Interview: MEWP components - changes and challenges
21 November 2022
Cobo’s chief business development officer explains how components for MEWPs are developing and how his sector has been struck by supply chain issues.
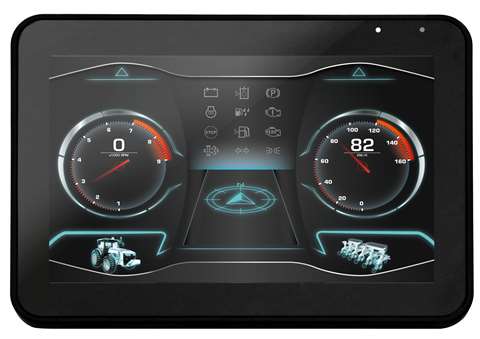
Cobo Group was founded in 1949 in Italy and remains a family-owned company with around 1,500 employees globally and a most recent annual turnover of €280 million – representing a record year.
One of those employees is Stefano Scapin, chief business development officer of Cobo, who is based in Hong Kong.
The company’s mission is to be a leader in the design, development and supply of component solutions for the non-high volume vehicle market.
The core business is heavy and mobile machinery, with most of it found in agriculture and construction, including a good proportion in the access industry, including telehandlers, airport ground support equipment and road sweepers.
Product range
Cobos products include a wide range of mechanical components, including steering and seating column kits, LED lighting, such as headlights, rear lamps and rotating lights, as well as a good range of switches.
Then there are instrument clusters and the electrical range, amounting to seven product lines in all, with the latest being powered electronics, including motor controllers.
“Our real value is in working with small- and medium-sized OEMs, and almost co-designing the electric schematic of the machine and providing a wide range of related components linked to software applications,” explains Scapin. Everything is related to safety.
“We have expertise in all the norms, including EN280 and experience in machine directives.”
Taking on the MEWP segment is no easy task, confirms Scapin, “It is very wide. If you look at the number of machines and applications.
“The AWP is the most critical because it is lifting people. There must be a fundamental focus on safety and that is our aim; to provide control systems related to movement but in the end related to safety.”
The system must be smart and safe enough to recognise when a dangerous incident takes place to stop all movement of the machine before the operator is faced with a life-threatening situation.
“We have been supplying LMIs to lifting applications for 30 years. If we look back then, they were made using sensors which measures the angle, then measures the length and the pressure in the lifting cylinder, and there might be a load sensor on the cage.
“The controller is the brain of the machine, which creates the algorithm the ensure the safety of the machine, and displays that information on a screen.”
Scapin is now seeing an evolution of the process. “We are still based in those fundamentals, but technology and norms have evolved. In Europe, the EN280 and ANSI A92, in the US, have pretty much aligned, and China is becoming global and adopting the same norms.
“So, we have a global alignment of standards which demands greater safety.”
Changes in MEWP regulation and production
Scapin adds, “Go back 20 years and these norms were not that strict - there was still a probability of error, today the EN280 and other norms explicitly require a performance level of components that are part of that safety chain and must meet a specific performance level.”
Besides the regulations, there are the products themselves. “The architecture has changed, everything needs to be redundant.”
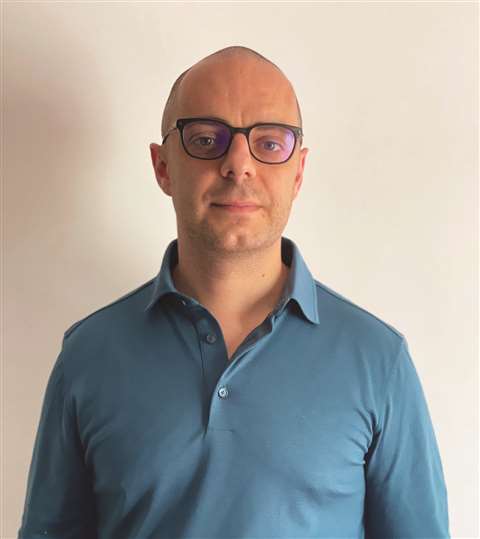
Usually, these days, says Scapin, “The devices need dual microprocessors. We have one sensor in one housing but inside that housing you have dual logic – if for any reason a micro controller in that angle sensor, for example, goes wrong, so you have back up.”
There is also an evolution in design and life cycle of products and their performance. “Now safety control has moved to 32-bit microprocessors and machines have more features and processing power.
“If you look at Human Machine Interface (HMI) equipment; in the past you had black and white displays, whereas today you start to see seven and up to 12 inch displays equipped with excellent user environment graphics and functions that are like the automotive industry.”
Multinational OEMs, explains Scapin, have many divisions and knowhow across the board, making integration of electronics much easier, as it is often produced in-house. “They keep the knowledge and manage the modifications.”
However, there are many other smaller companies that do not have the direct knowledge or expertise, “They need a full turnkey supplier, and in that case we have the capacity to work with them to design the electrical schematics of the machine.”
Scapin adds, “Most importantly, keeping an eye on safety and automation, we can help the manufacturer with the circuit architecture and in some cases work along with notified bodies like TÜV to get the certification process underway.”
Electrification of MEWPs
Based in Hong Kong, Scapin is well positioned to see how China compares in its development to the rest of the world.
For example, there are impressive advances in electrification. “China is surprising - when things happen, they happen at speed and you don’t always see it. Before Covid, the number of electric boom lifts was very limited.
“But for different reasons, Covid accelerated this technology, and now electrification has been deployed extensively in booms lifts, whether it be hybrid or electric equipment.
“From our side, if you think about connectivity and electrification these trends are closely linked. We have short distance communication so you have modules to translate from can bus to Bluetooth or Wi-Fi, then sent the machine information to an operator’s tablet as wireless diagnostics. “
How is alternative power and data changing the MEWP sector?
The company also has its own telematics, that is connected to the control system. Looking back, in the first evolution of collecting data there was a time where data was of little use. “We collected data but we did not know how to store, process and how to use it.
“If you overcome that you can improve your system by storing and processing data properly, around drivability, consumption and how to save energy. You can then also agree with manufacturers to release software updates remotely.”
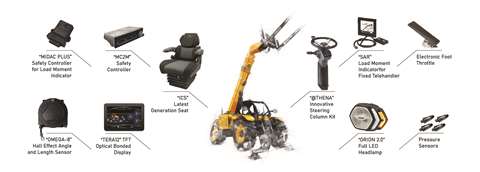
Turning to electrification, Cobo has seen the change in the industry first hand. “If we look at scissor lifts, for example, they are very much electrified. You still have machines that are hydraulic drive, but this has been changing for a number of years.
“The deployment of power electrics into boom lifts is also happening gradually.”
Indeed, says Scapin, Cobo is working with some companies in China that have more electric boom lifts than diesel-powered ones. The transition is happening, although there are still cost prohibitors. “If you compare lithium-ion with lead acid there is still a big gap. If you compare a combustion engine with a full set of electrified axles, plus power electronics, it’s still expensive.
“But this technology is developing very quickly and the cost is projected to go down, as soon as usage is expanded.
“The start up cost versus total cost of ownership is another issue and there must be government initiatives to specify that combustion engines cannot be used in certain places.”
In China, says Scapin, there’s a good synergy between technology and the infrastructure required to power it, which is another reason why deployment is happening quickly.
MAGAZINE
NEWSLETTER
CONNECT WITH THE TEAM
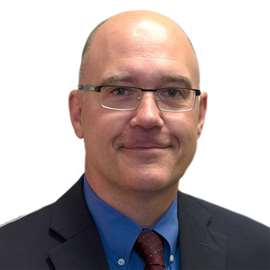
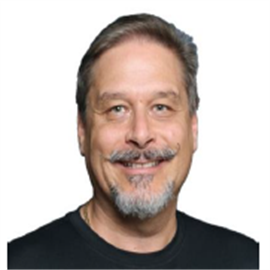
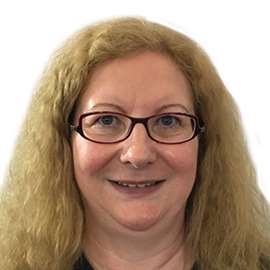