Cornerstones of Compression: Air compressor evolution
February 03, 2025
This continues a series of Cornerstones of Compression corollary articles that provide an historical look at the industries that drove the invention and technological evolution of compressors and supported the growth and development of the industries that depended on them. This issue reviews some early advances in piston rod packing and compressor valves that enabled higher compressor operating speeds and pressures.
Advances in Piston Rod Packing
Providing a seal around the reciprocating piston rod was a requirement for steam engines since their inception. Seals were also required on reciprocating compressor piston rods, which were becoming common in the latter half of the 19th century. Various washers, made of materials such as pork rinds, hemp, duck, rubber, metal foil, metal shreds and innumerable combinations of these materials, were “stuffed” or “packed” around the piston rods and held in place and compressed against the rod by a stuffing box. These required regular tightening of the stuffing box bolting to control leakage as the packing material wore away. Early metallic packing appeared in the form of wedge-shaped pieces of some type of soft metal so arranged that pressure from the bolted flange caused them to press on the piston rod. There were many variations of this design investigated during this period but, like their predecessors, they required continual maintenance, consumed engine power, and rapidly wore and scored the piston rods.
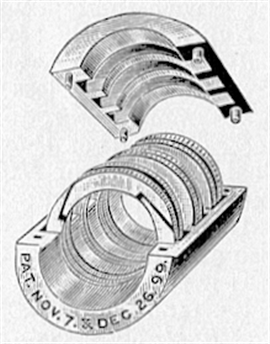
Adam W. France, an operating steam engineer in Philadelphia, Pennsylvania, experimented with various designs, ultimately developing a tangent-cut cast iron packing design that he patented in 1899. Fig. 1 shows an early France piston rod packing case with the tangent-cut rings. This full-floating metallic packing allowed the sealing elements to move freely within the assembly as opposed to non-floating packings in which the sealing elements were held rigidly in the stuffing box and required outside adjustment to compensate for wear or misalignment. The full floating metallic packing eliminated friction-producing packing materials. Further, the anti-friction metal sealing rings withstood high temperatures and pressures. And they provided an effective seal on piston rods that moved laterally as they stroked through the packing due to wear of the cross head or cylinder, unequal expansion of the parts, misalignment, or innumerable other causes.
Similar packing developments were made by O.J. Garlock at about the same time; and Charles Lee Cook also introduced several patents that improved piston rod packing. All three men went on to develop their own successful packing and sealing companies. The development of this type of piston rod packing was a critical step that eliminated a key barrier to increasing the speed and operating pressure of reciprocating compressors.
Advances in Compressor Valves
Early reciprocating compressors used heavy metal poppet valves or various mechanically-actuated valves, including Corliss valves, which were controlled by cams and linkages, similar to the steam engines that drove the compressor cylinders. They were heavy, noisy and short lived. In the early 1900s, technological advancements were resulting in higher speed engines and compressors, but the compressor valve technology was limiting reliability and performance. In 1905, an effort to overcome these limitations, Laidlaw-Dunn-Gordon, which had merged with Worthington in 1899, developed an arrangement called the Cincinnati air valve gear. It afforded a mechanical opening and closing of an inlet valve, and a mechanical closing of a discharge valve, all of which resulted in a higher speed, quieter running and more efficient compressor. The gear was only suitable for large machines and, though costly, was effective and widely used.
Innovative plate valves were first conceived by Hanns Hörbiger in Austria in 1895. Hörbiger began working with engineer Friedrich Wilhelm Rogler in 1900, and their new steel plate valves were shown to overcome all the disadvantages of valve designs that were common at the time, enabling the advancement of blast air compressor technology in Europe.
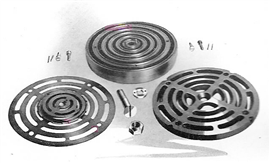
In the U.S., a period of rapid compressor valve innovation occurred between 1910 and 1920. In 1911, Lorenze Iversen, chief engineer for the Mesta Machine Company of West Homestead, Pennsylvania, patented an automatic plate valve for blowing engines. The Mesta automatic plate valve, shown in Fig. 2, soon became the standard, not only for Mesta, but for many other compressor companies that licensed the Mesta valve technology for air, gas and refrigeration compressors. Fig. 3 shows the wide range of valve sizes that Mesta manufactured.
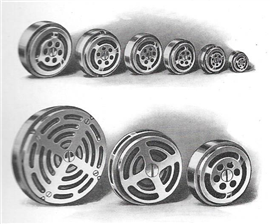
In 1913-1914, Chicago Pneumatic developed the Simplate valve that was used in its compressors for many decades. In 1914, Ingersoll-Rand began introducing new compressors with the “Rogler” valve, shown in Fig. 4, that was based on the earlier Hörbiger invention.
One of Laidlaw-Dunn-Gordon’s most noteworthy compressor advancements occurred in 1915 when it introduced the feather valve, which was actually patented in 1912. This valve, shown in Fig. 5, was so simple, noiseless, efficient and durable, and so universally applicable, that it at once made practically obsolete all old-time poppet valve type compressors. The Laidlaw-Dunn-Gordon feather valve became a staple of Worthington compressors for decades.
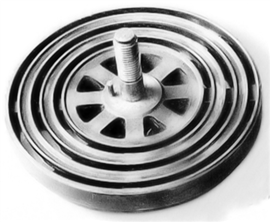
In c.1916, the Bury Compressor Company of Erie, Pennsylvania patented the Universal Pyramid box plate valve, shown in Fig. 6. This was described as having 50% more area than any other valve used and being “durable as the pyramids; silent as the sphinx.”
All of these valves included a means of cushioning and they worked on differential pressure, rather than relying on mechanical actuation. And they had less resistance, and therefore higher efficiency, than heavy metal poppet valves. These early 20th century valve and packing technologies remained prevalent through the 1970s, when the availability of engineered plastic materials again led to developments that enabled reliable compressor operation at even higher speeds.
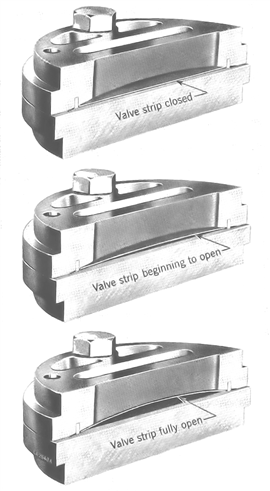
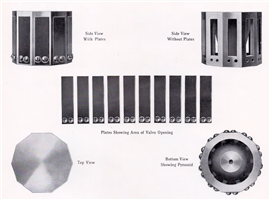
The next issue will complete this brief series on the evolution of industrial air compressors.
MAGAZINE
NEWSLETTER

CONNECT WITH THE TEAM
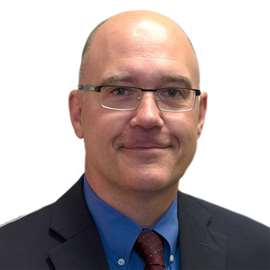
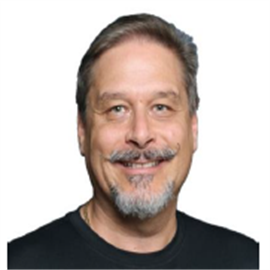
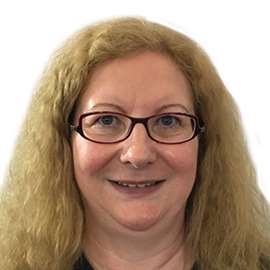
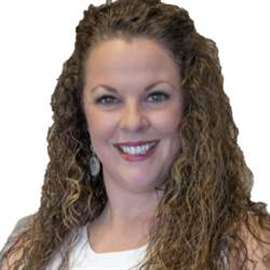