Cornerstones of Compression: Liquid Ring Compressors
August 29, 2023
Pioneer Nash has produced this unique product for more than a century.
The liquid-ring pump is an unusual machine that can also be used as an air or gas compressor. The first liquid-ring pump appeared in 1903 with a patent granted to Siemens-Schuckertwerke in Germany. Siemens manufactured liquid ring pumps under the Elmo brand name for a century for many industries and applications.

The first U.S. patent was filed by Lewis H. Nash in 1910. Nash, an apprenticed machinist and graduate engineer, was a prolific inventor. While still in school, he designed a new type of water measuring device. After graduation, Nash went to work at the National Meter Company in Brooklyn, NY, where he received over 60 patents for water meters and a comparable number for gas engines that the company manufactured. Although he was chief engineer, Nash’s relationship with National Meter was not always the best. The company did not prosecute infringements on his gas engine patents, and his efforts were underappreciated. Many of his developments were not pushed and his authority was continuously curtailed.
At the age of 53, when Nash conceived the idea of a new type of vacuum pump, he decided not to assign the patents to the National Meter Company. In 1905, he established the Nash Engineering Company (NEC) in Brooklyn to manufacture the product himself. But, being a native of Norwalk, CT, in 1908 Nash moved the firm to a small shop there, where it manufactured air pumps. After three years of development and testing, he patented his first designs for several liquid ring vacuum pumps and compressors used in steam heating and sewage systems. Facilities soon expanded significantly to support increased production of these products.
A 1914 ASME product catalogue characterized NEC as the exclusive manufacturer of hydro-turbine air compressors and vacuum pumps and it provided a description of the machines. “Casing, head and rotor constitute the entire compressor or vacuum pump. Note the absence of gears, valves, loose-moving or reciprocating parts. The rotor runs with a large clearance. All strains due to compression are removed from the shaft and bearings because the air is compressed simultaneously on opposite sides of the rotor. The water follows the case due to centrifugal force. Twice in a revolution, the water recedes from the rotor thereby leaving spaces between the blades into which air is drawn through the inlet ports. The water then surges back into the rotor, compressing and delivering the air through the outlet ports. The simplicity of the Nash hydro-turbine principle means a high-grade air compressor and vacuum pump at a reasonable price; a compressor which can be operated by anyone; a compressor which will run continuously on 24-hour service with undiminished efficiency. The air is delivered without pulsation. No air receiver is required. The space occupied is less than that of any other compressor of the same capacity. No elaborate foundations are necessary. There is no vibration or noise. Absolute reliability, durability and constant high efficiency is assured. The air is thoroughly washed by the water in passing through the pump, and is delivered entirely free from hydrocarbon compounds due to the decomposition of the lubricant. This puts the pump in a class by itself for agitating liquids, particularly cyanide solutions, for exhausting from gas producers, for air pressure filtration, and any process requiring clean air.”
After graduating with engineering degrees, Nash’s two sons joined the business. This allowed Nash to spend most of his time in his laboratory, where he could work out his many inventions and ideas. In 1922, he even ventured into politics, being elected representative to the Connecticut State Legislature. By the time of Nash’s death in 1923, NEC had grown to be a prosperous, well-established concern.

NEC went on to develop complete vacuum steam heating systems and vacuum sewage collection systems for many of the growing U.S. cities, as well as vacuum pumps used in other industries. This work continued into the early 1960s, whereupon the firm shifted away from the fields of commercial heating and sewage toward a focus on industrial machinery, such as vacuum pumps for paper, power, petrochemical, and food processing. By then, the Norwalk site had grown to more than 110,000 ft2 (10,220 m2) with more than 800 employees. Additional production facilities were established in several other countries. In 1995, operations were moved to Trumbull, CT.
Meanwhile, in 2000, Siemens spun off its liquid ring pump and compressor business to form Elmo Vacuum Technology. In 2002, that business merged with the Nash Engineering Company to form Nash Elmo, which was subsequently acquired by Gardner Denver in 2004. In 2012, Nash operations were moved to a new facility in Bentleyville, PA., where the company continues to operate today as a division of Ingersoll-Rand.
The original liquid ring compressor’s pressure capability was limited to a few psig. However, over time, discharge pressure ratings were increased to 30 psig (2.1 bar) for lower pressure models all the way to 200 psig (13.8 bar) for higher pressure models. Multistage liquid-ring systems were also built employing two compression stages on a common shaft. Modern units are built for inlet flows ranging from about 30 cfm (0.8 m3/min) to 9400 cfm (266 m3/min) or more. Compressors have been made from stainless steel, ductile iron, and other materials for compatibility with dirty, toxic, explosive, and corrosive gases.
MAGAZINE
NEWSLETTER

CONNECT WITH THE TEAM
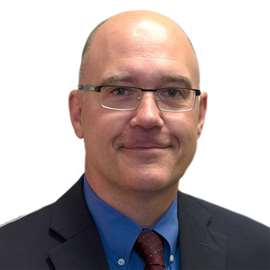
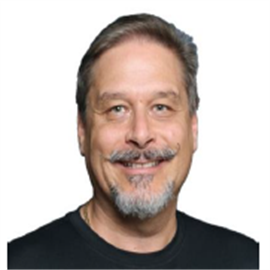
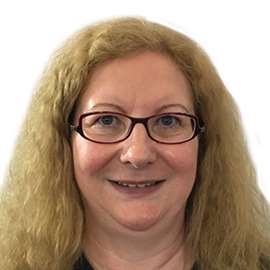
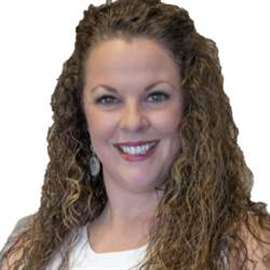