Digital app tracks maintenance
April 21, 2022

The gas compression industry has increasingly turned to digital support applications, partially because of the global pandemic, which has led to many employees working from home.
In response to this growing need for digital applications useful to the gas compression industry, HOERBIGER developed VISTRA, a cloud-based digital spare parts and performance assistant designed to help operators manage compressor parts inventory and maintenance processes.
This digital tool can provide end users more data and better insight into how a compressor, or a fleet of compressors, can be managed in a way that was not previously possible.
The application helps proactively manage compressor spare parts inventory and maintenance and provides important insights to help identify problem or bad actor components more quickly to reduce downtime.
The system gives end users real time, digital track and trace functionality, maintenance documentation and upgrade history.
“VISTRA represents a significant step forward for compressor and fleet uptime optimization with our North American customers,” said Nina Hirsch, Global Product Manager Digital Services with HOERBIGER. “By digitalizing the end-to-end maintenance and repair cycle, we’re making these processes a lot more efficient and are able to provide a higher level of valuable insights that will keep compressors and fleets running at optimal levels for longer periods of time.”
Customers who use VISTRA run the gamut of the energy industry, including rental fleet managers, upstream operators, midstream companies, refineries and gas processing plants. Basically anyone who has a compressor -- or a fleet of them -- to move or process gas.
VISTRA is a global offering but is currently available to end users in the U.S. and Canada.
The system is a software-as-a service system that is easy to install and only requires a web browser on a desktop or a laptop. For operators on the road, an intuitive smartphone application provides the same information readily available at their fingertips. It does not need any additional installation within a company’s computer system.
Once installed, the customer’s fleet of equipment and repair components has to be logged and tagged with a QR code that helps it organize and track components and link them to the company’s repair shops.
It also trains the customers work force on how to use the tools in the application.
Performance analytics
An end user’s compressor configuration gives VISTRA the exact location of components and identifies parts that won’t fit. Only the correct components that fit into a defined configuration can be prepared for maintenance, which simplifies and speeds up the repair process and reduces errors.
The system is more than just a parts tracking system.
“It provides performance analytics on component, compressor and fleet level. We are basically tracking the life cycle of each single component. With that, we can calculate the mean time between repairs of components down to the serial level,” Hirsch said. “By collecting this data over time you get a good overview on the performance of a particular compressor or an entire fleet. It helps you make informed decisions based on that data.”
The system can be applied to any specific make or model of compressor and engine.
HOERBIGER has a strong engineering group that works with customers, monitors repairs and goes through failure modes and is creating reports on quarterly basis. The company’s technicians can go back in front of the customer and see what is failing most often and what they can do to prevent that in the future.
Currently all customers for VISTRA use HOERBIGER for other repair services. For the most part, customers do their own maintenance and then send in components that need to be replaced or reconditioned to HOERBIGER.
The system does not monitor running conditions, temperatures, vibrations or pressures, but it can look at failures and help users establish an optimal repair program. It can also help operators understand where it is spending maintenance dollars on an annual basis.
Kerry Root, Regional Product Manager Digital Services, said VISTRA’s evolution started in November 2018, when a larger market survey that included interviews with industry professionals about potential new products and services in the natural gas industry was launched.
Pilot project
In May 2019, the company created a New Ventures Lab in Vienna. HOERBIGER took the information from the survey and saw a market need for a system which provided better visibility and traceability for compressor repairs and components. HOERBIGER engineers then started from scratch with a new product development approach, working closely with technicians, software developers and other engineering experts to create the interface we see today.
The application’s development proceeded through December 2019, and, by January 2020, it rolled out the first pilot project. Since then, the response from customers has been good and the company has seen steady interest globally. “The interest is definitely rising,” Hirsch said.
The lab also develops new models and tools to make customers’ business more efficient. VISTRA, the digital spare parts and performance assistant, is the first offering of a suite of digital tools to come out of the lab.
“I am proud of the digital focus we have thanks to our New Ventures Lab and am particularly thrilled with VISTRA. It not only marks the beginning of a new era in component repair, documentation and compressor insights, but it was also developed based on pains and needs identified through interviews with industry professionals,” said Wolfgang Sautter, CEO of the HOERBIGER Compression Division.
VISTRA offers multiple benefits for end users. It can eliminate maintenance errors, provide full transparency on inventory and fleet status, facilitate ordering of spare parts and eliminate maintenance delays.
The system helps end users shorten repair times, maximize uptime and helps customers save money by tracking down the exact parts when needed.
“The benefits for the end user are to have an optimum run time of the compressor, to avoid unplanned downtimes, to plan maintenance and to ultimately reduce running costs,” Hirsch said.
By using VISTRA consistently over time, operators gain insight into the status of their fleet and get better information to make informed maintenance decisions. In short, they can proactively manage potential bad components that can increase downtime.
Another benefit is the centralization of repair and component records. Once installed, the system replaces a scattered series of maintenance, repair and inventory records that some operators maintain.
“VISTRA gives you one point of contact and a single source of data for all your maintenance documentation and repairs,” Root said.
MAGAZINE
NEWSLETTER

CONNECT WITH THE TEAM
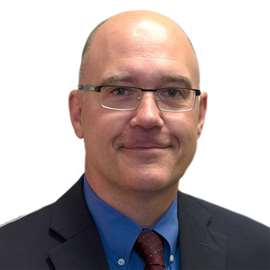
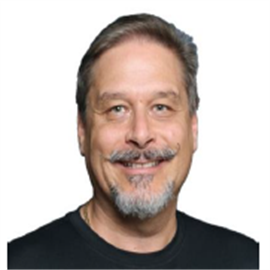
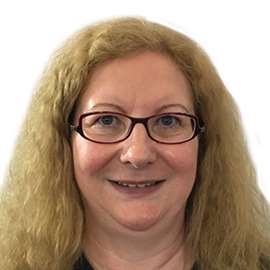
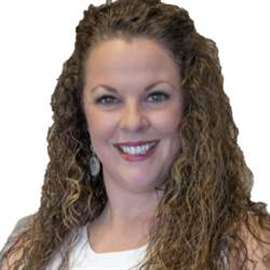