Commissioning a VFD (Variable Frequency Drive)
October 19, 2020
Experts examine the procedure of commissioning, running it up and checking it out, medium-voltage VFDs rated 250 hp (186.4 kW) and larger at a minimum 2.3 kV voltage level.
Equipment commissioning is a significant milestone in the life of any heavy industrial project. This activity brings the end user one step closer to project completion and achieving return on investment. Yet this step is often misunderstood, which can result in unmet expectations.
Successful project commissioning is a balance of several moving parts that must be completed in the right sequence at the right time.
Medium-voltage VFDs (Variable Frequency Drives) are commonly applied to electric motor-driven rotating machinery such as compressors, pumps, extruders and others. VFDs form a critical link between the electric utility and the motor/driven equipment as shown in Figure 1.
While many in the industry are familiar with starting up mechanical equipment, starting up electrical equipment is not as common. We consider the scope and applicability regarding medium-voltage VFDs rated 250 hp (186.4 kW) and larger at a minimum 2.3 kV voltage level.

Air cooled medium-voltage VFDs usually take several weeks to engineer and manufacture, as well as days to install. Months often pass between the installation and commissioning dates.
What is commissioning?
Equipment commissioning, commonly known as “startup,” is a series of activities performed by the field-service engineer of the equipment manufacturer in concert with the end user, engineering consultant and/or the driven original equipment manufacturer (OEM).
The purpose of commissioning is to safely put the equipment into service to meet process functionality and overall project objectives.
A safe and efficient startup will bring together select personnel from the equipment vendor, equipment purchaser and their representative for the following benefits:
- Confidence that the equipment performs as per expected under the full range of the foreseeable operating envelope;
- Opportunity for the end user’s operator, maintenance and service personnel to gain familiarity with the key components of the equipment, receive training and become familiar with system operation, and;
- From an equipment manufacturer perspective, record, and capture:
- Field markups and changes to generate a set of “as installed” electrical elementary drawings;
- “As installed” parameter settings and configuration data, such as drive files, and;
- “As installed” performance trend data.
When dealing with high levels of complexity, such as starting up a new plant, site or a medium-voltage motor and VFD service, a system is required to facilitate productivity. Checklists are a surprisingly simple solution to breakdown that complexity. A series of checklist items for a safe, reliable and efficient medium-voltage VFD startup are shown below.
Pre-commissioning timeline and checklist (administrative)
Approximate weeks from medium-voltage VFD commissioning start date |
Activity |
10–12 weeks beforehand |
- Request for commissioning quotation from VFD manufacturer |
Eight to 10 weeks beforehand |
- Request for VFD commissioning plan |
Six weeks beforehand | - Schedule VFD FSE for site arrival - Provide field-service engineer with guidance on safety-related training and need for special entry permit (eg TWIC card, permanent residence card (green card), passport, driver’s license) |
Two weeks beforehand | - Site supervisor’s contact details - Lodging guidance and others |
Pre-commissioning checklist (site)
While the foregoing checklist is mostly administrative, the series of activities below detail steps that must be undertaken at the site by the end user or the contractor before the VFD field-service engineer arrives onsite:
- Medium-voltage VFD is physically installed in the building;
- Secure VFD frame as per manufacturer guidance;
- Interconnect power and control cabling between VFD shipping splits (if applicable);
- Mount and complete electrical connections of the blower fans;
- Clean surroundings and panel interior to ensure it is free from dirt and debris;
- Verify all wire and cable entry points are sealed against weather, humidity, and rodents:
- High voltage cabling terminated between the VFD output and the motor observing the phase connections as per the VFD elementary drawings, and;
- Megger cables between the VFD and motor; - HVAC system commissioned and ready to provide necessary cooling or heating;
- Run the HVAC system for at least 24 hours prior to VFD energization. This ensures the VFD installation environment is free of condensing humidity;
- Motor might need to be detached from the driven equipment for initial testing depending on the VFD manufacturer;
- All voltage levels, such as medium voltage (eg 4.16 kV), low voltage (eg 480 V) should be available and locked out/tagged out. If redundant power supply (primarily 120 V) is made available, the associated UPS system must be checkout;
- Control wiring between the VFD and customer DCS/SCADA or PLC system completed and ready to supply commands, references and permissives;
- Incoming switchgear and feeder protection must be checked out and commissioned;
- Verify E-stop loop is wired and ready to be checked out;
- Speed reference signal is available from the control system;
- The following personnel are scheduled to arrive or be present when the VFD field-service engineer arrives:
Driven equipment OEM (such as pump, compressor, fan, extruder, etc.);
- Process control representative, and;
- Craft labor; - Verify any drawings, manuals, kirk keys and other items that were shipped with the VFD are available and not misplaced;
- Motor lubrication system is fully checked and commissioned;
- For water-cooled VFD, depending on type and method, cooling system external to the VFD must be commissioned and ready, and;
- Motor commissioning report available for review.
Common issues that lead to medium-voltage VFD commissioning delay and expense
It is not uncommon for the VFD field-service engineer to arrive onsite only to discover that the site is not prepared for startup. Below are some items that commonly delay equipment startup:
- Control systems beyond the VFD scope not complete and still in the process of being wired/terminated, and in some cases, software being developed onsite;
- VFD blower fans not mounted;
- Incoming power not available;
- Process not ready for full operating range;
- VFD energized in absence of field-service engineer leading to damaged components;
- Motor not commissioned, mounted or aligned;
- Incoming switchgear, if outside the scope of the VFD, is not commissioned, and;
- Absence of the manufacturer’s field engineer. It is always best practice to overlap the presence of the VFD, motor and driven equipment service engineers.
It should be noted that unless otherwise supplied by the VFD manufacturer, troubleshooting the driven equipment, electric motor, sync-transfer switchgear and external control systems is not included in VFD commissioning.
Conclusions and end user perspective
Starting up a medium-voltage VFD is often critical to the operational process for the end user, which means it is typically on the critical path for the project to begin creating product and generating revenue.
The process applications that are driven by the mechanical rotating equipment are also complex processes, which require expertise from field engineers for each piece of corresponding equipment. The complexity of starting the process requires an extensive coordinated effort.
Figure 2 provides an overview of key personnel that typically participate in a VFD commissioning. Each should be clearly aware of their roles and responsibilities.
The integrated effort for control communication between the end user’s site communications and each piece of equipment is important for sequencing of activities, and can prove to be a challenging part of the startup. Pre-commissioning integration meetings via phone/digital media are a cost-effective method for starting the process of facilitating communication between suppliers and ensuring the integrity of the equipment.
All foreseeable process scenarios should also be documented by the engineering consultant/end user and communicated to all parties involved. For example, when a drive starts multiple motors and runs on the drive, as well as synchronous transfers to utility, it is essential to communicate and test the scenarios for starting each motor based on process requirements. Questions to ask include ‘Does one motor always start first?’, ‘What signals are sent to the drive to start the second motor?’ and ‘What happens to the first motor?’
The drive and site communications can meet process requirements. Yet this can often lead to additional time and cost for the field service team onsite if the required process scenarios are not identified and notified ahead of time.
Understanding and communicating the startup requirements for the mechanical and rotating equipment is also important for the VFD field engineer to ensure the quoted costs are accurately captured. Any additional time should be budgeted and accounted for, so that there are no surprises in the field.
There are a variety of factors that need to be identified and communicated between the field service engineers, engineering consultant and the end user for the startup to run effectively and efficiently. The better the process scenario is mapped out and communicated, the more successful the startup process.

Sales manager, Control Technology Company
Waller began his career with Boeing Commercial Airplanes where he learned the structured process of engineering design, development and manufacturing.
At Control Technology he supports engineering consultants and end users in applying integrated electrical solutions, including substation transformers, industrial control buildings with medium and low voltage switchgear, motor control centers, UPS, PLC, and variable frequency drives.

Business development specialist, TMEIC’s Energy and Infrastructure Systems Group
Verma provides technical guidance and consultation for new products from idea generation through product launch. He focuses on application, sales enablement and business development of engineered Medium Voltage power conversion equipment.
He has presented several tutorials and seminars at conferences. Verma is the author of more than a dozen technical papers published internationally. He is also a senior member of IEEE and serves on an IEEE PCIC sub-committee to provide input on IEEE 1566 VFD standard.

Manager-technology, TMEIC India Private Limited
Varanasi provides specialized Variable Frequency Drives and Control expertise to clients and field engineers, advising clients and company engineers in resolving technical issues.
He has participated in the development, application engineering and project management of MV Motors and VFDs.
Varanasi is the author of scholarly papers published in internationally recognized conferences such as IEEE.
MAGAZINE
NEWSLETTER
CONNECT WITH THE TEAM
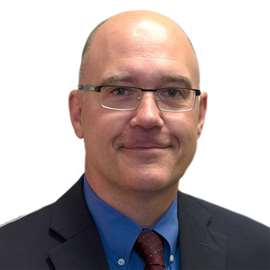
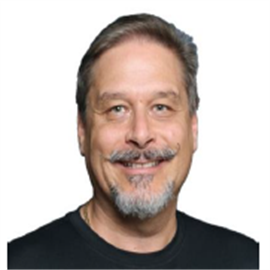
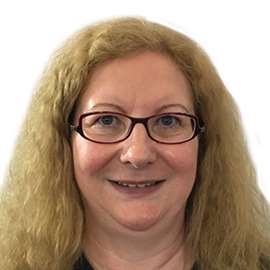