Unlocking efficiency in gas compression
April 30, 2024
Three trends and what they mean

As the global landscape continues to evolve, so do the challenges and opportunities within the various industries that depend on compressors to keep operations running. No matter what industry you are in or what gases your facility is compressing, the need for efficient, reliable, and environmentally conscious compression solutions has never been more critical.
As the Global OEM Industrial Sector Specialist at Chevron Lubricants, and with more than 30 years of technical experience in gas compression, I help people in the field understand lubrication within the context of various applications including problem resolution, filtration, flushing, and turbine engine and compressor lubrication. As a mechanical engineer, I have worked for Chevron for more than 20 years, and previously worked at Caterpillar Engine Division for 13 years.
And with that backdrop, I’m eager to explore three key trends that touch all types of gas compression in varying facilities that are reshaping the industry and the actionable takeaways that you can implement in your day-to-day operations right now.
Trend #1:
Increasing energy efficiency
While pushing for energy efficient operations isn’t a new trend, it is one that deserves attention because there are simple changes you can make to help your operation save energy – a win-win for the environment and your bottom line.
First and foremost, one way to increase energy efficiency is by taking a serious look at the viscosity of the lubrication you are using – let’s start by dispelling myths around high viscosity. A common misconception is that higher viscosity oils provide superior lubrication, and contrary to the long-held belief that higher viscosity lubricants equate to better performance, modern engineering principles are challenging this notion. How? Lower viscosity oils not only reduce energy consumption but also enhance cooling capabilities, thus optimizing equipment efficiency. Let’s dig into this more and look at the “how” and “why.”
Viscosity is essentially a measure of resistance to shear, meaning higher viscosity oils generate more heat and require additional energy for operation. By transitioning to lower viscosity oils, operators can mitigate heat generation, improve cooling efficiency, and ultimately save energy.
Moreover, in rotating equipment like dynamic compressors lower viscosity oils contribute to longer oil life and can eliminate phenomena such as electrostatic discharge, which can compromise oil integrity. It’s essential, however, to strike a balance and avoid excessive viscosity reduction, which could lead to increased wear and potential equipment failure. The key lies in meticulous measurement and analysis to optimize viscosity selection for each application, a practice akin to the precision tuning of a musical instrument.
To achieve greater energy efficiency in gas compression, operators can take several steps:
1. Selecting optimal viscosity: Conduct thorough analysis and measurement to determine the optimal viscosity at the operating temperature for each application. Determining the middle ground between viscosity reduction and proper equipment lubrication is crucial to prevent excessive wear and potential equipment failure.
2. Regular maintenance: Implement a proactive maintenance schedule to ensure equipment is operating at peak efficiency. This includes monitoring oil quality, conducting regular inspections, and addressing any issues promptly to prevent energy waste due to equipment operation inefficiencies.
3. Investing in advanced technology: Embrace technological advancements--such as online oil analysis systems like direct imaging particle count and contamination control equipment like relative humidity monitors for the oil--to monitor oil health and equipment performance in real-time, and identify areas for improvement. This allows for proactive maintenance and optimization of energy efficiency.
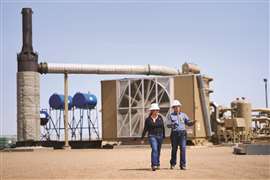
4. Employee training and education:
Provide comprehensive training to operators and maintenance personnel on the importance of energy efficiency and proper lubrication practices. Encourage a culture of continuous improvement and knowledge sharing to drive sustainable energy-saving initiatives.
Overall, increasing energy efficiency not only reduces operational costs but also contributes to environmental sustainability by minimizing energy consumption and reducing carbon emissions, such as with longer oil drain intervals driving less oil disposal. By adopting lower viscosity and higher performance oils and implementing proactive maintenance strategies, operators can optimize equipment performance while lowering their environmental footprint.
Trend #2:
Mitigating methane slip through proper lubrication
With sustainability taking center stage, the industry is grappling with the challenge of methane slip, a significant concern in both natural gas compression and processing operations. Proper lubrication plays an important role in mitigating methane slip by ensuring optimal sealing and preventing accelerated wear of critical components.
By selecting appropriate reciprocating compressor oils and maintaining proper lubrication practices, operators can minimize methane emissions and be sure they are adhering to regulatory compliance. This underscores the need for industries to improve their commitment to environmental stewardship and highlights the urgency of addressing methane slip through proactive measures. Here are four reasons we need to pay more attention to methane slip:
1. Environmental impact: Methane is a potent greenhouse gas, contributing significantly to global warming and climate change when leaked into the atmosphere. As sustainability becomes a top priority, reducing methane emissions is essential to mitigate environmental risks and adhere to emission reduction targets.
2. Regulatory compliance: Governments and regulatory bodies are increasingly implementing stringent regulations to control methane emissions. Proper lubrication practices directly influence methane leakage rates, making it imperative for operators to comply with regulatory standards to avoid penalties and maintain operational licenses.
3. Equipment performance and longevity: Beyond the environmental implications driving methane slip, poor oil choice can also lead to accelerated wear and tear of critical compressor components. Proper lubrication ensures optimal sealing of rod packing seals and reduces friction, preventing premature equipment failure and costly downtime.
4. Industry reputation: As concerns over climate change continue to escalate, industries are under heightened scrutiny regarding their environmental impact. Demonstrating a commitment to environmental stewardship by actively addressing methane slip through lubrication practices enhances your operation’s reputation and fosters trust among stakeholders.
Addressing methane slip through proactive lubrication measures aligns with industry efforts to adopt sustainable practices and reduce carbon footprints. By selecting appropriate reciprocating compressor oils and adhering to maintenance protocols, operators can minimize methane emissions and contribute to overall environmental sustainability goals.
Trend #3:
Preventing deposits and contamination management
Contamination control is a challenge across various types of compressors, including centrifugal, screw, and reciprocating compressors. Contamination, whether in the form of dirt, water, or chemicals, can significantly impact the performance and longevity of compressor equipment. The lube oil system in turbo compressors, although well-sealed, can still be vulnerable to ingress, making monitoring contamination levels crucial. Preventing contamination requires a multi-faceted approach.
In gas screw compressors, where premature compressor wear is often linked to contamination issues, effective filtration of intake gases is vital. Contaminants in the gas stream can compromise the oil creating wear from hard particles and varnish from chemical contamination and, consequently, the compressor’s performance and lifespan. Preventing deposits and managing contamination in gas compression is crucial for several reasons:
1. Performance optimization: Contamination, whether in the form of dirt, water, or chemicals, can severely impact the performance of compressor equipment. Even small particles can disrupt the operation of compressors, leading to decreased efficiency and potentially costly downtime.
2. Longevity of equipment: Contamination not only affects performance but also accelerates wear rates on compressor components. Over time, this can lead to increased maintenance requirements, higher repair costs, and ultimately shorter equipment time between overhaul. By managing contamination effectively, operators can extend the life of their compressor equipment and reduce overall maintenance expenses.
3. Maintaining oil quality: In turbo compressors, the lube oil system is particularly vulnerable to contamination from poorly maintained reservoir breather filters especially when vapor extractors
are in use. Contaminants such as water
from humidity and particles can degrade
the quality of the oil, reducing water separability, accelerating oil degradation and potentially causing deposits, leading to damage in internal components. This highlights the importance of monitoring contamination levels and taking proactive measures to maintain oil quality.
To better manage contamination in gas compression, operators can take the following steps:
1. Implement real-time monitoring: Advances in technology, such as online oil analysis, allow for real-time monitoring of contamination parameters. By continuously monitoring particle and water contamination levels, operators can quickly identify potential issues and take corrective action before they escalate.
2. Utilize internet-connected machines: Internet-connected (IioT) oil monitors on compressors enable operators to receive immediate alerts about contamination events compared to weeks or months for conventional bottle and lab oil analysis. This facilitates swift intervention and preventive measures, minimizing the impact of contamination on equipment performance and longevity.
3. Install dry air purges and maintain air filters: For turbo compressors, installing dry air purges on storage or mothballed reservoirs and regularly maintaining air filters are essential practices to prevent dust ingress and contamination. These simple yet effective measures can significantly reduce the risk of contamination-related issues.
4. Maintain vapor extractors and inlet gas filtration systems: In screw compressors, proper maintenance of vapor extractors and inlet gas filtration systems is critical to safeguarding against contamination. Regular inspection and cleaning of these components can help ensure the integrity of the gas stream and prevent contaminants from entering the compressor.
Overall, by prioritizing contamination control and implementing proactive maintenance practices, operators can mitigate the risks associated with contamination and optimize the efficiency and reliability of compressor equipment across various applications.
Take action
In conclusion, the evolving landscape of gas compression presents both challenges and opportunities across industries worldwide. Regardless of your industry or the gases your facility compresses, the imperative for efficient, reliable, and environmentally conscious compression solutions has never been greater. As we navigate these trends, it’s clear that prioritizing energy efficiency, mitigating methane slip, and managing contamination are paramount for success. By embracing these trends and implementing proactive measures, operators can optimize equipment performance, minimize environmental impact, and ensure the longevity of their compressor systems.
Author’s note: Paul Sly, Is Global OEM Industrial Sector Specialist at Chevron Lubricants. He has more than 30 years of technical experience in gas compression and has been with Chevron for more than 20 years and previously worked at Caterpillar Engine Division.
MAGAZINE
NEWSLETTER
CONNECT WITH THE TEAM
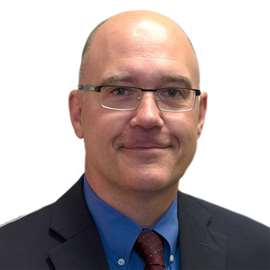
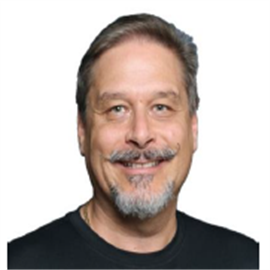
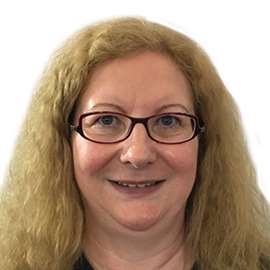