Cornerstones of Compression
June 18, 2024
Fuller Sliding Vane Compressors
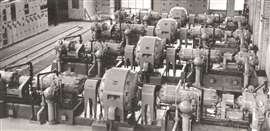
Col. James W. Fuller III founded a company in Catasauqua, Pennsylvania in 1926. The Co. engineered and sold pneumatic conveying systems for fluidic, pulverized, dry materials, principally finished Portland cement and cement raw materials. His original Fuller-Lehigh Co. of Fullerton, Pennsylvania, which developed and patented the Fuller-Kinyon screw pump – a pneumatic pumping system for pulverized coal and dry cement, had been disbanded when Babcock & Wilcox acquired the patent and manufacturing rights for coal conveying.
Continuing to focus on cement plants, Fuller discovered that they did not have sufficient high-pressure air for conveying. So, he decided to build compressors for applications with Fuller-Kinyon pumps. A decision to build water-cooled reciprocating compressors was imminent when a Fuller executive, on a business trip to Europe, became impressed with sliding vane rotary compressors. The compressor design, which had originally been created and patented in Switzerland, was being manufactured by Cie de Machines Pneumatiques Rotatives of Gennevilliers, France.
Compared to reciprocating compressors, the new rotary vane compressor design was compact, light-weight, simple in construction and lower cost. It had negligible vibration, used simple foundations and was pulsation-free. Seeing its many benefits for pneumatic conveying and other applications, Fuller immediately began to develop the technology for both vacuum pump and compressor applications. In 1931, Fuller acquired the exclusive rights to manufacture the compressor in the U.S.

The success of the rotary vane compressor is dependent on physical factors properly interrelated to obtain vane (blade) life of 10,000 hours or more. The original French design utilized thin blades of special alloy steel that required a mating cylinder bore material of hardened steel, usually a liner press-fit into a jacketed cast iron cylinder. Fuller’s team made major improvements to the French design. The first Fuller Co. patent, U.S. no. 1,890,000 granted in 1932, described lubrication of an undercut bore cylinder design, providing for a larger sealing area at the bottom of the cylinder between the high-pressure discharge port and low-pressure inlet port, and a bottom-nested rotor in the cylinder. A patent for a two-stage rotary vane compressor and vacuum pump followed in 1933. Design improvements in 1934 included a high-quality cast iron cylinder and laminated plastic blades, redesigned inlet and outlet ports for improved efficiency and longevity, and improved lubrication and water jacket cooling systems. A 1935 patent described a design to reduce the risk of the rotor expanding into the heads by using a fixed drive end head and floating non-drive end head design, which also improved compressor efficiency.
Compressor production was subcontracted to a conservative quality foundry and machine shop in Manheim, Pennsylvania that produced the compressors to Fuller’s designs and standards. A widespread acceptance of the rotary design occurred during the World War II years. Production orders increased so greatly that Fuller was forced to acquire and enlarge the Manheim foundry and shop in 1946.
Pneumatic conveying of dry cement continued to be an important application for Fuller rotary vane compressors, but in the decade following World War II, the company found many new applications for its compressors. In 1945, Fuller introduced a high-pressure rotary vane compressor for pressure ratings up to 300 psig (20.7 bar). In 1949, it partnered with a major industrial frozen-food system supplier to adapt single-stage rotary vane compressors for ammonia gas, granting them exclusive packaging rights for the Fuller rotary ammonia booster. As a first-stage booster to a second-stage reciprocating compressor, the arrangement greatly reduced the size, cost, and power requirements of commercial frozen storage refrigeration systems. New specialized designs included innovations such as a pressurized dual-shaft seal arrangement and an oil-jacket cooling system to prevent freezing, both of which were soon patented. Thousands of Fuller compressors were produced for ammonia refrigeration in ensuing years.
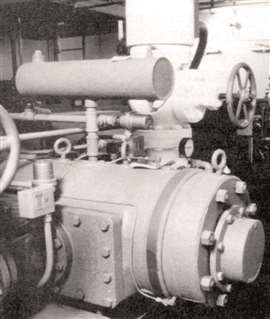
In 1950, Fuller Co. introduced a two-stage vacuum compressor capable of reaching 29.97 in. of Hg (1.015 bar) vacuum. Its exclusive undercut cylinder bore design proved to be critical to its eventual success, allowing for minimal internal leakage and reduced operating temperatures and power consumption. The Fuller Co. was vastly strengthened through its acquisition, in 1954, by General American Transportation Corp. (GATX). Operating as a subsidiary of GATX, Fuller’s engineering and marketing were immediately expanded. Developments continued, especially for ammonia compressors, and by 1962, Fuller marked the sale of its 10,000th compressor. In the period from 1963 to 1970, major improvements were made at the Manheim plant, including expansion of the foundry capacity to 100 tons per month.
In 1968, Fuller introduced a larger rotary vane compressor, capable of more than 3000 inlet cfm (85 m3/min). In 1986, an investment group that included GATX-Fuller management acquired the company. Product development continued, and in 1987, the Co. released a variation of the compressors having a circular bore that enabled higher speeds and capacities within a smaller compressor body.
FLSmidth A/S acquired the company in 1990, and product evolution continued, including introduction of an integral drive option on larger compressor sizes and use of FLSmidth’s carbon fiber vanes that reduced cylinder wear while increasing compressor speed, temperature and pressure capabilities.
The company’s rotary vane compressors found uses in dozens of different applications. In addition to moving bulk solids and ammonia refrigeration, they have been used for transfer of liquids and heavy hydrocarbon gases, providing compressed air, boosting wellhead natural gas, fuel gas and process gases, and for vacuum and vapor recovery services.
Product evolution in the 2000s included improved lubrication systems and an efficiency upgrade that allowed old, costly and inefficient 600 rpm direct drive electric motors to be easily replaced with premium, low-cost 1800 rpm motors without changing the foundations or layouts. More recent developments included improved lubrication systems and PLC controllers with capability for monitoring and controlling compression operations. Along the way, the Fuller compressor line was rebranded and trademarked as the FLSmidth Ful-Vane rotary vane compressor, and it remains an important product of FLSmidth Cement USA Inc.
MAGAZINE
NEWSLETTER
CONNECT WITH THE TEAM
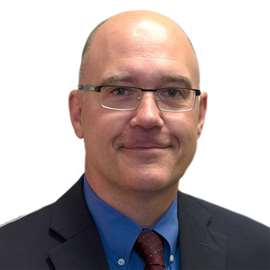
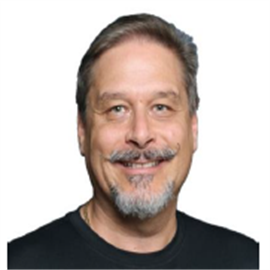
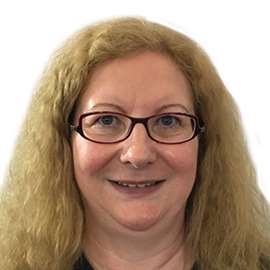