An electric equipment battery primer, part 1: traditional technologies
18 June 2024
Editor’s Note: the following was contributed as an exclusive to Power Progress by battery manufacturer EnerSys, Reading, Pa., and edited for length and style. It is part of a three-part series from EnerSys on understanding battery technology for electric equipment and vehicles.
The internal combustion engine (ICE) has been a reliable workhorse since it was patented over 200 years ago. However, the ICE is coming under increasing scrutiny due to legislative mandates about emissions, fluctuating fuel prices, costly engine maintenance requirements and even health concerns over emissions. As a result, many OEMs have increasingly been taking a battery-electric (BE) approach for equipment, such as forklifts and floor care equipment.
Over the last decade, the battery options in the market have expanded to meet a variety of applications for industrial equipment, from traditional lead acid batteries to more advanced options, such as lithium-ion and thin plate lead acid batteries.
To optimize a fleet’s performance, OEMs and equipment managers need to consider all aspects of the application before choosing the right battery. These considerations include power demands, length of equipment life, any equipment lease contract terms and space constraints for maintenance and spare battery storage.
This first in a three-part series of articles about the different battery technologies and their applications will explore the traditional flooded lead acid battery. This battery type is still a solid, proven, dependable technology used today for many different industrial vehicle and equipment applications. They have some performance limits but are still considered a great option for many fleets.
Lead acid intro
The traditional flooded lead acid battery consists of lead plates submerged in a liquid electrolyte solution. They were first used to power the lights in train carriages in the late 19th century. Today, they are the standard option for engine starting in on-highway vehicles, such as cars, trucks and motorcycles.
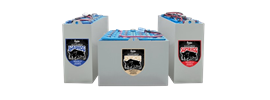
It wasn’t long before companies began testing batteries as a prime power source in industrial vehicles, and by 1906, the Pennsylvania Railroad introduced the first battery-powered platform trucks for moving luggage at a train station.
As flooded lead acid batteries became less expensive and more readily available in the 1990s, many major forklift manufacturers introduced new battery-powered machines for indoor material handling applications. The batteries are also commonly used to power floor care equipment and utility vehicles, such as electric carts, tow tractors and burden carriers.
Proven technology
Traditional flooded lead acid batteries are a popular choice for industrial equipment because they are the most proven battery technology. They are also lower in cost than other battery options and readily available from many battery manufacturers.
There are a variety of flooded lead acid batteries available, each offering different voltages, power outputs and capacities to meet specific application needs.
While they are highly dependable, these batteries do have some drawbacks, such as limited energy storage density, that make them better suited for lighter-duty applications.
Power density
Flooded lead acid batteries charge more slowly than other technologies. For industrial equipment and forklift applications, they are designed to run down to about a 20 percent charge level before needing 10 - 16 hours to fully recharge and cool.
For heavier-duty applications that cannot afford such charging downtime, batteries can be changed out between shifts. However, that is a time-consuming process that requires the purchase and storage of extra batteries.
More maintenance
Flooded lead acid batteries typically require a higher level of maintenance than more advanced battery technologies. For instance, water must be added weekly to the appropriate level. Over- or under-watering will cause damage and reduce battery life.
Additionally, they must be regularly equalized by charging to a higher-than-recommended voltage. This removes sulfate crystals that can build up over time. Inadequate equalization can cause crystal build-up that reduces battery capacity.
Because this maintenance can result in extended downtimes, many users choose to keep and maintain backup batteries.
Fast-charge options
Fast-charge flooded lead acid batteries were introduced in the 1970s as the go-to solution for heavy-use equipment. They feature the same technology as traditional lead acid batteries but use upgraded intercell connectors and other components to allow for faster, more aggressive charging.
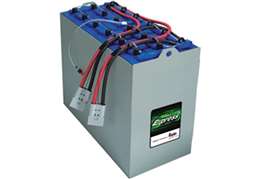
The initial cost of fast-charge batteries is usually a bit higher than their traditional counterparts. They are most effective when paired with express battery chargers, which also have a slightly higher cost than standard battery chargers.
However, fast-charge batteries allow users to make use of opportunity charging during work breaks and other stoppages, minimizing the need for the longer periods of charging required of traditional lead acid batteries.
Since fast-charge batteries endure more intense usage, proper maintenance is even more critical. For instance, they still require equalization and the addition of water. They also offer a lower energy density, making them best suited to medium-use applications.
Fast-charge batteries have an average life of 2 - 4 years depending upon their level of use and maintenance schedules. By comparison, a traditional flooded lead acid battery has a typical useful life of 3 - 6 years — again, dependent upon usage and maintenance.
Part 2 of this article series will discuss more advanced battery technologies.
MAGAZINE
NEWSLETTER
CONNECT WITH THE TEAM
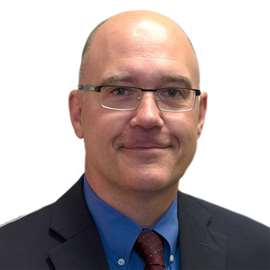
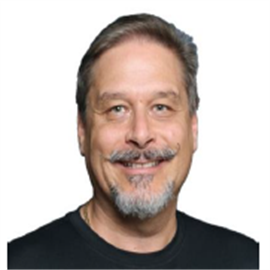
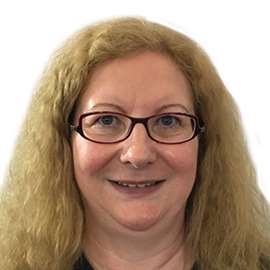