Cornerstones of Compression: The Domestic Engine and Pump Company
October 27, 2022

Near the end of the 19th century, Hagerstown, Maryland bicycle mechanics, Charles and Harry Segner, developed a gasoline engine. The brothers formed the Domestic Engine Company and sold their first 2.5 hp (1.9 kW) air-cooled engine in December 1899. The next engine sold was a water-cooled model in June 1900. In 1901, having perfected their design, they applied for patents for a sparker, feed regulator and governor for “explosive” engines. Their make and break ignition side-shaft engines were designed for domestic farm needs such as sawing wood, churning, separating milk, pumping water and grinding feed, which was a basis for the company’s name.
At the same time, H.M. Etter of Greencastle, Pennsylvania designed and patented a hand pump for farm use. Etter’s pump featured a rack and pinion drive which provided greater mechanical advantage than other pumps then in use. His Etter Pump Company produced the “Etter Easy Running Pump,” which was especially advantageous in areas where water wells were frequently very deep.

In April 1904, J.E. Reisner and several other influential Shippensburg, Pennsylvania citizens purchased Segners’ and Etter’s companies, incorporating them into the Domestic Engine and Pump Company with a new plant to be built in Shippensburg. Reisner was named president, with Charles Segner as general superintendent and Etter leading pump manufacturing for the new enterprise. Production of pumps and engines at the new plant began in early 1905 with a normal work week of 62 hours (10.5 hours on weekdays and 9.5 hours on Saturdays).
Sales increased, more production machines were purchased and additional facilities were soon built. Until the beginning of 1915, the product line still consisted only of Etter pumps and Domestic Type A gas engines. The principal innovation during this period was to use the engine to drive the pump with a belt-driven pump jack, an arrangement that led to a product line of water systems for rural homes.
The first Domestic engines bore no nameplate rating, but were probably 1.5 hp (1.2 kW). By 1908, larger models were being added, and the Type A line ultimately ranged from 1.0 to 12 hp (0.7 to 8.9 kW), with about 10,000 being produced by 1915. Although Type A engine production continued until 1919, the more advanced Type F engine was introduced in 1915. It shared many parts with the Type A, but utilized high tension magnetos and spark plugs instead of the sparker block ignition, and it produced higher output for a given displacement. Type F models ranged from 1.5 to 15 hp (1.2 to 11.2 kW). A vertical engine was also designed and sold as the “Fisherman”, primarily to power fishing boats. In 1915, annual production surged to more than 2000 engines.

However, prior to World War I, most of Domestic’s competitors had switched from side-shaft to less costly cam-driven push rod engine designs. As a result, after 1915 Domestic’s market gradually shifted from agricultural and residential water systems to commercial and industrial uses such as engine-driven pumping and hoisting rigs, many of which were used by heavy construction contractors or in marine applications. Both of these markets, as well as the burgeoning demand for portable air compressors, became core markets for Domestic.
Interestingly, Domestic produced an angle engine-compressor almost two decades before that concept was adopted by larger engine-compressor manufacturers. The first Domestic engine-compressor was introduced before 1916, adapting a 4 in. bore x 4 in. stroke (102 x 102 mm) Type F engine. By 1917, a line of integral units were offered with two or four 5.0 in. bore x 6.0 in. stroke (127 x 152 mm) Type F horizontal engine cylinders and rated at higher speeds than earlier models. Coupled to the engines were one or two 6.0 in. (152 mm) or 6.5 in. (165 mm) bore x 6.0 in. (152 mm) stroke compressor cylinders to provide 50 to 184 cfm (1.4 to 5.2 m3/min.) of air up to 100 psig (6.9 bar). These popular units were produced as complete compressor plants, mounted on trailers or trucks with heavy riveted air receivers that were tested to 250 psig (17.2 bar). Contractors, municipal water companies, city sewage boards, highway maintenance departments, and other customers used them for rock drilling, structural steel riveting and chipping, concrete cutting and breaking, pneumatic picking and spading, and tamping.
By the late 1920s with many competitors, Domestic’s single-cylinder engine production gradually diminished to units equipped with direct coupled high-pressure force pumps or diaphragm, mud or trash pumps intended for pumping services in construction, quarrying and farming operations. Most engine manufacturing ceased prior to World War II. Total engine production exceeded 30,000 units from 1905 until the last unit shipped in 1952. Many Domestic-built engines bore the nameplates of other sellers, such as Bond, Leader, Schramm and Rider-Ericsson.

However, 1917, Domestic had patented and produced a vertical lift, poppet valve type diaphragm pump. Other types of reciprocating pumps followed, and by the late 1920s, these were increasingly driven by larger Waukesha or LeROI gasoline engines, as Domestic transitioned into becoming a significant manufacturer of pumps. The product line continued to grow to include sludge pumps, caisson pumps, plunger or high-pressure pumps, sump pumps, non-clog sewage pumps and hoists until 1936 when the company bought the manufacturing rights to the Ames line of vacuum and condensation pumps. By 1947, this redesigned and extended line had become Domestic’s principal product. During WWII, Domestic designed and manufactured large quantities of centrifugal pumps, used for water purification by the U.S. Marine Corps.
Charles Segner, vice-president and general manager, died unexpectedly in 1936, as did Harry Segner, plant superintendent, in 1937. Reisner remained president and chairman of the board until 1947, when the company was sold to Empire Industries. Notably, the company was still manufacturing H.M. Etter’s original pump at the time of his death in 1949 at the age of 90. In 1972, ITT bought the Domestic Engine and Pump Co. and changed the name of the operation to ITT Domestic Pump.

MAGAZINE
NEWSLETTER
CONNECT WITH THE TEAM
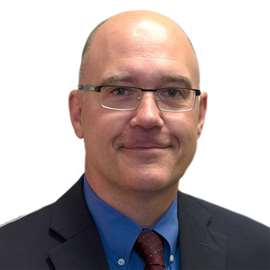
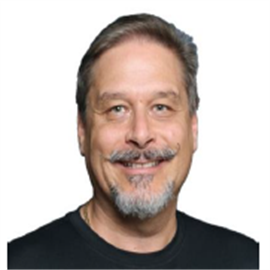
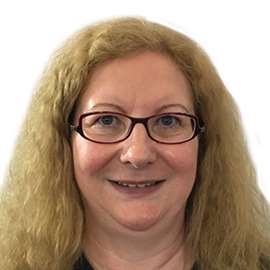