If The Foundations Be Shaken
March 28, 2017
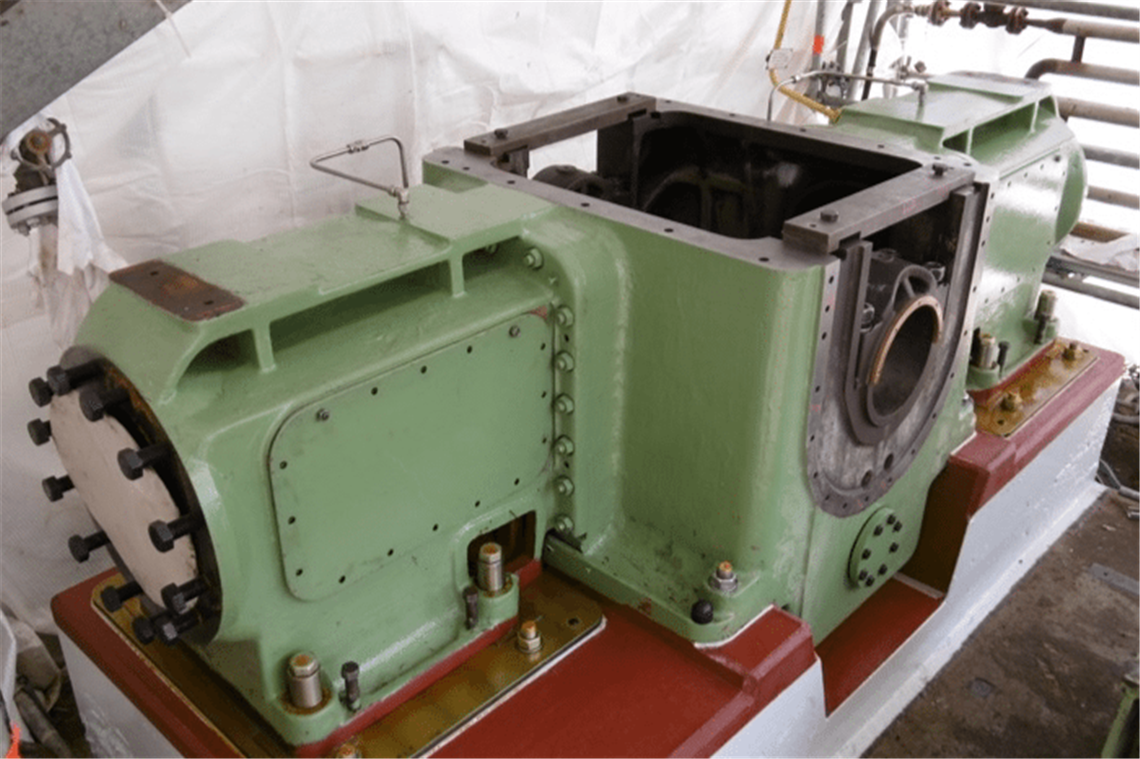
This article was originally published in the December, 2016 issue of COMPRESSORtech2. Subscribe for free to receive every issue in your mailbox or your inbox.
In the mid 1900s, reciprocating compressor foundations were expected to last 20 to 30 years. However, many of the machines installed in the 1960s or 70s are still running on their original foundations, which are in need of repair or replacement because of poor design, construction or maintenance [1].
Particular problems may signal that there is something wrong with the compressor foundation. These problems could be a broken anchor bolt, twisting movements of the machine frame or excessive vibrations.
Often, the machine has to be stopped in order to make these repairs — or else it might stop itself. In many cases, unplanned shutdown could be avoided by looking at maintenance records, the original construction and the as-built situation. There are signs to indicate the foundation is in bad condition. The many updated publications of API, ASTM, GMRC, ISO, DIN, CUR, EOTA, and other regulations and advice are helpful as well.
Moreover, the modern machinery’s performance (horsepower and flow capacity), accuracy of alignment, and environmental requirements with respect to sound and vibrations (due to stricter governmental regulations) have been increased radically over the past decades. This has made the need for increased attention to the foundation, anchorage and upkeep an important issue.
Without repeating all the facts and figures and describing all possible scenarios, this paper is intended to give some guidance on how to inspect a compressor foundation and what possibilities there are for repair. It will also cover some practical issues faced over the past 15 years.
Desk Research
To get a good understanding of the situation, first, desk research is required in order to gather all necessary information.
As-built construction
Especially when observing older configurations, an inspection of the foundation plan and the as-built construction drawings is required in order to check if the foundation and anchoring are designed and perform according to the relevant guidelines such as API recommended practices 686, GMRC Guidelines and PIP REIE 686. Also, check if there has been an update of the compressor or driver where the foundation has not been updated accordingly.
The As-Built Construction Should Be Reviewed On:
Concrete mat and block design
Information on the required dimensions and minimum weight of the concrete block can be found in the aforementioned guidelines. A rough check can be made first, and if it is found that guidelines were not followed, then a more detailed analysis may be required.
Rebar details
In general, there should be a minimum bar size of .75 in. (19.05 mm) (GMRC Guidelines for high-speed reciprocating compressor packages) [2]. There are also rules and practices that can be found in GMRC and API RP 686 to check rebar spacing and material. Again, a simple check could be enough to determine if further action is required and/or if the original design was made according to the applicable standards. Please note that other guidelines may provide different values and therefore one should determine which guideline is to be followed.
It is important to understand whether possible cracks could be related to insufficient rebar. For example, over fifteen years ago rebar spacing at the top of the foundation was advised as being approximately 12 in. (300 mm), while nowadays 6 in. (150 mm) is advised.
Concrete Properties
The concrete should have a minimum compressive strength of 4060 psi (28 MPa) (GMRC, API RP 686), although the design value in many cases does not reflect reality since concrete can be weakened by oil or just because the actual poured concrete was not at optimum quality. If the properties are in doubt, it is advised to have this checked in a laboratory.
Soil and pile setup
A foundation should never be installed without thorough analysis and characterization of the underlying soil. First of all, find out if a study has been done before designing the foundation. Also, look for any changes in the soil properties, for example, due to rising water levels.
For this, the advice of a geotechnical consultant is required in order to determine important elements like mass density, layer variation and stiffness of the soil. Based on this data and on the type and mass of the compressor system, a determination can be made as to whether pilings need to be used and the proper type of foundation for the job.
A tool that could be helpful in checking whether the design of a compressor foundation might be susceptible is the Compressor Foundation Analysis Tool (COFANTO). This program is available to R&D members of the European Forum for Reciprocating Compressors (EFRC).
Anchor type and dimensions
It is of major importance to gather all information on the anchor bolts. Some installations incorporate outdated anchor bolt designs that can eventually lead to problems. At the very least, the following information is to be obtained on the anchorage:
- Bolt preload and designed clamping force.
- Bolt material, size, and type.
- Designed stretch length/elongation.
- Coating/surface treatment.
- Pre-installed versus post-installed.
- Pocket size and type information.
- Edge distance of the anchor pockets.
- Type of grout used for bonding.
Most standards and guidelines, such as the API RP 686, provide helpful guidance on the subjects mentioned above. The information gathered during research on the as-built construction must be combined with maintenance records and a field investigation to form a judgment on the foundation’s state.
Maintenance records
The compressor’s maintenance records are to be analyzed to see if there are any signs of:
- Inability to hold alignment or anchor bolt tension
- Loose or broken anchor bolts
- Increasing vibration levels (above zone B/C of theEFRC guidelines) [3]
- Crank case, crosshead, or support block damage and wear
- Excessive bearing wear
- Piping damage (excessive repairs needed for the attached piping)
These points could indicate foundation problems. All gathered information on trending vibration measurements, repair records, oil analyses and more will also be of great help in foundation troubleshooting.
Field Investigation
After all the data has been collected from the desk research, it is time to examine the compressor foundation on-site. First, the foundation and compressor are examined while running. More comprehensive investigations can be done while the machine is stopped; however, in general, this is only done when it has already been determined that there is something wrong with the foundation or anchorage.
Visual inspection (running compressor)
A lot of information can be gathered during a systematic visual inspection. Most common issues are quite easy to spot. One should look for the following issues:
Loose or broken foundation bolts
Loose or cracked foundation bolts are easy to spot. Very frequently, the compressor trips on a broken anchor bolt, and often, machine operators realize there is something wrong with the foundation if one of the anchor bolts fails. While this is indeed a strong indication, it is also possible that the cause of a bolt failure is to be found somewhere else. For example, sometimes it is easy to over-torque bolts with hydraulic tools.
Compressor looseness
Compressor looseness is easily spotted by air bubbles showing between frame-feet and grout in oil or water (Figure 1). These air bubbles indicate looseness, meaning that the anchoring system is not performing as it should. Oil also considerably reduces the required friction between the frame parts and the grout layer.

Usage of shim plates
Excessive usage of shim plates often indicates that there is a need to “fill-up” space. This can be an indication that there is something ‘moving’ or a mistake has been made during the design phase. The maximum number and thickness of shim plates differ depending on the guideline, region, and the local engineering standards. Different guidelines agree on not using more than three shims in a pack, as more shims lead to spongy (soft) pads.
Unfortunately, the use of adjustable jacks, steel shim blocks or wedges is still frequently advised for alignment of pumps, skids, base frames or even compressors while they remain in place. These steel jacks make the equipment stand on “high heels,” forming a direct steel contact between machine frame and concrete foundation. Instead of having the necessary constant compression on the grout layer, the machinery stands on noncompressive steel blocks, which allows oil and water to penetrate between the steel and grout.
Even worse, neither the anchors nor the grout can function according to their design, as pre-tension is lost on the steel jacks and grout is merely an aesthetic cover.
Another problem with steel shim blocks in the grout is that they tend to corrode. This is a very common condition and causes serious problems such as cracked grout and a machine that is tilted out of alignment.
Edge lifting and delamination of the grout
Edge lifting is caused by the difference in the rate of thermal contraction between epoxy grout and concrete. Generally, the main reason for edge lifting is poor or inexperienced application and the usage of bad quality concrete.
Delamination often occurs between cementitious grout and concrete; mostly caused by the bad adhesive properties of the grout or due to poor preparation of the concrete block.
Edge lifting and delamination do not always form an immediate threat to the foundation of the machine since the part under the machine (if well grouted) is under constant pressure and therefore in better condition. However, oil and water can intrude into the foundation, causing more problems. It can also be a sign of poor application and therefore a reason to suspect more problems.
Cracks in grout layer
Cracks in the grout layer may have different causes such as sharp corners, fast curing or thermal expansion. In many cases, these cracks do not form an immediate threat. However, it is important to look for their root cause and to seal it to prevent further damage.
Deterioration of the grout layer
Penetration of (crude) oil and other fluids into cementitious grout will over time weaken its compressive strength and the adhesive capacity of cementitious grout in the anchor pockets [4]. This will continue up to a point where the grout will crumble between your fingers.
Oil penetrating along the anchors will eventually jeopardize the fixation of the machinery.
Cracks and cold joints in the concrete foundation
Cracks in the concrete foundation can be due to various factors such as weather conditions, and thermal or aggregate expansion. They can be found at re-entrant angles such as the corners where the foundation of the crosshead support is connected to the main block, but also in the sump area, and, of course, cracks running from the anchors towards the outside of the foundation.
When observing cracks in the concrete foundation, one has to realize that vertical cracks are less “dramatic” than horizontal cracks. Horizontal cracks can cause alignment disorders while vertical cracks do not.

The compressor and its foundation must form a tightly integrated structure. Vibration energy travels in the form of waves down and out through the foundation where the soil can absorb it. Breaks, cracks or separations in the integrated compressor/ foundation structure will prevent the vibrational waves from traveling downward [5].
Horizontal cracks create “separated” parts in the foundation and there- fore it will become unable to transfer vibrations into the soil. The monolithic structure (Figure 2) is disconnected.
The same problems can be caused by construction joints, also called “cold joints.” Because concrete does not bond very well to itself, separation can occur if different parts of the foundation are not poured continuously.
Concrete carbonation and spalling
If carbon dioxide from the air reacts with calcium hydroxide in concrete, it forms calcium carbonate. This process is called carbonation. This is a slow and continuous process progressing from the outer surface inward and has two effects: it decreases mechanical strength of concrete and it decreases alkalinity, which is essential for corrosion prevention of the reinforcement steel.

Carbonation and rebar located too close to the concrete surface can cause rebar corrosion. The expansion of the iron oxides induces mechanical stress that can cause the formation of cracks, disrupt the concrete structure, or make outer parts of the foundation fall off (spalling, Figure 3) [6,7]. These phenomena are easy to recognize during visual inspection of the foundation.
Displacement of foundation
Instability of the soil can cause sink- ing or tilting of the foundation (Figure 4). Therefore, displacement of the foundation can indicate that the soil is not adequately supporting the foundation. This can be checked with tools such as a digital water level and tapeline, or more precisely by laser scanning. Trending measurements (measurements over time) can provide more suitable information.

More comprehensive investigations (Running compressor)
The aforementioned visual inspection can be done relatively simply within a few hours. Depending on the information gathered from the desk research and the visual inspection, it may be wise to perform additional investigations.
Vibration measurements
Vibration measurements and analysis of the machine system (which includes anchoring and foundation), will provide hard data to compare with the ISO 10816-8 classification table and the EFRC guidelines for vibrations in reciprocating compressor systems [8,9].
Additionally, an ODS (operating deflection shape) animation can offer a clear visualization of the movements of the complete installation. This can help you to recognize things as looseness or unwanted movements.
More comprehensive investigations (Stopped compressor)
More comprehensive investigations can be done if the machine is stopped. In case of a foundation repair or regrout, these investigations can be useful for deciding if anchor bolts need to be replaced or to find out how much of the concrete has to be chipped away.
Core drilling and investigations
Diamond-drilling of core samples is required in order to check the depth of oil penetration into the block. These cores may also be used for a more extensive carbonation investigation [6] and to check the quality of the concrete. Differences in homogeneity of the concrete can be identified and a compressive stress test can be performed. Oil penetration and changes in concrete quality can also be noticed when new anchor pockets are drilled or old anchor bolts are removed (Figure 5).

Alignment checks
The alignment of the compressor to the driver and the alignment of the extensions to the frame need to be checked since foundation issues will ultimately lead to alignment issues. Also, the alignment of the rotor to the magnetic center needs to be checked to determine web deflection and rod runout. Depending on the need for further investigation, more values can be measured such as the flatness of soleplates and the linebore (center line measurement).
Inspection of the anchor bolts
Anchor bolt stretch may be measured with an ultrasonic bolt meter, provided the anchor model and data are known. Are there signs of bolt over-stretching? If the grout layer has blocked the anchor to stretch, it will typically stretch just below the nut.
If the compressor is removed, it is also possible to investigate bonding of the anchor into the concrete foundation by using a hollow plunger cylinder and a dial indicator. This can be done by placing the cylinder over the bolt and applying load with a hydraulic cylinder while the dial indicator is attached to the head of the anchor bolt. If the bolt comes up more than the stretch length after applying the design load (be careful not to apply too much load) for 24 hours, then one can be sure that the anchor is debonding from its pocket.
Analysis And Correction Plan
After all the data from the desk and field research has been gathered and combined, it is time to write an analysis and correction plan. The analysis plan is an evaluation of foundation and anchoring and should also contain an indication of the urgency.
For example, a loose anchor bolt, in combination with vibration levels above EFRC reference values, requires high urgency since the machine’s anchoring cannot be guaranteed. The machine should be stopped in order to perform at least an emergency repair. Cracks in a grouting layer in combination with normal vibration levels, in general, require no special urgency. A repair can be planned during the next overhaul or when convenient.
It is hard to provide a list to indicate which problems require immediate attention and which not, since there is always a combination of problems and every situation is different. Hence, in general, one can say that every problem that is an immediate threat for anchoring, and load transfer of the compressor should be a reason for instant repair.
Repair methods
After the urgency of a repair is determined, the repair method is to be selected. If an urgent repair is compulsory, it is also possible to perform a crisis repair on short notice while planning a more durable repair during a maintenance stop.
There are more factors that influence the selection of a suitable repair method. The most important (but surely not the only) factors are:
- Urgency of the repair.
- Safety conditions.
- Timeframe for the repair.
- Possibility of removing the machine or not.
- Time of the year (weather conditions).
Table 1 shows a brief summary of some common problems, their typical urgency, and possible repair methods. Please, note that this list is not a complete reference with required urgency indications and repair methods.

The correction plan should include a proposal for repair, specifying alignment, usage of soleplates, anchoring method, grouting, injecting, and other activities with a time schedule. It is also important to conduct a safety and risk analysis and to provide a budget price for the repair.
Practical Issues During Repair
When repairing a compressor foundation (regularly incorporating a regrout of the machine), some issues require special attention. New techniques, materials, and insights may require a change of mind for many companies. To avoid unexpected changes in planning and budget, these subjects should be discussed at an early stage.

3-D positioning
Before an installation is removed, the exact position of the complete line should be registered. A 3-D tracking laser is used to measure the exact position of the frame, anchors, cylinders, crosshead supports, centerline of the crankshaft, expansion vessels, and all flanges of the main piping (Figure 7). This 3-D position measurement provides a complete set of data on the position of the installation.
For example, the measurement can tell whether the total installation (compressor-driver) is within tolerances in the water-level plane. This information may indicate possible tilting of the total foundation. Corrections at the time of reinstallation need to be addressed as early as possible. The consequences are to be considered case by case.

If the old anchor bolts are to be removed, the 3-D measurement data is used to install the machine on the exact same (or improved) coordinates. In urgent cases, it is even possible to install the anchor bolts in place before the compressor is back on-site.
Soleplates
Not all reciprocating compressors are installed with soleplates (Figure 8). Some compressor configurations require a little free horizontal movement of the crosshead due to thermal expansion. If this is the case, it will be indicated by the compressor manufacturer. Soleplates (in these configurations called sliding plates) or bending plates allow these movements, while grouts will crack.
Another big advantage of installing soleplates is the ease of removal of the crosshead support without having the grout jacked away. Especially, since nowadays high-performance epoxy grouts are advised, it will save a lot of time and money if one does not have to jack away and replace the grouting. Furthermore, precision alignments are easier to perform at any later time.

When designing soleplates, it is important to avoid sharp corners (otherwise, the grout will crack) and include a good jacking solution (leveling bolts). Also, the design should be stiff and there must be a possibility to apply a corrosion-resistant coating to the soleplate on-site, depending on location and local coating specifications. In many cases, it is not possible to apply a coating beforehand because the epoxy grout needs to bond with the steel and not with the coating. Therefore, during the design phase, a plan should be made as to how such a coating can be applied on-site.
In some cases, adapting a special anchoring system with coupling is also required so it becomes possible to loosen the extension and slide it away. This is required for many reciprocating compressor models, otherwise, removing the extension will not be possible.
Method of alignment
Unfortunately, the use of adjustable jacks, steel shim blocks or wedges is still frequently advised for alignment of pumps, skids, base frames, or even compressors.
These steel jacks make the equipment stand on “high heels,” forming a direct steel contact between machine frame and concrete foundation. Instead of having the necessary constant compression on the grout, the machinery stands on noncompressive steel blocks, which allows oil and water to penetrate. Neither the anchors nor the grout can function according to their design as pre-tension is lost on the steel jacks and grout is merely an aesthetic cover. Furthermore, these parts are subjected to corrosion, which jeopardizes the alignment. Leaving adjustable alignment tools in place is strongly discouraged. (API RP 686) [9].
The only correct solution is to use jack bolts. They are easy to apply in soleplates, skids or frames. The bolts are removed after full cure of the grout, followed by proper torquing of the anchors. Jack bolts should be engineered to carry the full weight of the machine skid under all conditions expected during skid leveling.

On the concrete foundation, a round metal landing pad should be placed to carry the jacking screw. The design of the pad is stainless steel with rounded edges and can be found it the API RP 686 (Figure 9).
Anchoring
Anchor pockets are to be drilled according to the calculated anchor data. Besides the fact that the adhesive surface of the pocket is determinative, the diameter to be drilled should be chosen based on the existing situation of the old anchor. One must consider: Is it only the anchor that is to be removed, or is there also a metal sleeve or a hammerhead construction that must be removed?
The best practice for anchor bolt installation requires having the anchors hanging free, and centered, from the machine feet into the pockets before grouting them (Figure 10). This method guarantees correct height and position, without touching the concrete. An equal space between anchor and machine foothole is obtained, which makes the necessary alignment possible.
A group of anchors, such as those installed in the frame, should perform as equally as possible. Having one or two anchors apply excessively more or less load than the others should be avoided; a deviation of less than 10% is best practice. For this reason, avoid replacing one or two anchors only and leaving the others in place.
Grouting
According to API RP 686 and other recommendations, epoxy grouts are always best for reciprocating compressor systems.
Epoxy grout has many advantages over cement grout; however, there are also some issues. If the application is done by a certified and experienced company, these difficulties will have no negative influence. Inexperienced applicators will face some unexpected situations that will lead to problems. Some examples of essential concerns are:
• Creep calculation.
• Temperature limitations.
• Mixing techniques.
• Usage of expansion joints.
• Edge lifting.
• Temperature during application.
There are many different epoxy grouts available. Compare the quality, ease of application and technical properties. The best option is to choose a proven product such as Chockfast Red epoxy grout and a reliable applicator such as EMHA.

Injection of cracks
As explained earlier, there is a big difference in cracks in grouting and cracks in cold joints in the concrete foundation.
Cracks In The Cement Grout Layer
In the past, attempts were made to inject cracks in grouting with low viscosity epoxy, but the results were generally very disappointing due to the poor quality of the cementitious grout. Replacing the grout layer with epoxy grout is the best option.
Cracks In The Foundation
Vertical cracks running in corners and along the sump are easily injected with low viscosity epoxy (Figure 11). Low pressure pumping at a slow rate will push the majority of oil and water out. Special epoxies absorb a considerable amount of oil and water as well. Stone pockets will be filled.

Horizontal cracks or cold joints reduce the possibility of transmitting vibrations into the mat. Due to the ongoing vibrations, a clearance at this plane is created in the foundation. This creates two ‘separated’ parts in the foundation. Injection of these cracks with an epoxy will not be satisfactory since these horizontal disconnections require additional compressive strength in order to bring the separated parts together again. Therefore, long anchors (pull anchors, Figure 6) are to be installed across the cold joint, making the foundation monolithic again.
Epilogue
This paper should provide some guidance in a situation where problems with the foundation or anchoring of a reciprocating compressor system are suspected. For ease of understanding, more extensive data and details are avoided, but these can be found in the applicable guidelines.
Several international standards, guidelines and best practices for the design of foundations, anchors and grouting of reciprocating compressor systems have been developed. Unfortunately, most of this material is either not available for everybody, is too general or not directly applicable.
For that reason, an EFRC project was started entitled: “Summary of international guidelines, standards and best practices of foundations, anchors and grouting of reciprocating compressor systems.” This document is intended for use by rotating equipment and civil engineers of end users, packagers, EPC contractors, grouting companies and reciprocating compressor OEMs. The document can be downloaded from the EFRC website (www.recip.org) at the end of 2016, by its members only [10].
About the authors: Theo de Kok (BBA) is the unit manager, Industrial Services at EMHA. Contact him at: [email protected] Tom Hoekstra is a senior technical manager, Industrial Services at EMHA. Contact him at: [email protected].
References:
1. EFRC project: “Summary of international guidelines, standards and best practices of foundations, anchors and grouting of reciprocating compressor systems” (www.recip.org)
2. EFRC paper: “Best Practices in Compressor Mounting” James A. Kuly, October 2010, Florence, Italy ITW/ Polymer Technologies, USA, at the occasion of the 7th EFRC Conference,
3. “Recommended Practice for Machinery Installation and Installation Design” API Recommended Practice 686 second edition, December 2009 Ref 5.4.2
4. GMRC Technical Report: “Foundation Guidelines” A. J. Smalley P. J. Pantermuehl, January 1997, Mechanical and Fluids Engineering Division South-west Research Institute Report No. TR-97-2
5. GMRC Guideline For High-Speed Reciprocating Compressor Packages For Natural Gas Transmis-sion & Storage Applications, October 7, 2013, Gas Machinery Research Council ACI Services Inc.
6. “Experimental and numerical investigation of dynamic rocking foundation behavior” Phipps, Jacob Nathan 2013. Graduate Theses and Dissertations. Paper 13615
7. EFRC project: “Guidelines for Vibrations in Reciprocating Compressor systems” European Forum Reciprocating Compressors (EFRC), November 2009
8. “Sulfate attack in concrete and mortar” An abstract from the book ‘Understanding Cement’ ISBN-13: 978-0-9571045-2-5
9. “Polymers in Concrete”, 1994, Satish Chandra, Yoshihiko Ohama ISBN-13: 978-0849348150
10. “Effect of Crude Oil Spill on Compressive Strength of Concrete Materials” Ejeh, S.P. and Uche. Journal of Applied Sciences Research: 1756-1761.2009
11. “Mechanical vibration – Evaluation of machine vibration by measurements on non-rotating parts” Part 8: Reciprocating compressor systems, BS ISO 10816-8:2014
12. EFRC paper “Reciprocating Compressor Foundations They do not last forever” R. van Lienen, H. Lankenau, 5th EFRC Conference March 2007, Prague. NEAC compressor service GmbH
13. “Mechanical vibration – Evaluation of machine vibration by measurements on non-rotating parts” Part 8: Reciprocating compressor systems ISO 10816-8:2014
MAGAZINE
NEWSLETTER
CONNECT WITH THE TEAM
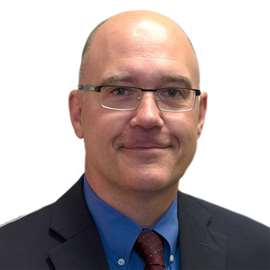
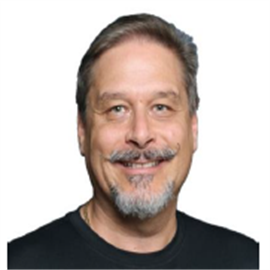
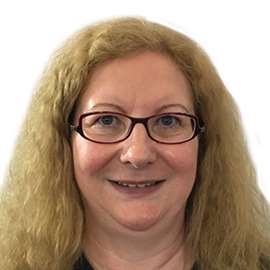