Midstream leaders collaborate to create Ariel compressor training in VR
April 28, 2023
Attendees to the 2023 GCA Expo & Conference were treated to a surprise as they were able to experience an Ariel compressor in virtual reality, compression thanks to Tulsa-based XALTER who built the VR training module for Targa Resources and Kodiak Gas Services. This VR compression skid is the latest in a series of midstream VR projects that XALTER has delivered to the gas industry.
In a May 2022 article entitled VR goes mainstream in compressor maintenance, we first shared details on a VR learning initiative being rolled out by Oklahoma State University Institute of Technology (OSUIT) to use VR in their natural gas compression program to complement the hands-on training students receive on real-world equipment.
OSUIT previewed their virtual gas compression skid at the 2021 GPA Midstream Convention as part of a multi-year, multi-million dollar partnership with energy sector employers whereby XALTER creates VR content that can be used both by OSUIT in the classroom and industry partners in the workplace. In our 2022 article, OSUIT Dean Bob Firth pointed to the learning advantages that VR provides plus anytime, anywhere learning to increase proficiency and mastery as key benefits of adopting VR in higher education. From an industry perspective, GPA Chairman and EVP at Targa Resources, Clark White went on to say that he believed that VR is the future of training and had already purchased a VR headset to become familiar with the technology.
Now fast-forward to 2023 and we’re seeing more midstream operators adopt VR for compressor training. This month, Targa Resources and Kodiak Gas Services will be rolling out the virtual gas compression skid shown at the GCA Convention & Expo to train operators and technicians on a CAT 3606 diesel engine and Ariel compressor. One of the many advantages of the VR compression skid is that it provides 24/7 access to training – ranging from first-time parts identification and procedures, to refresher and recertification training on common procedures. VR helps operators and technicians practice startup, shutdown, and LOTO procedures along with various preventative maintenance tasks in a “safe place to fail” without the risk of damaging real-world equipment or interrupting gas production.
Because the virtual compression skid allows hundreds of staff to simultaneously train via self-guided or instructor-led sessions, training throughput is no longer limited to how many operators or technicians can be gathered around a physical compressor or travel budgets. Additionally, training can be scheduled in near real-time as trainees can use a VR headset or laptop computer to access the training simulation – thereby eliminating weeks of training schedule delays.
Targa Resources and Kodiak Gas Services plan to use the virtual compression skid to complement existing real-world training to improve operator and technician proficiency while also measuring the impact of VR on test scores and first-time pass rates for competency assessments and certifications.
Operators who were given early access to Beta versions of the virtual compression skid early this year raved about its realism and ease of learning curve to interact in a virtual environment. The interest was so high that several asked for gamification aspects to be added to the VR training content including leaderboards to track competitions among themselves for bragging rights for time-to-completion of training tasks and training completion stats. This is hardly the reaction that traditional classroom and field training conjures up and reflects the needed changes in how we train today’s workers. As mentioned in our article last May, XALTER is quick to point out that VR doesn’t replace real-world learning – but it does increase practice repetitions so that learners are more familiar with parts/systems identification, process and procedures, and safety scenarios before being confronted with them in real-world situations.
One of the key safety concerns shared by Targa Resources was the process of servicing valves on the Ariel compressor. The spring tension on the valves creates a dangerous situation if improperly removed and a potential source of serious injury. While Ariel has built a nice video library for their customers to outline service and maintenance tasks, people learn by doing (active learning) – and this is especially true of today’s workforce. Millennials are now the largest generation in the workforce and they are digital natives – as are Gen Z workers as over half prefer to learn by doing, and only 12% learn effectively via classroom instruction.
“We are excited to be able to pilot VR as a training medium in 2023 and have high hopes for its adoption and use across our organization in the future. The timing couldn’t be better as we welcome a new Learning & Development leader to our team and the data captured from the VR pilot will be valuable in helping us evolve our learning strategies. I think there is a huge opportunity for OEMs to modernize their training by adopting VR to support key customers like us,” said Clark White, EVP at Targa Resources.
As mentioned previously, VR offers workers a “safe place to fail” as they practice compressor valve replacement and other critical operating and maintenance procedures before laying hands on expensive equipment in the field. What’s more, VR allows for randomized safety scenarios to be triggered that force operators to respond and those remediation actions can be timed and captured within the VR session and integrated directly into learning management systems (LMS) for richer data and better insight into operator and technician proficiency. Even eye tracking and hand tracking data can be captured to help technical training professionals assess and predict worker safety and performance.
The virtual compression skid learning module allows trainees to walk around and inspect the CAT 3606 diesel engine and Ariel compressor – just like in real life.
The CAT/Ariel compression skid is just one of multiple VR learning modules built by XALTER to support the energy sector as others include separation towers, a pig launcher/receiver, vapor recovery units, and others. What makes XALTER’s approach unique in the market is that they bring together technical colleges and private industry to co-fund the VR projects, thereby reducing the initial investment by up to 50%, while sharing expertise and data to fast-track each organization’s ability to learn how to use VR effectively. Other collaborations include a pig launcher/receiver that was designed in partnership with Energy Transfer and OSUIT and demonstrated at the GCA Expo & Convention. Additional VR projects include vendor/customer collaboration such as John Zink Hamworthy Combustion and Marathon Petroleum.
XALTER’s CEO Kevin Anderson explains it this way, “We realize that VR is an exciting new learning medium embraced by younger workers and training leaders. But most experienced energy executives have been disappointed before when a shiny new technology didn’t deliver on its promise. A measure of caution and skepticism is understandable. To gain the trust of energy sector executives, we structure our VR pilots and programs with clear learning and operational objectives, defined ROI metrics, and a focus on business outcomes measured in quarters, not years. By mitigating risk, sharing best practices across customers, and providing the necessary deployment support for adoption and use, we are helping more OEMs and operators take advantage of what VR can offer.”
For compressor OEMs and service companies interested in exploring VR, both XALTER and OSUIT say they are eager to collaborate.
MAGAZINE
NEWSLETTER
CONNECT WITH THE TEAM
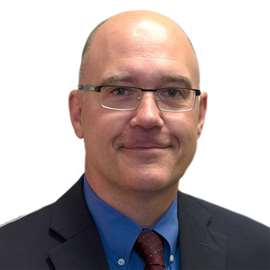
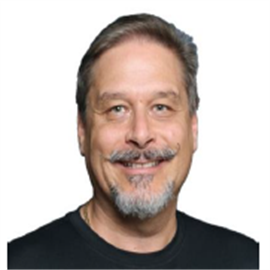
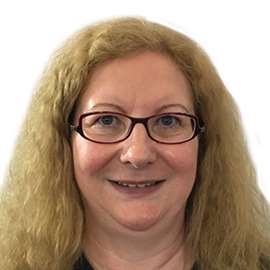
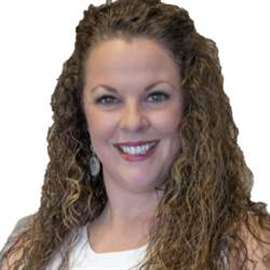