Hardware and software: how the latest crane tech can boost safety and reliability
12 January 2022
Hardware and software alike, the latest technology launched for the crane industry focuses on improving safety and reliability of operations. Niamh Marriot reports.
On site, crane operator safety is obviously a massive priority. Drivers work long hours and navigate difficult and diverse conditions and restrictions. Ohio, USA-based Baker Concrete Construction is one of the latest companies to adopt Crosby’s BlokCam system of camera-based operator assistance devices. Crosby says the crane is at the heart of the construction site and that it’s vital to understand the value of keeping the lifting crew and all site personnel safe and operational. The company say its modular cameras can improve communication and overall awareness during lifting operations.
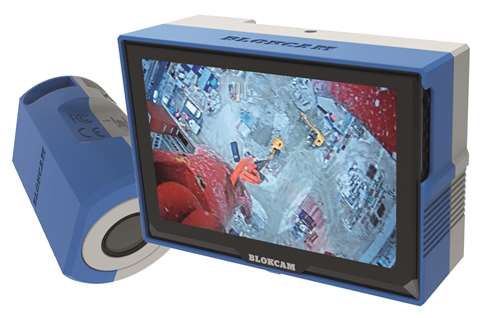
Speaking about the BlokCam system, Mike Arrabi, a crane operator at Baker Concrete Construction, says, “You’re able to see the depth that you’re working with, even in a blind spot. I think all cranes should be mandatory camera-equipped and the Crosby BlokCam product is by far the most advanced system I’ve seen.”
What is the latest technology for crane operations?
Camera systems are installed in more than 85 per cent of tower cranes in the UK, and uptake in the USA is dramatically improving too, according to BlokCam.
The Crosby BlokCam X2 was the industry’s first fully modular system compatible with tower cranes, the company says. Features include an auto-focus lens to always give a clear views of the load and surrounding area beneath the hook (HD 1080p resolution). It also offers users audio from the sensor to the cab and optional single and split-screen modes can be provided with additional cameras. The system can record on loop for up to 30 days.
The Crosby BlokCam M3 is a modular camera for telescopic and mobile cranes and has a HD display with built in speakers, automatic brightness control, and multi-voltage AC and DC inputs. The latest product in the range is BlokAlert, a wireless AV warning system to alert crane operators when workers are in harm’s way. The unit is mounted to the hook block of a crane.
Safety in lifting operations
A new wireless handheld control system has been designed and manufactured by Autec to improve safety in lifting operations. The system can assist a range of hoisting machines, including overhead cranes, jibs, hoists and winches. It can be configured with 4, 6 or 8 two-step pushbuttons and uses both a standard internal and rechargeable Li-ion external battery.

Also recently launched from the Italian manufacturer is a range of monitoring solutions, Autec Vision System (AVS), which can display live video feedback. Wireless control systems with 4.3 inch (110 mm) display screens can be configured in several ways to suit the user. Images, machine data and signals or alarms can be displayed simultaneously, either side by side or overlapping, and up to four video cameras can be employed on the same machine with two simultaneous feeds shown on the display.
Palfinger’s Smart Control
Palfinger’s Smart Control helps operator control the tip of the crane more efficiently and intuitively.
“We want to make working with a loader crane even easier, more efficient and smarter,” says Michael Völker, head of product management loader crane at Palfinger.
The crane tip can be moved vertically or horizontally to the desired position with one lever movement on the radio remote control. With conventional control, this requires several lever movements. The logic of the movements of the new crane control can be processed in the Paltronic control unit. The system autonomously calculates the direction of movement using sensors and electronics. In conjunction with the HPSC-Plus Load function, the truck inclination can also be included and compensated.
When the extension boom system is fully extended, Smart Control calculates the deflection of the position of the boom up to the crane tip and automatically compensates it. The company also offers Flow Sharing which distributes the correct amount of hydraulic oil.
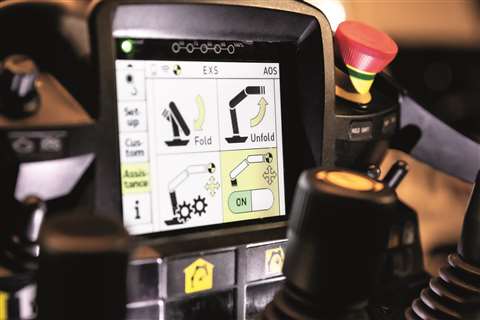
Collaboration can create new technology to improve safety on site. Zyter, a digital health and internet of things (IoT)-enablement platform, has said it is collaborating with Zurich North America, Qualcomm Technologies, Everguard.ai and Rudolph Libbe Group to advance the use of AI-based IoT technologies to enhance construction safety. The goal is to help prevent jobsite incidents and accidents that can result in serious injuries and costly property damage.
How to properly train crane operators
Properly training operators can mitigate risk on site and equip workers with the confidence to handle real world experiences. CM Labs develops portable and accessible training simulators that can be run on its desktop package Vortex Edge Plus, its motion-enabled Vortex Edge Max, and its fully immersive Vortex Advantage, which can all be paired with control levers.
Its latest simulator is the Boom Trick which teaches operators how to deploy and use a digger derrick attachment. It was designed in collaboration with different OEMs to help ensure precision engineering and realistic machine behaviour. Trainees progress through a curriculum developed in consultation with training organisations and the built-in certification exercises ensure operators receive practical training for real world experiences.
Julien Richer-Lanciault, CM Labs’ construction and forestry product manager says, “With the construction industry doing absolutely everything it can to eliminate barriers to training, this is an ideal solution to getting the next generation of skilled labour exposed to the challenges and rewards of a construction career.”
Automation and digitialisation
Lancashire, UK-based CoreRFID has installed its automated safety inspections system, CheckedOK, for Dynamic Safety Solutions Ltd, which has bases across Ireland.
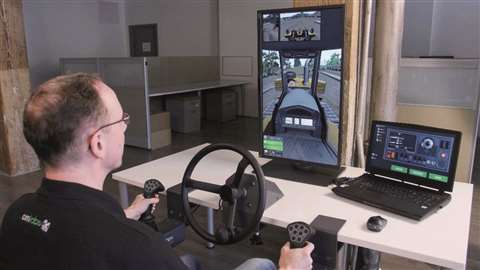
CheckedOK enables equipment inspectors to use a mobile or tablet device to input data onsite. That data is then automatically updated to a secure hosted database, and certification documents are available for online viewing and download. It also assists authorised users meet industry regulations such as LOLER and GA1.
UK-based Capja’s consultancy model intends to digitise all traditional paperwork for cranes – everything from pre work crane checks, operator information, digital signatures and time stamps, to company-branded invoice creation. ICST spoke to Josh Wallman, Capja co-founder and director, who says the pandemic has helped speed up digitalisation adoption. Those who haven’t engaged with it yet should be encouraged to do so, he says. The benefits are vast and can make site operations run much more smoothly. As an internet connection is not always guaranteed on site, the Capja mobile phone app can download relevant information and then work offline throughout a day’s work, uploading all data once in range of Wi-Fi. The company has also recently introduced QR codes for ease of access to secure information.
ANTI COLLISIONThe expansion of the Eurovea complex by JTRE, near the Danube river in Bratislava, is the largest construction project in Slovakia. With three contractors working on the site, Adifex, Strabag and Sytiq, there have been up to 16 Liebherr cranes working at the same time, from self-erecting K series, EC-B flat-top cranes to EC-H high-top cranes. The layout of the construction site is only 300 x 100 metres and some cranes have a common working area with more than five other cranes. Michal Lipák, sales manager at Kranimex says, “It was a challenge to co-ordinate cranes between three companies on such a little area. We chose AMCS Technologies anti-collision systems. It was a big challenge to convince our clients to let us try it on such a complicated jobsite as they were thinking that it will make cranes slower and cost them time, but DCS 61-S with IoT Lifting application provided us with real-time data.” This meant they could show cranes were slowed down or stopped only approximately 3 per cent of its working time. “After installation of the system on the jobsite we didn´t have single collision between cranes. We were able to reduce service cost for the cranes (inspections, damaged ropes etc.). Customers who tried this system once are now using it on all their projects. At this moment we have more than 30 cranes equipped with this system. We are working at many jobsites with more than four cranes and for me there is no better solution to prevent collision of cranes.” |
AUTOMATION NATION![]() Syracuse, an Israeli startup, is developing a system augmenting cranes with autonomous operating capabilities. Its system uses physics and robotic motion algorithms to operate the crane along a certain trajectory. By using a complex set of movements, the company says its system can reduce load transport times by 50 per cent, while ensuring collision-free operation. The system incorporates high-grade, industrial components, including Lidar range sensors and video cameras to generate a real-time 3D digital twin of the job site, that includes the static and dynamic obstacles in the construction site, hook block position, as well as load dimensions and position. The company started development in late 2019 and is backed by Skyline, a large tower crane rental company in Israel. Currently, Syracuse has two prototype systems installed on commercial tower cranes. |
MAGAZINE
NEWSLETTER
CONNECT WITH THE TEAM
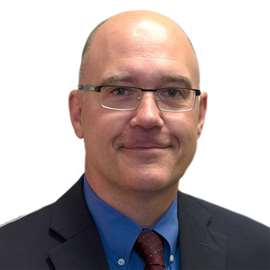
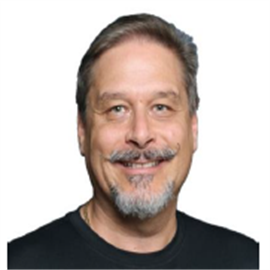
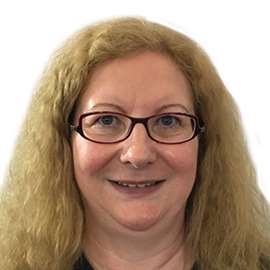