Cornerstones of Compression: The Cooper-Bessemer free piston engine
December 19, 2023
Cornerstones Corollary: Great ideas that didn’t make it!

The Cornerstones of Compression series has highlighted many significant products and companies over more than 160 years of continuous progress. However, there were also some great engine and compressor ideas that were unsuccessful.
In the 1950s, Cooper-Bessemer (C-B), well into its 2nd century of business, faced a seemingly overwhelming challenge from the General Electric (GE) combustion gas turbine that was wedging progressively deeper into the gas pipeline market. GE’s turbine driven centrifugal compressor concept appeared certain to overtake the reciprocating integral engine-compressor for use in pipelines, and C-B’s own recently developed centrifugal compressor could not check the swelling tide of competition.
The cost of steel pipe made it desirable to have the compressor stations spaced closer together to keep all the pipe “full”. In the larger lines, compressor stations were going to be spaced about 30 to 50 miles apart, so the pressure drop from one station to the next would be small enough that a centrifugal compressor could be used to boost the pressure from station to station.
Serious threat
After El Paso Pipeline Co. purchased 19 GE turbine driven centrifugals for its pipeline in the southwest U.S., C-B knew that its big integral engine-compressor market had a serious threat. C-B countered by offering its large four-cycle LSV gas engines with speed increasing gears as drivers, but gas turbines continued to gain favor with the pipelines.
C-B’s chief engineer, Ralph Boyer, later reflected that the only way that he could see to beat them and do it in a reasonable time was with a piston engine, and that was a serious mistake. He said that the company president made it his business every day to come to Boyer’s desk and say, “what the hell are you doing about a gas turbine engine.” Knowing little about gas turbines, and also having a long history of building diesel engines for marine applications, it was natural for C-B to investigate a new idea that the U.S. Navy was interested in.

The free-piston engine concept emerged in Europe in the late 1920s, but experienced minimal commercial success. Interest resumed after World War II. Using opposed horizontal pistons that were mechanically linked to ensure symmetric motion, the concept provided some advantages over conventional technology, including compactness and a vibration-free design. C-B and the Navy viewed the free-piston engine as having the high thermal efficiency qualities of the reciprocating internal combustion engine and, as a hot gas generator driving a power turbine, providing higher rotating speeds than conventional engines. C-B also viewed it as the perfect solution for the gas pipeline market.
Significant challenges
As the piston motion between the endpoints was not mechanically restricted by a crank mechanism, the free-piston engine had the valuable feature of variable compression ratio, which could provide operational optimization, higher part load efficiency and possible multi-fuel operation. Variable stroke length was achievable using a frequency control scheme in which piston motion was paused at bottom-dead-center (BDC) using a controllable hydraulic cylinder as a rebound device. The frequency could therefore be controlled by applying a pause between the time the piston reached BDC and the release of compression energy for the next stroke. Since there were fewer moving parts, the purely liner motion reduced frictional losses, and manufacturing cost were less. It was expected that the simple and compact design would therefore require less maintenance and provide increased lifetime over conventional engines.

However, its unique features also presented significant challenges that had to be overcome in order for it to be a realistic alternative to conventional technology. Accurately controlling the position of the piston dead centers was the biggest challenge, as this was necessary in order to ensure fuel ignition and efficient combustion, avoid excessive in-cylinder pressures and avoid the pistons violently slamming into the cylinder heads. And without an energy storage device, such as a flywheel, if the engine failed to build up sufficient compression or if other factors influenced the injection or ignition and combustion, the engine could stall and stop. This resulted in misfiring and a need for accurate speed control.
Serious flaws
C-B began laboratory testing of a free-piston engine in January 1952, first operating on diesel fuel. A 1953 ASME paper provided some insight into the highly proprietary and secretive development with the U.S. Navy. The two opposed throws each had an inboard 14 in. (356 mm) diameter two-cycle power cylinder and an outboard compressor cylinder bore of 37 in. (940 mm). Both the power and air scavenging cylinders were single-acting with a net stroke of 18.5 in. (470 mm). Operating at about 555 cpm, the engine produced the equivalent of 1750 hp (1305 kW) of hot gas energy at 1000°F (538°C) with a 45% thermal efficiency. The paper stated that there was no necessity for governing the reverse bounce of the pistons, since the pressure in the bounce and the compressor rear spaces were automatically controlled. The bounce air supply was taken from the scavenge air. A single pair of racks connected the two piston assemblies.
C-B intended to provide a 5000 hp (3729 kW) prime mover by using three free-piston hot gas generators operating in parallel to drive a single multi-stage axial power turbine. However, the challenges of consistently smooth combustion with natural gas proved to be much more challenging than diesel, and development progress crept along at a slower pace than C-B could afford. By 1955, C-B concluded that the free-piston concept had serious flaws that could not be overcome. It never made it out of development, and the program was scuttled by 1957.
Fortunately, the company saw a potential for development of yet another novel prime mover, and it secretly began evaluation of the jet (aircraft derivative) gas turbine concept in early 1956. By 1960, it introduced the world’s first jet gas turbine successfully driving a C-B centrifugal compressor at a Columbia Gulf gas pipeline station (see COMPRESSORTech2, July 2013). This enabled it to remain a leader in pipeline compression for many more decades.

MAGAZINE
NEWSLETTER

CONNECT WITH THE TEAM
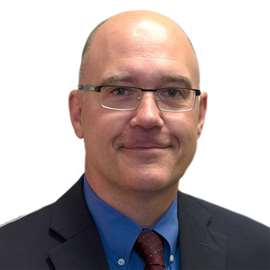
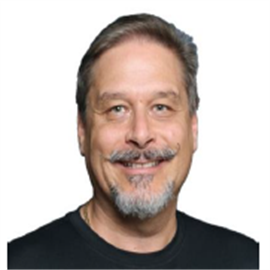
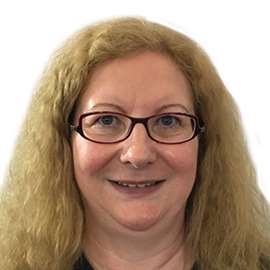
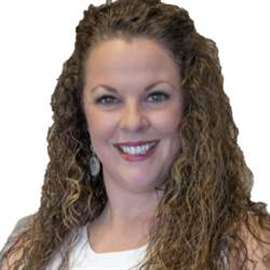