Caterpillar to show technology, equipment at MINExpo
18 September 2024
New Cat Dynamic Energy Transfer (DET) solution included on stand
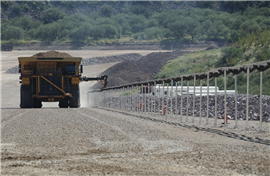
Caterpillar said its MINExpo 2024 stand will immerse visitors into the mine site of the future; showing technology for an energy transition and customized solutions designed to increase customers’ efficiency, safety and profitability. The planned 2024 exhibit will showcase Caterpillar’s work with autonomy and automation and its progress in greenhouse gas reduction technologies.
“Caterpillar’s legacy is to deliver an exceptional experience at every job site through customer focused solutions and services,” said Denise Johnson, Caterpillar Resource Industries’ group president. “As our exhibit shows, together with our customers, we are mining better, smarter and safer. And this is just the beginning of our closer-than-ever before collaborations with customers.”
The Caterpillar MINExpo experience will showcase the company’s latest innovations to support the energy transition, including the recently announced Cat Dynamic Energy Transfer (DET), a solution it said will help solve one of the most complex aspects of the mining industry’s energy transition – energy management.
Cat DET
DET is a fully Caterpillar-developed system that can transfer energy to diesel-electric and battery-electric large mining trucks while they are working around a mine site. It can also charge a machine’s batteries while operating with increased speed on grade, improving operational efficiency and machine uptime. The Cat DET system provides the industry with options to support both near-term and long-term sustainability strategies.
“We believe Cat DET provides a technological leap for the mining industry. Our team of innovators designed this system to provide immediate benefit to miners who want to lower their operating costs and greenhouse gas emissions today while also creating flexibility for the future,” said Denise Johnson, Caterpillar’s Resource Industries group president. “We know customers need choices to fit their unique site objectives. We are proud to deliver an innovative, integrated solution that can support their needs of today and those of the future.”
Cat DET is comprised of a series of integrated elements, including a power module that converts energy from a mine site’s power source, an electrified rail system to transmit the energy and a machine system to transfer the energy to the truck’s powertrain.
The company said the rail system is a highly deployable, mobile solution that can be customized to customers’ site layouts, including high-speed and curved haul roads. The connecting arm can be installed on either side of a truck and on multiple truck models, providing options to fit customers’ specific operations. It can also be used on mature or developing sites, and it can be easily moved or expanded to allow maximum mine site coverage.
Cat DET will integrate with the Cat MineStar Command for hauling solution, merging autonomy and electrification technologies to provide a holistic site solution.
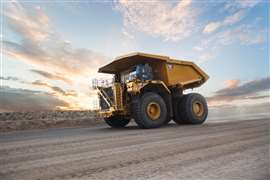
Optimizing through technology
From fleet management to fully autonomous machine operation, Cat MineStar provides building block technology packages that are scalable to meet the mining operation’s needs as it moves along the technology integration journey. Visitors will be able to experience interactive engagement with MineStar fleet management solutions for both surface and underground operations at the exhibit’s conversation stations. A third station allows attendees to explore precision mining solutions dedicated to site optimization.
Every piece of equipment that will be on the show floor is infused with various levels of technology, said Caterpillar. In addition to the ultra-class 798 AC featuring Command for hauling, the R2900 XE LHD will be equipped with Cat MineStar Command for underground that enables remote machine operation. The diesel-electric LHD will also feature MineStar Detect for underground to safeguard against unintended interactions between personnel and assets and enhance operator alertness, both enhancing operating safety.
Caterpillar will launch two new technology offerings to the MineStar ecosystem at the show:
Delivering the next layer of safety, Collision Awareness System (CAS) is a site-wide solution that uses the latest in technology advancements to enhance situational awareness by warning operators of potential machine interactions before they have a chance to happen. CAS will be highlighted on the 995 and 798.
A new office application for Terrain Payload Management expands the payload tracking technology to Cat Electric Rope Shovels and Draglines.
Virtual reality experiences will allow attendees to “get into the cab” of the Cat 7495 electric rope shovel and 6060 hHydraulic mining shovel. Showcasing the capabilities of Cat Command technology, two remote operating stations will give visitors the chance to operate a dozer or rotary blasthole drill located hundreds of miles away from the Caterpillar exhibit. A third station will offer simulations of Cat Command for underground, demonstrating the technology’s versatility and ease of use.
“Customers will experience our latest technology innovations and autonomous developments throughout the Caterpillar show floor at MINExpo,” said Sean McGinnis, vice president and general manager of technology and global sales support for Caterpillar. “Mine site automation makes significant impacts in operations and not just with autonomous haulage. Today, we have customers around the world utilizing our autonomous solutions for drilling, loading, dozing, hauling and underground, and we are working with many customers to develop the autonomous sites of tomorrow.”
Support beyond the sale
The in-booth Caterpillar service bay and nearby displays will highlight options available to mining customers for maintaining the machinery and meeting production targets. Track pad displays for rope and hydraulic shovels and dozers will show the latest offerings designed to maximize undercarriage life.
Demonstrating the ways Cat dealers keep machines operating , attendees will be able to step inside a service van, which makes customized hose and couplings on site. The van offers the capabilities of quickly returning a machine to service by making the necessary size and length of the hose for repair.
Conversation stations allow team members to engage with customers on a range of topics including, but not limited to: repair options, parts and component remanufacturing, machine rebuilds, various truck body options, and bucket choices. Also, a range of 3D printed parts will be on display along with multiple engine exhibits, including the Cat C32 Reman, C32 core, upgraded 3512 E and C175 cutaway.
Spanning machines to technology to services, Cat Job Site Solutions ties everything together with customized, scalable solutions that are results driven. Team members will meet with attendees to demonstrate how, working with the dealer, Cat Job Site Solutions provides a strategy with intended outcomes and a plan for action that meets the unique challenges of the mine site. Additionally, team members cover how Cat Customer Value Agreements (CVA) provide a custom services package to enable hassle-free ownership of equipment.
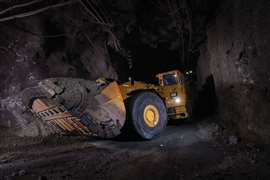
The iron
“Since MINExpo 2021, our teams have made incredible progress with the development of our electric technology and supporting solutions,” said Brian Weller, vice president of electrification, Caterpillar Resource Industries. “We have been working side-by-side with select customers to accelerate the deployment of Caterpillar’s first battery-electric haul trucks. These machines will soon be operating at our customers’ sites where they will be tested and validated across a variety of applications.”
Caterpillar’s underground Cat R1700 XE load-haul-dump (LHD) loader uses battery-electric propulsion that produces zero exhaust emissions and generates less heat than an engine-powered model. The Cat R2900 XE LHD provides a switch reluctance electric drive system that Cat said meets the mining industry’s needs for bigger payloads, faster loading and lower emissions. The 12.2-m-long (40-ft-long) PGS 1260 HD Energy Storage System (ESS) module offers energy storage for charging battery electric machines, and the MEC500 provides mobile equipment charging for the underground mining industry.
Beyond zero-exhaust emissions and fast charging, the battery electric R1700 XE LHD has a 15-tonne (33,069-lb) payload, 18 kph (11.2 mph) fully loaded top speed and up to 2.5 hours of aggressive run time between charges. Five bucket size options offer capacities ranging from 5.7 to 7.5 m3 (7.5 to 9.8 yd3).
The 372-tonne (410-ton) Cat 798 AC mining truck is configured for autonomous haulage with Cat MineStar Command for hauling. The 798 AC features a refreshed cab for operating at high altitudes plus a three-piece window design to improve visibility. Truck messaging will convey the number of ways mines can lower GHG emissions today through alternative fuel options and electric drive systems. Additionally, video stories will show how customer rebuild efforts are driving sustainability at mines, while scale truck bodies will cover the range of options Cat trucks offer for maximizing payload and hauling program efficiency.
“We believe systems, such as Command for hauling, are essential to optimize mine site performance, both with our current product line and as we introduce new offerings like our battery electric solutions,” said Marc Cameron, senior vice president, Caterpillar Resource Industries. “Autonomous technology will help monitor and orchestrate the complex balance of onboard energy, available charging assets and production targets to achieve the lowest operating costs.”
The latest next generation loader, the Cat 995, will anchor the “loading better” display during MINExpo, equipped with a 27.5 m3 (36 yd3) and Cat Advansys 230 GET system to move more material with less downtime. Built to the same size as the 994K, the 995 features a higher rated payload and reportedly demonstrates 21% higher efficiency and 24% more production than the 994K in equal operating mode.
The Cat 24 motor grader will represent the range of haul road maintenance machines that includes the 14, 16 and 18 models. The C24’s High-Performance Circle (HPC) provides a 16,000-hour service life and eliminates frequent inspection, wear strip replacement and circle shoe adjustments. It will be displayed with Caterpillar’s 8.5-m (28-ft) moldboard option – 16% longer than the standard blade – to enhance safety at larger mines by reducing the amount of time spent in the middle lane to clear the windrow.
The largest of the Cat drill rig offering, the exhibited MD6310 rotary drill shares a common platform, parts, components and technologies across the product line. Developed for high-production drilling on 12- and 15-m (39.4- and 49.2-ft) bench heights, it is capable of drilling up to 311-mm (12.25-in) hole diameters and offers up to 30˚ angle hole drilling for cast blasting.
With building-block technologies through semi-autonomous operation, the company said the MD6310 was one key contributing factor to global mining services provider, Thiess, surpassing 1 million meters autonomously drilled milestone using Cat drills.
Caterpillar’s stand at MINExpo 2024 is in Central Hall No. 6333, at the Las Vegas Convention Center from September 24-26.
MAGAZINE
NEWSLETTER
CONNECT WITH THE TEAM
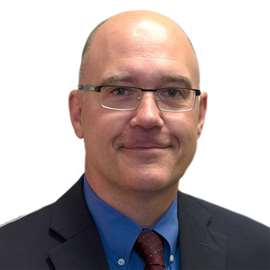
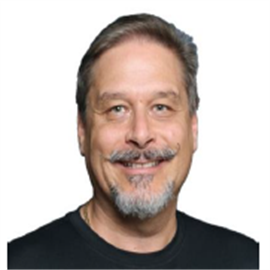
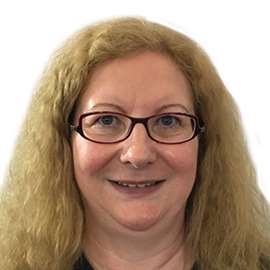