature technology that is nowadays mostly required by the aftermarket. “We target different markets such as off-highway, power generation, heavy-duty on-road, railways, among others,” concluded Colucci.
MAGAZINE
NEWSLETTER
CONNECT WITH THE TEAM
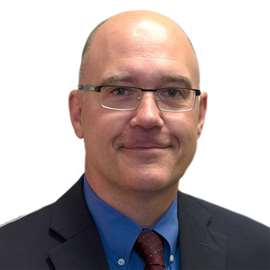
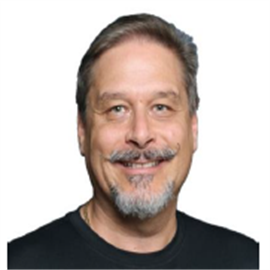
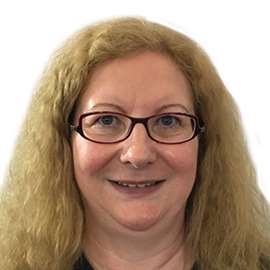